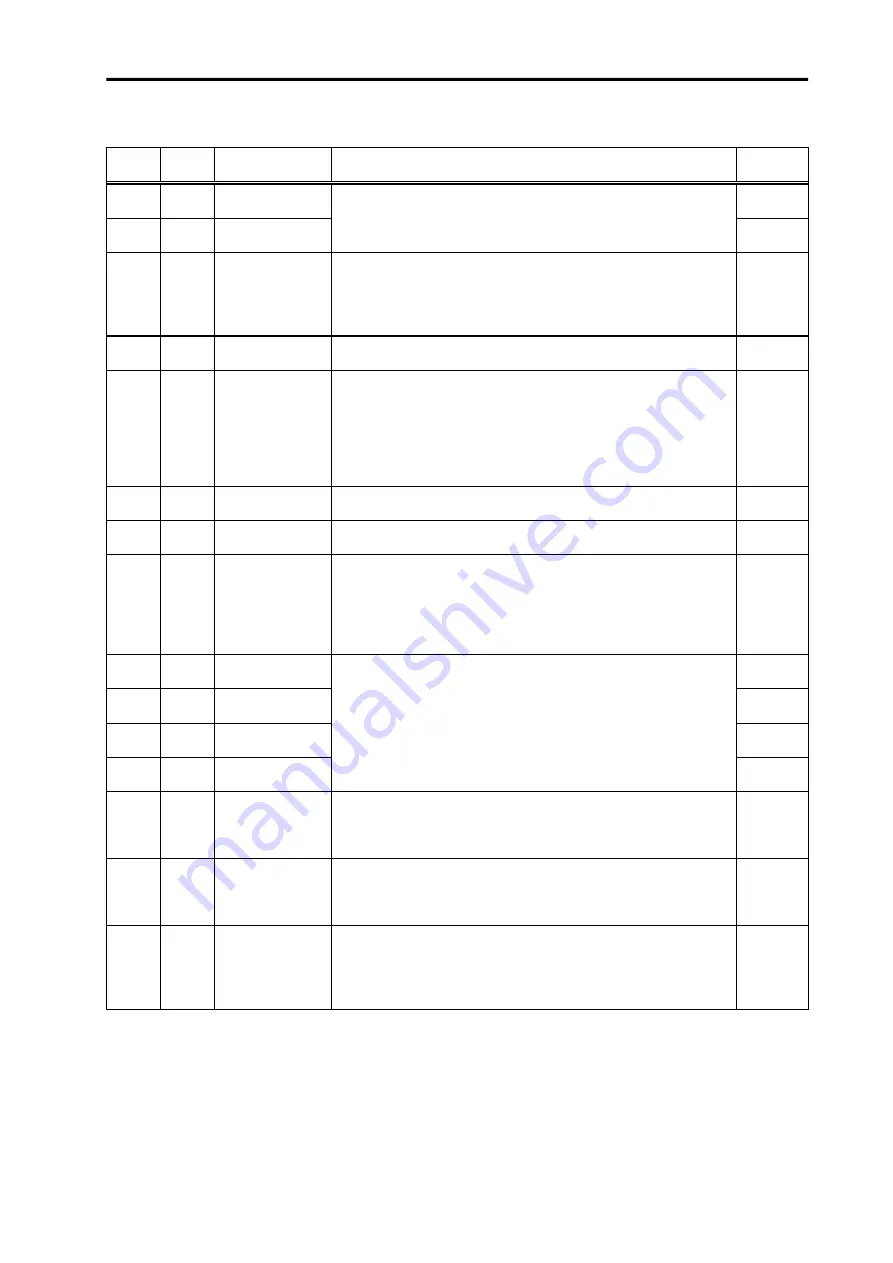
Chapter 5 Adjustment
5-33
5-6 Parameter list
No. Abbrev. Parameter
name
Explanation
Setting range
(Unit)
SV001 PC1*
Motor side gear
ratio
1 to 32767
SV002 PC2*
Machine side gear
ratio
Set the motor side and machine side gear ratio.
For the rotary axis, set the total deceleration (acceleration) ratio.
Even if the gear ratio is within the setting range, the electronic gears may
overflow and cause an alarm.
1 to 32767
SV003 PGN1 Position
loop gain 1
Set the position loop gain. The standard setting is “33”.
The higher the setting value is, the more precisely the command can be
followed and the shorter the positioning time gets, however, note that a
bigger shock is applied to the machine during acceleration/deceleration.
When using the SHG control, also set SV004 (PGN2) and SV057 (SHGC).
1 to 200
(rad/s)
SV004 PGN2 Position
loop gain 2
When using the SHG control, also set SV003 (PGN1) and SV057 (SHGC).
When not using the SHG control, set to “0”.
0 to 999
(rad/s)
SV005 VGN1 Speed loop gain
Set the speed loop gain.
Set this according to the load inertia size.
The higher the setting value is, the more accurate the control will be,
however, vibration tends to occur.
If vibration occurs, adjust by lowering by 20 to 30%.
The value should be determined to be 70 to 80% of the value at the time
when the vibration stops.
1 to 999
SV006
Not used. Set to “0”.
0
SV007
Not used. Set to “0”.
0
SV008 VIA
Speed loop lead
compensation
Set the gain of the speed loop integration control.
The standard setting is “1364”. During the SHG control, the standard
setting is “1900”. Adjust the value by increasing/decreasing it by about
100 at a time.
Raise this value to improve contour tracking precision in high-speed
cutting. Lower this value when the position droop vibrates (10 to 20Hz).
1 to 9999
SV009 IQA
Current loop q axis
lead compensation
1 to 20480
SV010 IDA
Current loop d axis
lead compensation
1 to 20480
SV011 IQG
Current loop q axis
gain
1 to 2560
SV012 IDG
Current loop d axis
gain
Set the gain of current loop.
As this setting is determined by the motor’s electrical characteristics, the
setting is fixed for each type of motor.
Set the standard values for all the parameters depending on each motor
type.
1 to 2560
SV013
ILMT
Current limit value
Set the normal current (torque) limit value. (Limit values for both + and -
direction.)
When the value is “500” (a standard setting), the maximum torque is
determined by the specification of the motor.
0 to 500
(Stall [rated]
current %)
SV014 ILMTsp
Current limit value
in special control
Set the current (torque) limit value in a special control (initial absolute
position setting, stopper control, etc). (Limit values for both of the + and -
directions.)
Set to “500” when not using.
0 to 500
(Stall [rated]
current %)
SV015 FFC
Acceleration rate
feed forward gain
When a relative error in the synchronous control is large, apply this
parameter to the axis that is delaying. The standard setting value is “0”.
For the SHG control, set to “100”.
To adjust a relative error in acceleration/deceleration, increase the value
by 50 to 100 at a time.
0 to 999
(%)
Parameters with an asterisk * in the abbreviation, such as PC1*, are validated when the NC power is turned ON again.
Summary of Contents for MELDAS MDS-B-SVJ2 Series
Page 1: ......
Page 2: ......
Page 4: ......
Page 6: ......
Page 46: ......
Page 92: ......
Page 108: ......
Page 152: ......
Page 186: ......
Page 194: ......
Page 218: ......
Page 260: ......
Page 282: ......
Page 283: ...12 1 Chapter 12 Inspections 12 1 Inspections 12 2 12 2 Life parts 12 2 ...
Page 294: ......
Page 297: ......