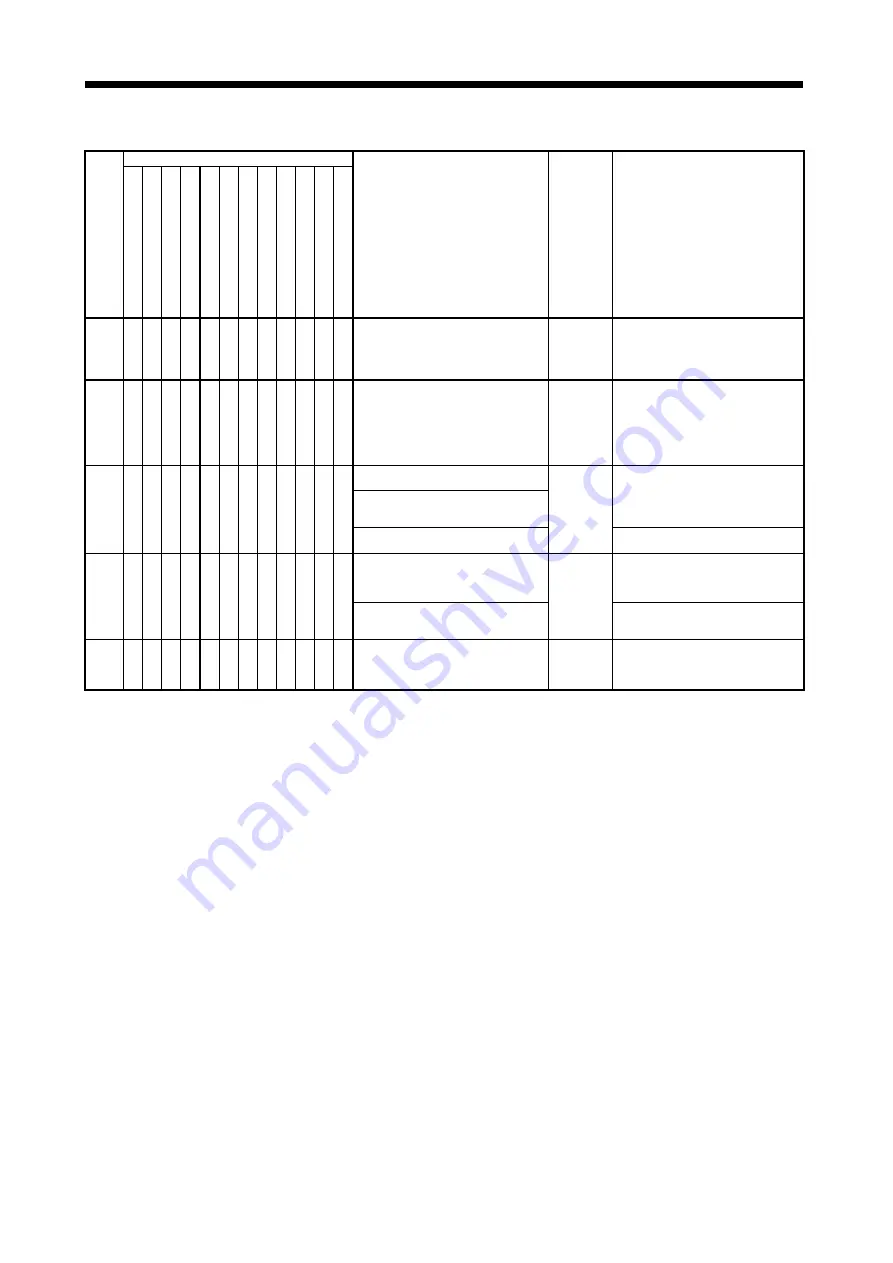
APPENDICES
APP
−
14
Table 2.5 Positioning Control Error List (200 to 299) (Continued)
Control Mode
Error
Code
Po
s
it
io
n
in
g
F
ixed
-P
itch
F
e
ed
Sp
e
e
d
S
p
eed
/P
o
sitio
n
S
witch
in
g
S
p
eed
S
witch
in
g
C
o
n
s
tan
t-S
peed
JOG
M
a
n
u
a
l P
u
lse Gen
e
ra
to
r
Ze
ro
in
g
P
o
sitio
n
F
o
llo
w-Up
Co
n
tr
o
l
OS
C
Error Cause
Error
Processing
Corrective Action
211
!
•
During positioning, an overrun occurs
because the deceleration distance for the
output speed is not attained at the point
where the final positioning address is
detected.
Axis motion
decelerates
to a stop.
•
Set a speed at which overrun does not
occur.
•
Set a travel value which will not cause an
overrun.
214
!
•
An attempt was made to control an axis
already being moved by the manual pulse
generator by setting the manual pulse
generator operation enable flag for that axis.
The manual
pulse
generator
input is
ignored until
the axis
stops.
•
Perform the manual pulse generator
operation after the axis has stopped.
•
The speed switching point address is more
than the end point address.
•
An address to control positioning in the
opposite direction was set during speed
switching control.
•
Set the speed switching point within the
range from the previous speed switching
point address to the end point address.
215
!
•
The same servo program was been
executed a second time.
A rapid stop
is executed.
•
Modify the sequence program.
•
In position follow-up control, when the
control unit is "degrees", a command
address outside the 0 to 35999999 has
been set.
•
When the control unit is "degrees", set a
command address within the range 0 to
35999999.
220
!
•
The command address has exceeded the
stroke limit range in position follow-up
control.
Axis motion
decelerates
to a stop.
(M2001+n
OFF)
•
Set an address within the stroke limit
range.
225
!
•
In constant speed control, the speed at the
pass point exceeds the speed limit value.
The speed is
kept at the
speed limit
value.
•
Set a speed command value between 1
and the velocity limit value.