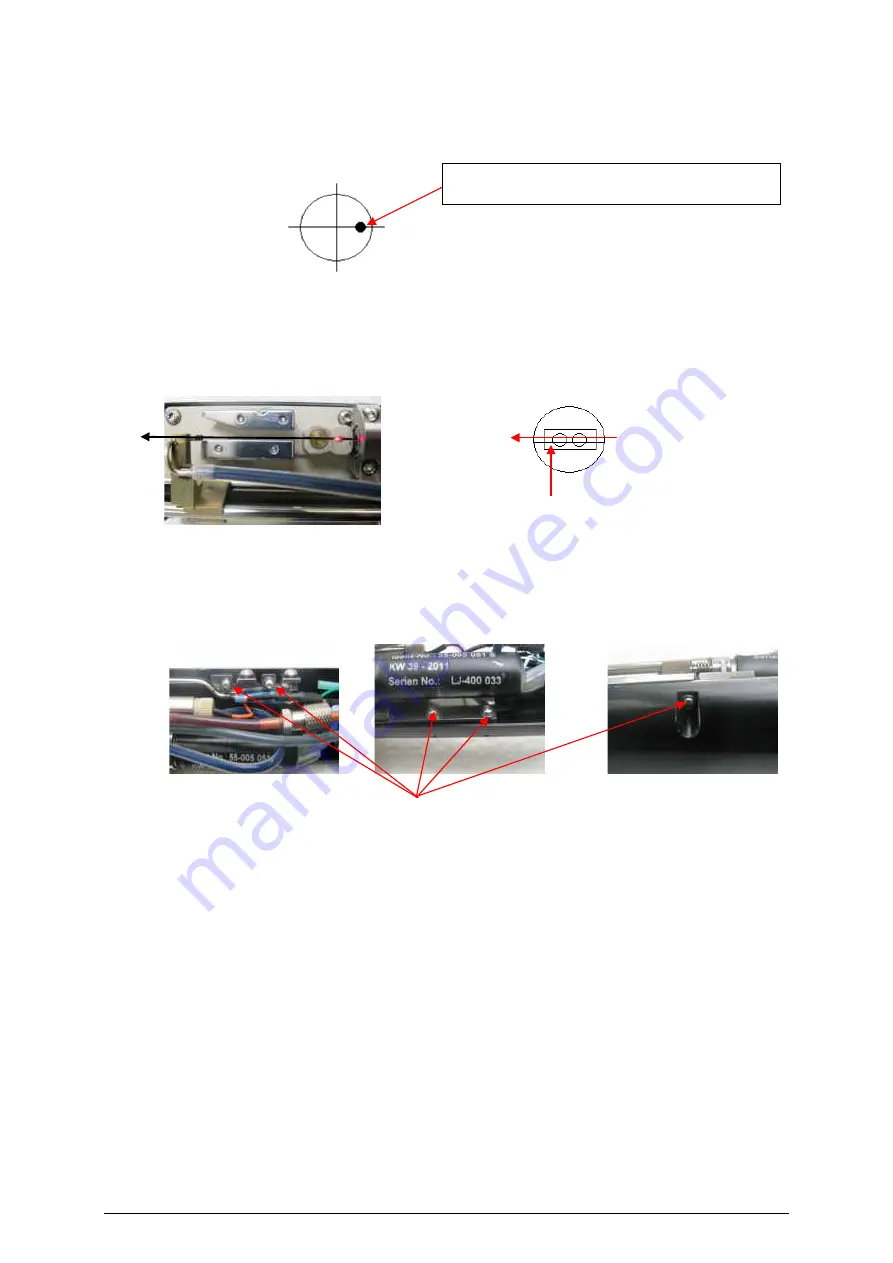
Page 56 of 61
6. Adjust the ink jet just like in the sketch below. The sketch shows the view from nozzle to gutter.
The ink jet is adjusted by moving the oscillator body, which is connected, to the nozzle retainer.
See picture above. When the ink jet is in the correct position, fix the screws again.
7. After the ink jet adjustment, it may be necessary to adjust the entire drop production unit in order
to make sure that the ink jet passes in parallel to the inner edges of the charging tunnel. To avoid
parallax faults you need to point your perspective exactly vertical to the charging tunnel.
inner edge of the charging tunnel
8. To adjust the drop production unit you need to untighten the five attachment screws of the fixing
plate just so far that you can move the unit manually. After adjusting the unit, fix the attachment
screws and check the position of the ink jet.
Ink jet position in gutter tube
Attachment screws