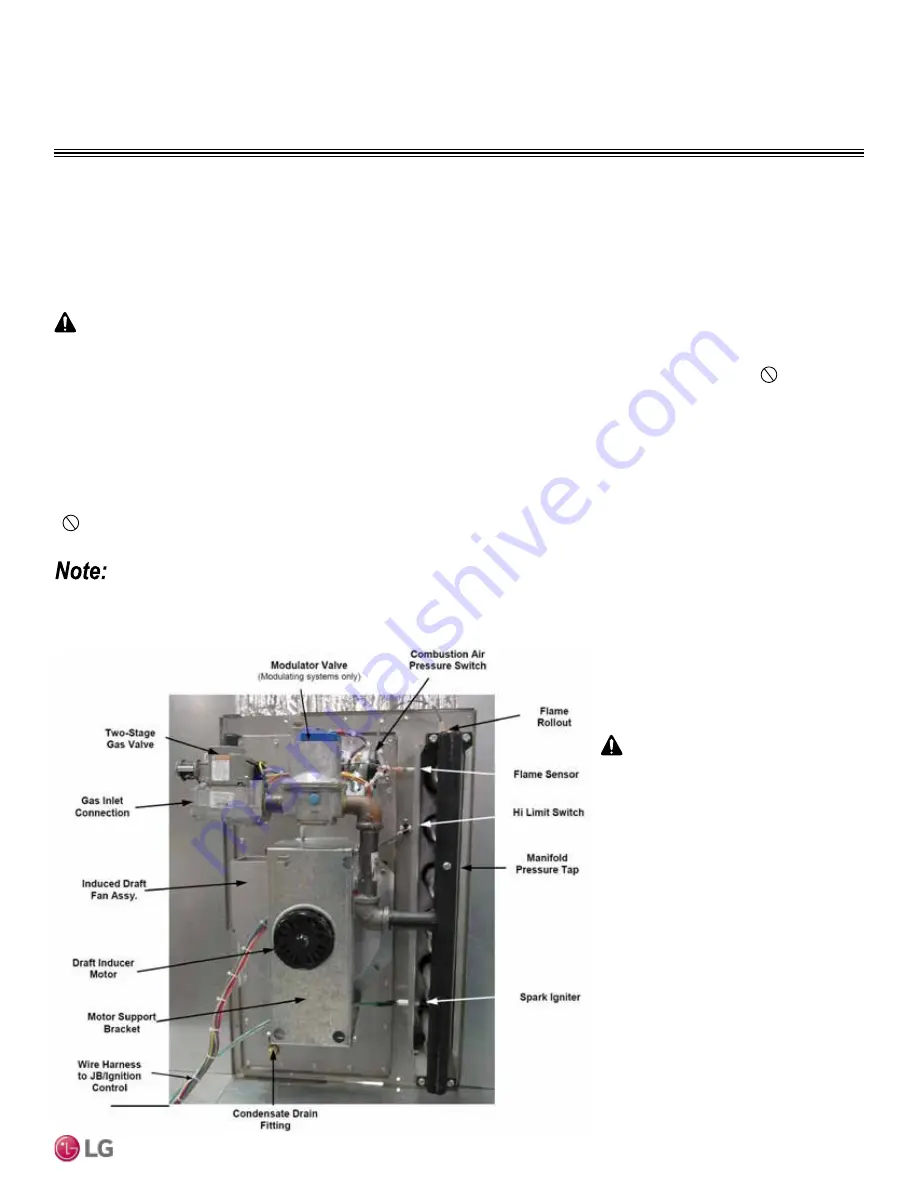
35
Installation
Due to our policy of continuous product innovation, some specifications may change without notification.
©LG Electronics U.S.A., Inc., Englewood Cliffs, NJ. All rights reserved. “LG” is a registered trademark of LG Corp.
GAS HEATER CONNECTION AND STARTUP
Pressure Testing the Gas System
• When test pressures exceed 14 in. w.c., the heater must be disconnected from the supply gas piping.
• When test pressures are 14 in. w.c. or less, the heater must be isolated from the supply gas piping by closing its individual manual shutoff valve.
• The gas pressure to the unit must be checked to make sure that the gas pressure does not fall out-side of the maximum and minimum
allowable gas pressures listed on the unit nameplate.
DANGER
Carbon monoxide is a lethal, colorless, odorless gas.
Fuel gas poses a danger of explosion which can cause personal injury, product damage, or property damage.
Do not use
matches, candles, flame, of other sources of ignition to check for leaks.
Gas-fired equipment is designed to provide safe, controlled combustion. The installer must ensure that the correct amount
of supply combustion air and a properly operating vent system is provided. If the installation does not permit the burner to
receive the proper supply of combustion air, complete combustion may not occur and carbon monoxide may be produced.
For your safety, if you smell gas:
Check both the supply lines and factory piping for leaks. Apply a soap and water solution to all piping and watch for bubbling. Some soap used for
leak detection are corrosive to some metals. Carefully rinse to remove soap and clean the pipe after leak test is completed.
• Open windows.
•
Don’t touch electrical switches.
• Extinguish any open flame.
• Vacate the area.
• Immediately call your gas supplier.
DANGER
The use and storage of gasoline or other flam
-
mable vapors and liquids in open containers in
the vicinity of the furnace is hazardous. There is
a risk of fire, explosion, physical injury or death.
Figure 43:
Furnace Module Component Description.