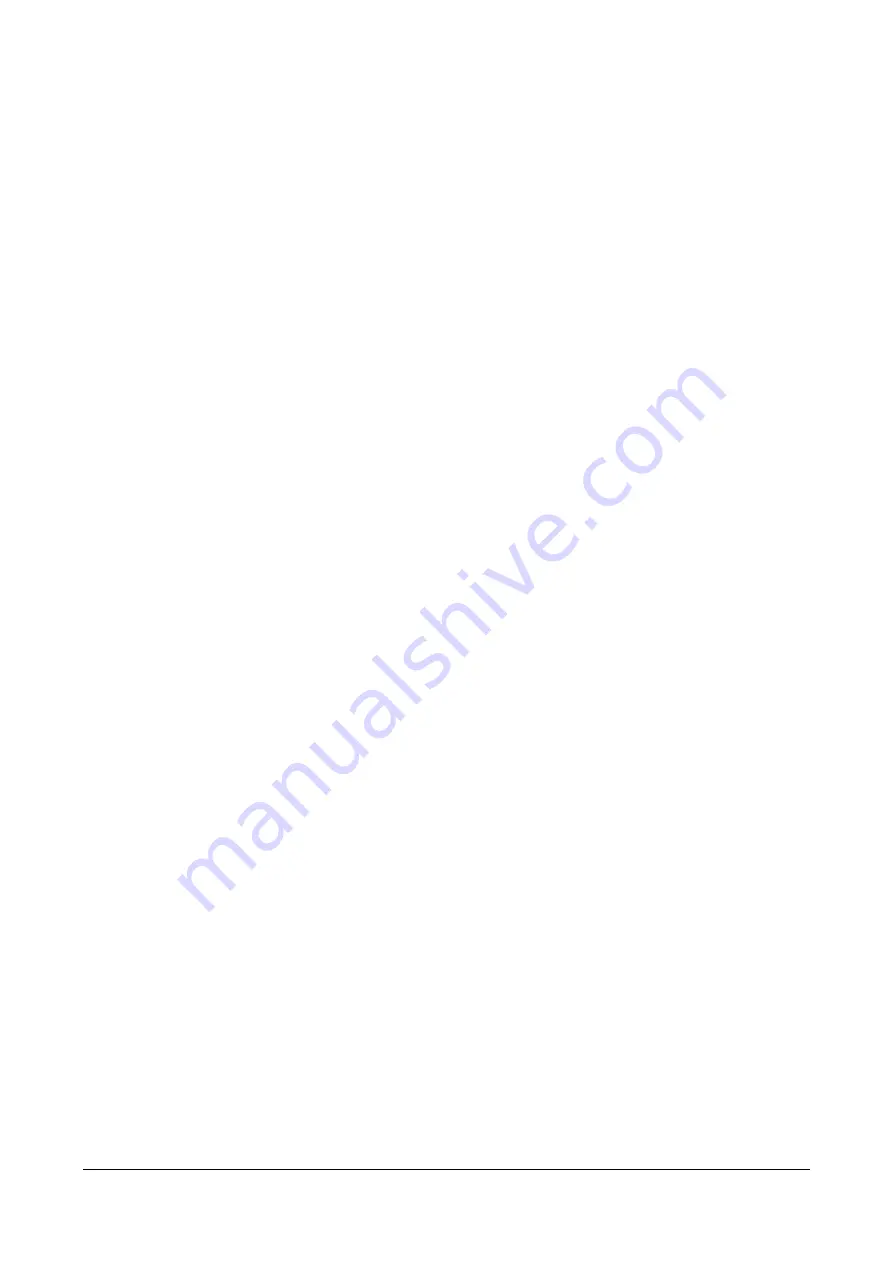
BA550001-en
57
If necessary, the brake must be readjusted as described in the section
"Adjusting the pit jack brake".
12.3.5
Pre-filter
Pneumatically operated pit jacks have a pre-filter at the compressed air inlet,
which is necessary to protect the control unit.
To check, disassemble the compressed air coupling and remove the hexagonal
threaded pin behind it. The filter can now be removed and checked for dirt and
damage. If necessary, clean using compressed air or replace if damaged, see
spare parts list.
12.4
Yearly inspection
Depending on the operating conditions, the lift must be inspected at intervals of
no more than 12 months. In particular, safety equipment, fastenings and load-
bearing components must be inspected.
This inspection must be carried out by a competent person in order to ensure
safe operation until the next inspection.
The inspection and its findings must be documented.
Irrespective of these regulations, the following inspection points must be
checked at least every 12 months and corrected if necessary.
12.4.1
Screw connections
All fastening screws on the pit jack and chassis must be checked and tightened
using a torque wrench.
The tightening torques can be found in the corresponding section in the
appendix.
12.4.2
Rollers on pit jack and FG
Rollers on the pit jack and chassis must be checked as described in section
"Rollers" and replaced if necessary.
Summary of Contents for MPJ Series
Page 6: ...6 BA550001 en Blank page...
Page 13: ...BA550001 en 13 6 Technical data 6 1 Relevant pit dimensions...
Page 29: ...BA550001 en 29 10 mm...
Page 35: ...BA550001 en 35...
Page 39: ...BA550001 en 39 I F H G J A E C D K B...
Page 114: ...20 PL670000_002 de...