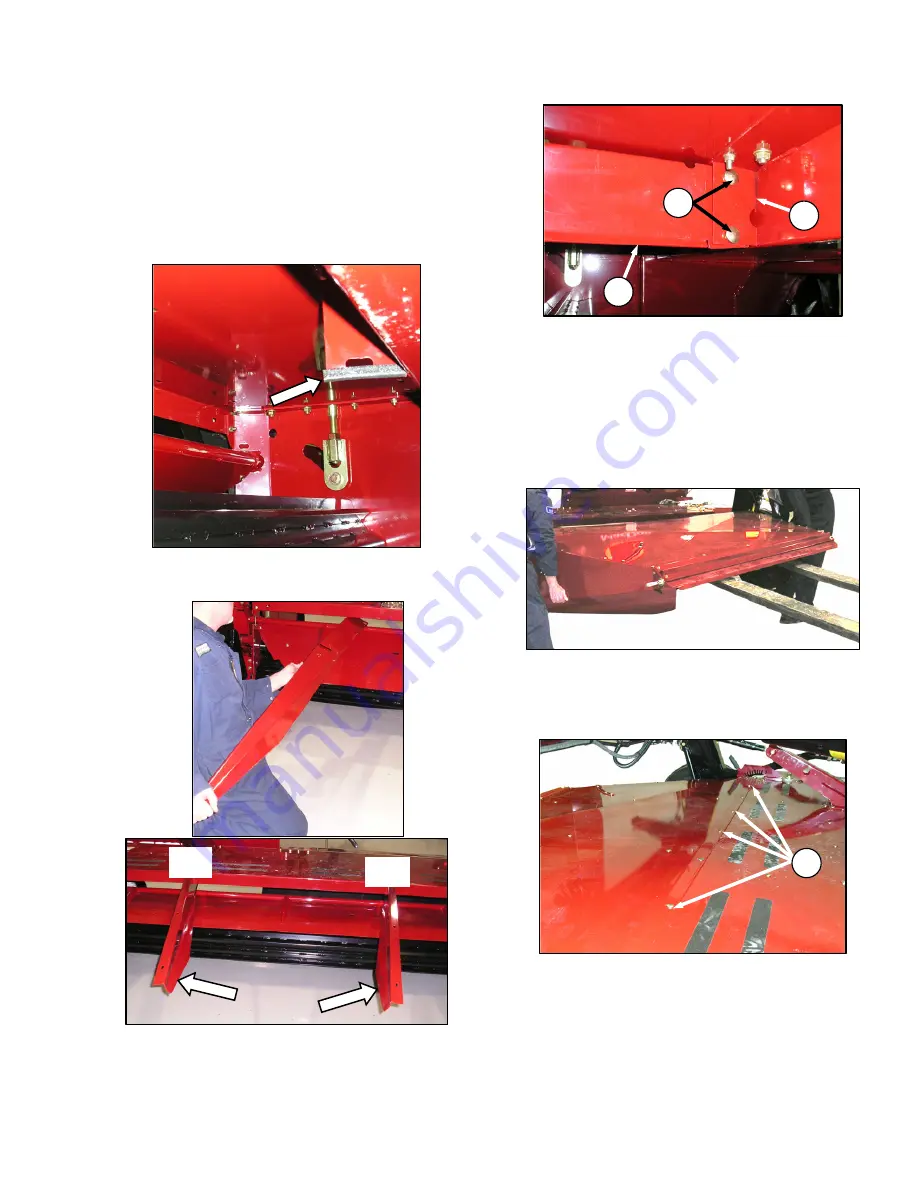
UNLOADING AND ASSEMBLY
Form # 169080
Model Year - 2010
31
STEP 20. INSTALL FORMING
SHIELD
A. INSTALL SUPPORTS
a. Remove supports and hardware bag that were
removed from shipping locations in earlier
steps.
b. Remove protective moulding from behind
cutterbar doors (2 places).
c. Insert support from rear of header as shown.
The supports are handed and lower flanges
must face each other.
d. Locate support (A) on outboard side of mounting
bracket (B).
e. Retrieve two ½ x 1.0 lg. carriage bolts (C) and
locknuts from hardware bag and secure suppport
to bracket. Do not fully tighten bolts.
f.
Repeat for other support.
B. ATTACH FORMING SHIELD
a. Place forming shield on lift forks and position
forming shield adjacent to supports.
b. Slide forming shield onto supports and back fork
lift away.
c. Locate shield to align holes in forward row. Install
four 3/8 x 0.75 lg. bolts and nuts in forward row at
locations (D) to hold shield. Nuts on inside. Do
not tighten.
(continued next page)
LH
RH
A
B
C
D