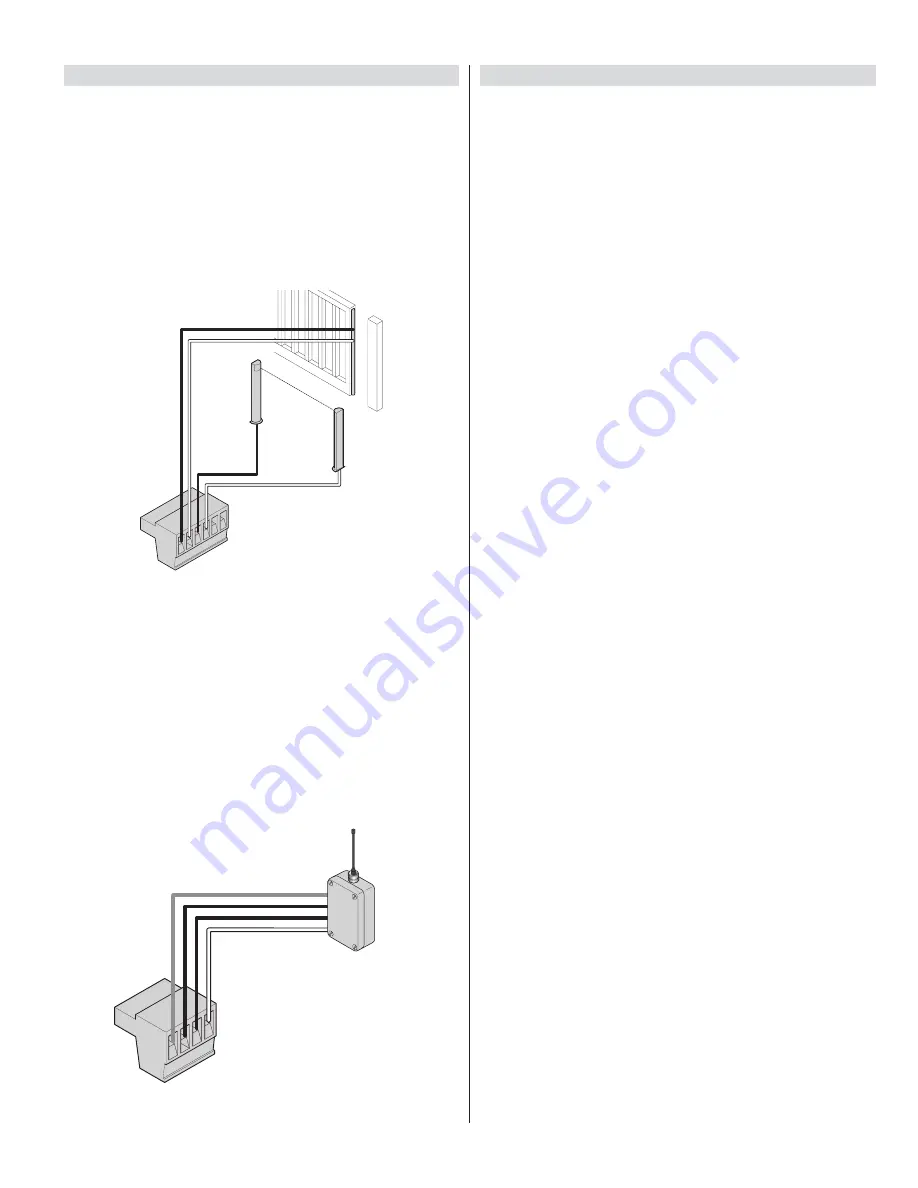
24
Proper inspection of all equipment is required to ensure continuous
functionality, safety and to ensure reliable operation in all weather conditions.
Inspect electrical assemblies and wiring installations for damage, general
condition, and proper functioning to ensure the continued satisfactory
operation of the electrical system. Adjust, repair, overhaul, and test electrical
equipment and systems in accordance with the recommendations and
procedures in the OPENER and/or component manufacturer’s maintenance
instructions.
Replace components of the electrical system that are damaged or defective
with identical parts, with manufacturer’s approved equipment, or its
equivalent to the original in operating characteristics, mechanical strength,
and environmental specifications. A partial list of suggested problems to look
for and checks to be performed are listed below:
18.1
Damaged, discolored, or overheated equipment, connections, wiring,
bearing caps and installations.
18.2
Excessive heat or discoloration at high current carrying connections.
(look for bluing or heat affected metal).
18.3
Misalignment of electrically driven equipment. (Causes strain on pulley
assemblies and bearings).
18.4
Poor electrical bonding (broken, disconnected or corroded bonding
strap) and grounding, including evidence of corrosion.
18.5
Dirty equipment and connections. Clean equipment and connections.
18.6
Improper, broken, inadequately supported equipment, wiring and
conduit, loose connections of terminals, and loose ferrules.
18.7
Poor mechanical or weld joints. Broken welds.
18.8
Condition of circuit breaker and fuses. Ensure that they are of the
correct type and amperage.
18.9
Insufficient clearance between exposed current carrying parts
and ground or poor insulation of exposed terminals. All exposed
connections must be covered (prevent arcing between exposed parts,
and electrical shock).
18.10
Broken or missing wire, connectors, etc.
18.11
Operational check of electrically operated equipment such as motors,
inverters, generators, batteries, lights, protective devices, etc. Ensure
proper functionality of all systems during inspections.
18.12
Ensure safety placards and warning signs are present as specified
within this document. Ensure proper functionality of all safety devices
as specified. Non-functioning or malfunctioning safety devices should
be replaced immediately.
17.5 - Exit and edge inputs wiring diagram
28 EDGE
29 GND
30 EXIT
31 GND
The EDGE input may be configured as a monitored ANALOG input, or
DIGITAL (NC or NO) input. The EDGE sensor input is intended for ANSI/UL
325 listed gate edge sensors to protect against entrapment and hazardous
pinch points along the moving edge of the closing gate. The EXIT sensor
input is provided to activate to open the gate, or re-open a closing gate, upon
sensing an exiting vehicle.
28
29
30
31
32
33
Figure 24 - EXIT AND EDGE INPUTS
17.6 - Radio receiver connection (third party)
38 12V
39 OPEN
40 CLOSE
41 GND
The customer supplied radio receiver allows the gate operator to be operated
via remote, such as wireless key-card readers or user remote controls.
Connecting the Open (39) and Close (40) pins together with a receiver
enables single-button gate control. This configuration allows a single button
to control the gate in the following sequence:
Press - Gate Open
Press - Gate Stop
Press - Gate Close
Press - Gate Stop
38
39
40
41
Figure 25 - RADIO RECEIVER CONNECTION
17 - OPTIONAL INPUTS (CONT.)
18 - INSPECTION AND OPERATION
Summary of Contents for Apollo 4300SW
Page 2: ......
Page 40: ...38 35 GATE ARM INSTALLATION Figure 33 CORRECT LAYOUT INCORRECT INSTALLATION Figure 34...
Page 44: ......
Page 45: ......