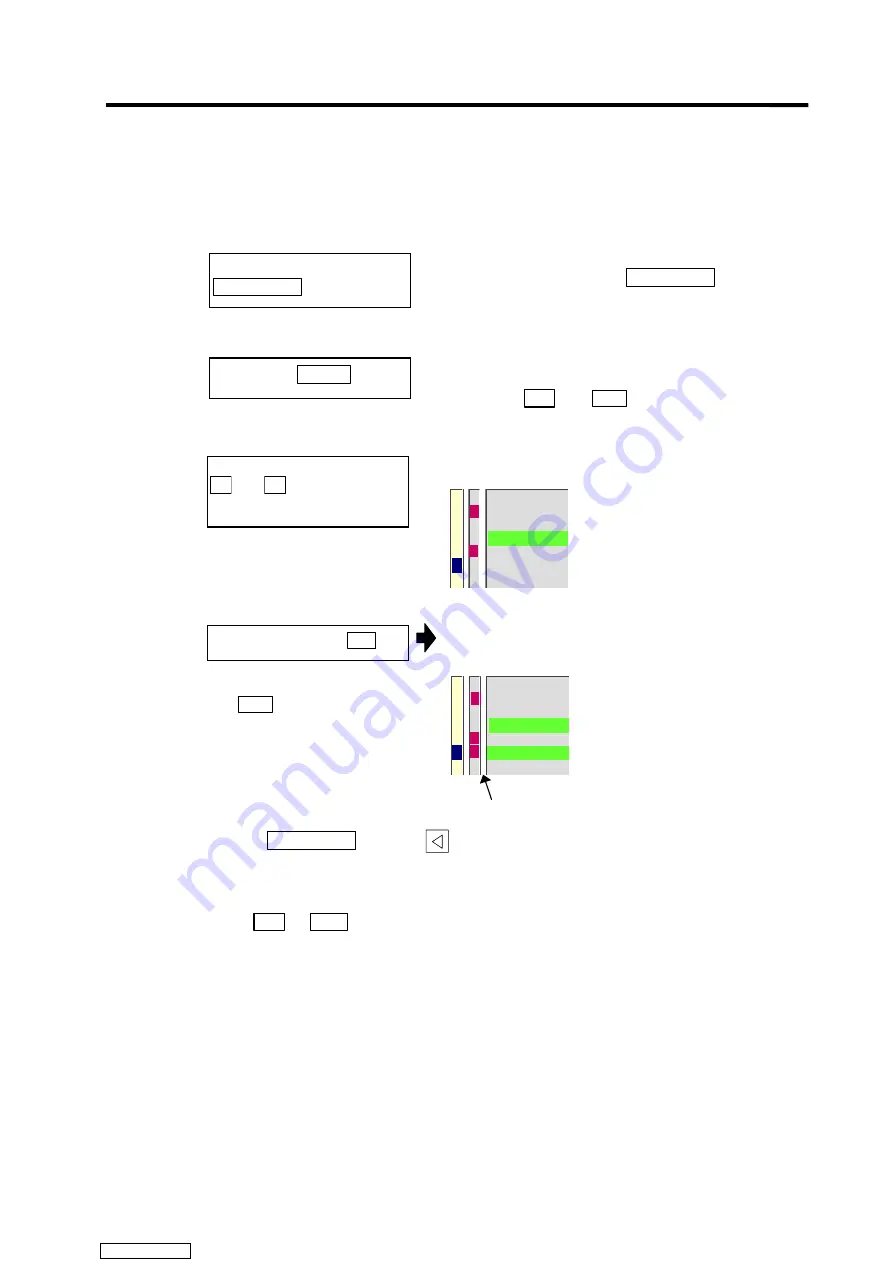
CHAPTER 1 SCREEN OPERATIONS
2. Monitor (Operation) Screens
I
– 101
2.9.1 Turning PLC switches ON/OFF
(1) Operation method (To turn switch "#6 Program restart" ON)
1)
A message confirming the start of PLC switch setting
will appear. The menu key Setting valid will be
highlighted.
2)
The PLC switch setting mode will be entered. The
cursor will appear at the PLC switch No. position. The
menu keys ON and
OFF
will appear normally.
3)
The #6 number is highlighted.
# Name
Auto restart
Protect delete
Manual/Absolute
Optional stop
Handl interrupt
Program restart
*
*
1
2
3
4
5
6
7
4)
The "#6 Program restart" switch turns ON, and a
∗
mark
appears.
# Name
Auto restart
Protect delete
Manual/Absolute
Optional stop
Handl interrupt
Program restart
*
*
1
2
3
4
5
6
7
*
(Note 1)
If the Setting valid menu or
key is pressed again during the PLC switch setting
mode, the PLC switch setting mode will be canceled.
(Note 2)
The PLC switch setting mode will be canceled when another screen is opened.
(Note 3)
The cursor will not appear in modes other than the PLC switch setting mode. If the menu
key ON or OFF is pressed in this state, a message indicating that the mode is not the
PLC switch setting mode will appear.
Press the menu key
Setting valid .
Press "Y" or INPUT .
Press the cursor keys
↑
and
↓
to move the
cursor to "#6".
Press the menu key
ON
.
A
∗
mark appears.
To turn OFF, press the menu
key
OFF
.
Downloaded from
Summary of Contents for MELDAS 600M Series
Page 15: ...CHAPTER 1 SCREEN OPERATIONS Downloaded from ManualsNet com search engine ...
Page 333: ...CHAPTER 2 MACHINE OPERATIONS Downloaded from ManualsNet com search engine ...
Page 386: ...CHAPTER 3 MAINTENANCE Downloaded from ManualsNet com search engine ...
Page 442: ...CHAPTER 4 APPENDICES Downloaded from ManualsNet com search engine ...