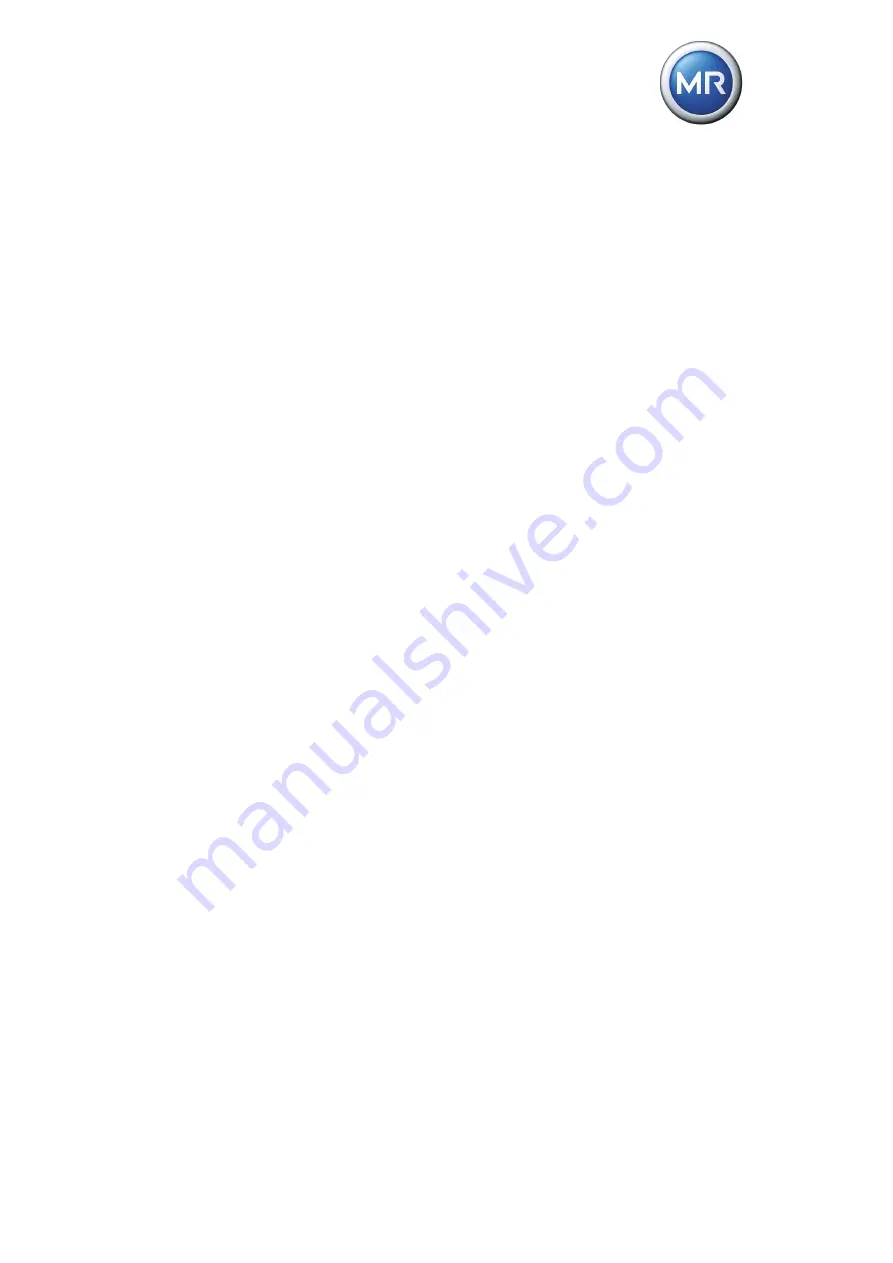
5 Mounting
© Maschinenfabrik Reinhausen 2012
2117246/02 EN
TAPCON® 230 basic
59
5.5 Function
check
Carry out a function check to test that the voltage regulator is wired correctly.
Check the following:
After being switched on, the screen displays the MR logo and then a vol-
tage value.
The green "Operating display" LED in the top left on the voltage regulator
lights up.
The voltage regulator can now be configured. The actions required for this are
described in the following
chapter
(see "
Commissioning
" on page 61).