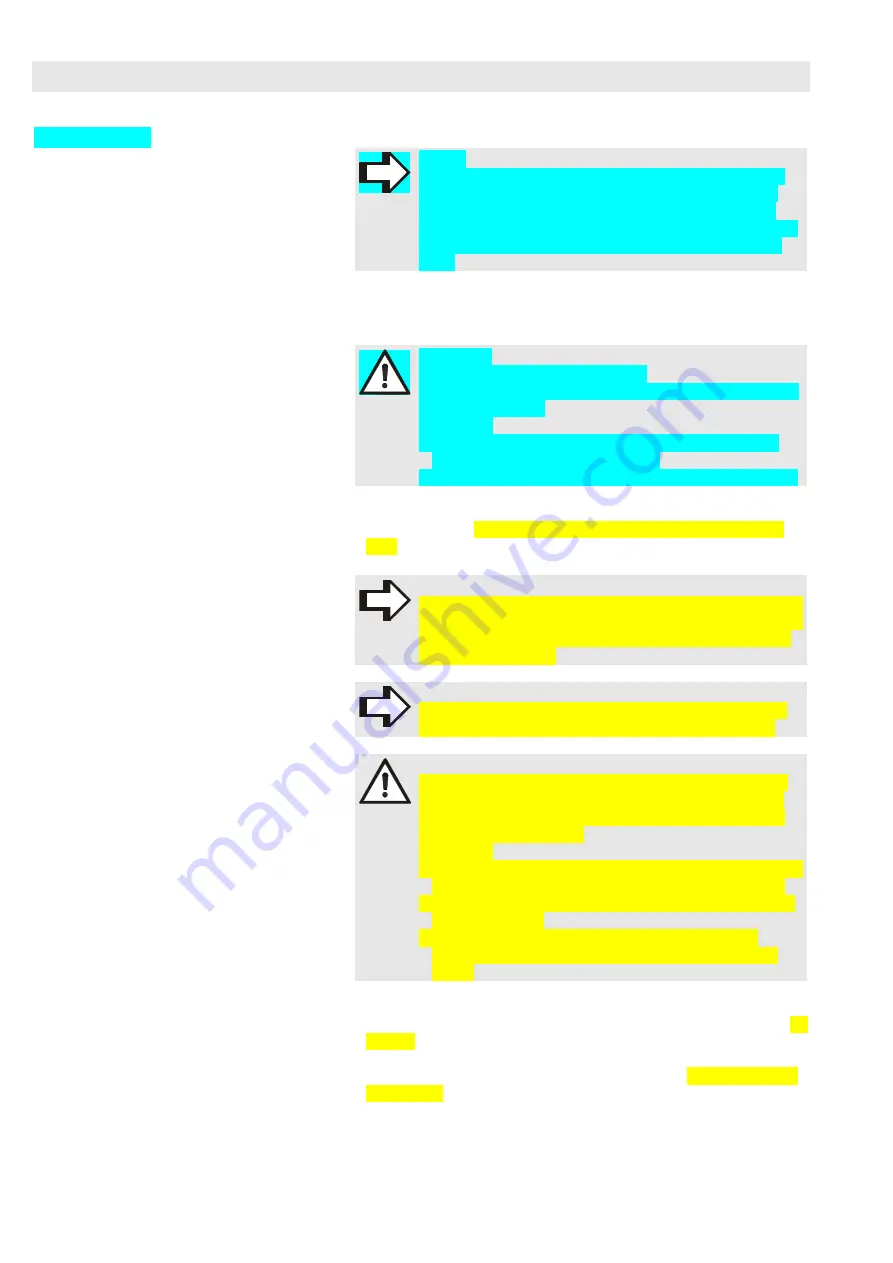
6. Assembly
ThermiStar L .. SP 01/03/10
36
Welding work
NOTE!
If any welding work is scheduled on the refrigerant
line, a protective gas (i.e. nitrogen) will need to be
passed through the pipe in order to prevent scale
formation. Scale and other contamination can impair
the proper operation of the device leading to disor-
ders.
Assembly of the split evaporator
CAUTION!
Risk of injury due to refrigerant!
Refrigerant is corrosive and causes cold burns upon
contact with skin.
Therefore:
-
Wear chemical-resistant protective gloves when
handling refrigerant at any time.
-
Wear protective glasses to avoid contact with eyes.
-
The location of the evaporator must always be higher than the
heat pump unit (ensure proper gradient when installing cooling
lines).
NOTE!
Install the split evaporator in flow direction parallel to
the property boundary (not towards the neighbouring
plot) in order to reduce noise transmission to neigh-
bouring properties.
NOTE!
Ensure that no plants or objects are located in flow
direction in order to guarantee efficient operation.
CAUTION!
Device damage due to improper installation of cool-
ing lines or improper positioning of the evaporator.
Mechanical damage to the device can occur due to
insufficient lubrication.
Therefore:
-
Dimensioning and installation of cooling lines must
be carried out by technicians authorised by MHG.
-
The length of the cooling line may not exceed 15m
single distance.
-
The gradient of the cooling line from the split
evaporator to the heating pump may not exceed
1.5 m.
-
The line dimensions are matched exactly to the capacity of the
heat pump (line length between heat pump and split evaporator up
to max. 20 m). Altered line routing and clearances between heat
pump and split evaporator must be agreed upon with MHG since
the pipe dimensioning changes. Long line paths extend the thaw-
ing process and are to be avoided.
-
The lines are insulated with diffusion-proof material. The gaps of
the insulation must be glued.
Summary of Contents for 98.30000-6324
Page 1: ...ThermiStar L SP 01 03 10 ...
Page 18: ...5 Technical Data ThermiStar L SP 01 03 10 18 5 2 Type plate Fig 4 Sample type plate ...
Page 21: ...ThermiStar L SP 01 03 10 5 Technical Data 21 ...
Page 39: ...ThermiStar L SP 01 03 10 6 Assembly 39 Fig 11 Sensor cable heat source intake 5 ...
Page 68: ...8 Maintenance ThermiStar L SP 01 03 10 68 8 4 Spare part drawing and legend Fig 40 ...
Page 88: ...Your notes ThermiStar L SP 01 03 10 88 ...
Page 89: ...ThermiStar L SP 01 03 10 Your notes 89 ...
Page 90: ...Your notes ThermiStar L SP 01 03 10 90 ...
Page 92: ......