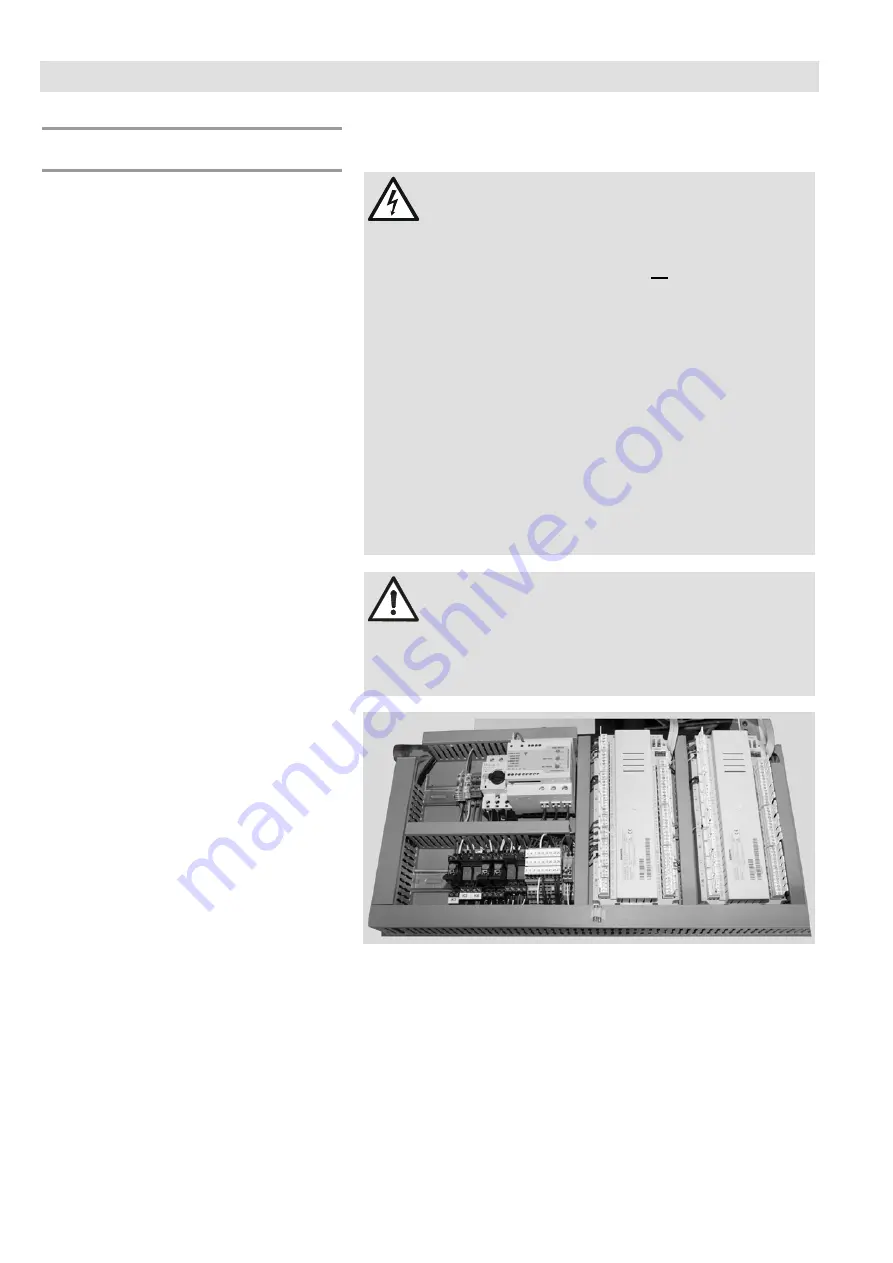
6. Assembly
ThermSelect®
52/100
6.6 Electrical
connection
DANGER!
Risk to life through electrical current!
Contact with live components can cause serious inju-
ries.
Therefore:
-
When working on the device, all supply lines must
be without current.
-
Make sure that all electrical parts are without cur-
rent.
-
The applicable VDE and utility company regulations
as well as the respective regulations and guidelines
of the country of destinations must be complied
with.
-
The electrical connections must be inspected by a
responsible technician before establishing the con-
nection with the line supply.
-
An external separator (e.g. main switch) must be
envisaged for all electrical supply lines to the ma-
chine.
-
Only operate the heat pump within the implementa-
tion frequency (s. chapter 5.3 Type of electricity for
compressor) (in Germany 50 Hz).
CAUTION!
Interferences through electrical fields!
Supply lines (230 V) may interfere with sensor lines
(electrical low voltage).
Therefore:
-
Sensor and supply lines may not be routed in the
same cable conduit.
Fig. 17:
Overview of electric connections
Summary of Contents for ThermSelect
Page 1: ...ThermSelect As of 9 March 2011...
Page 22: ...5 Technical Data ThermSelect 22 100 5 2 Identification plate Fig 4 Sample identification plate...
Page 25: ...ThermSelect 5 Technical Data 25 100...
Page 31: ...ThermSelect 5 Technical Data 31 100...
Page 45: ...ThermSelect 6 Assembly 45 100 Fig 10 Sensor cable heat source inlet 5...
Page 72: ...8 Maintenance ThermSelect 72 100 8 4 Spare part drawing and legend Fig 37...
Page 96: ...Your notes ThermSelect 96 100...
Page 97: ...ThermSelect Your Notes 97 100...
Page 98: ...Your notes ThermSelect 98 100 12 Index...
Page 100: ...Your notes ThermSelect 100 100...