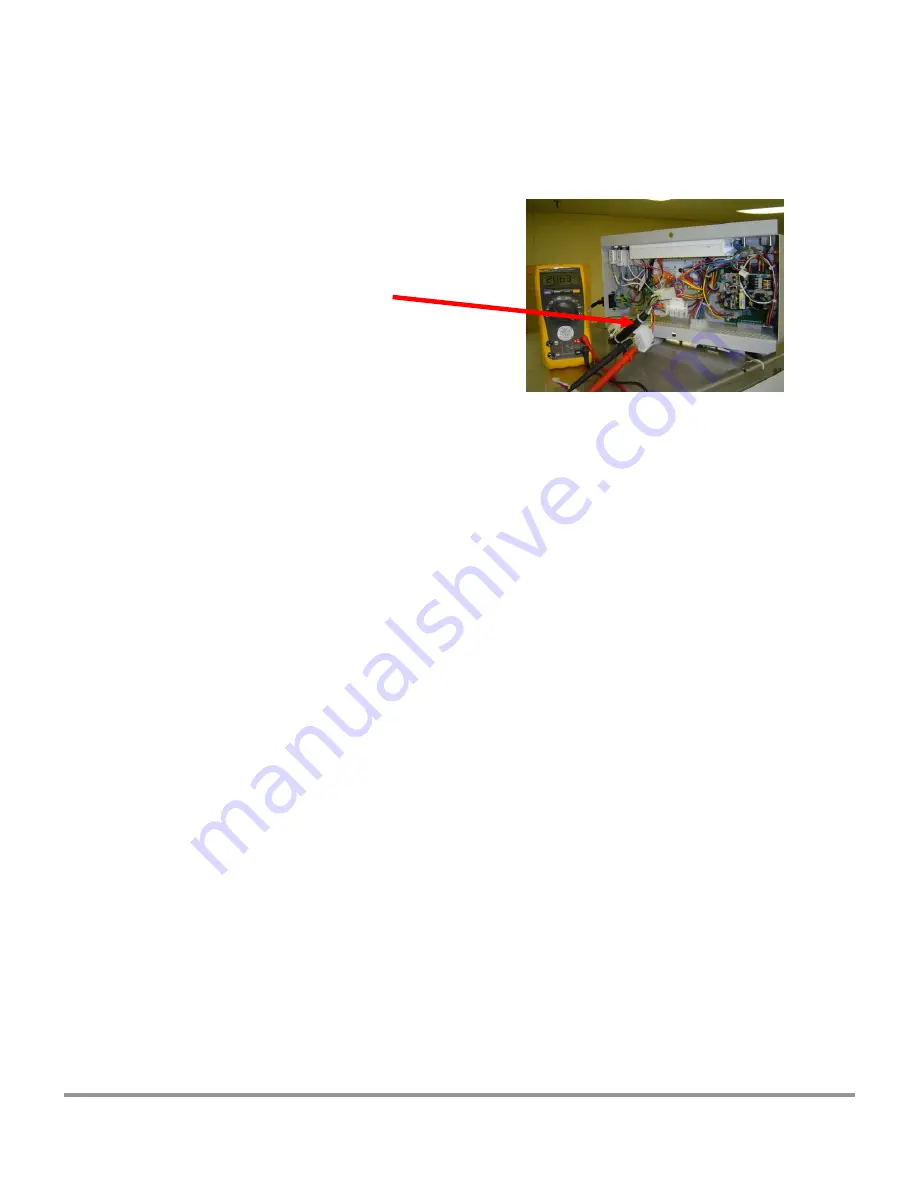
Product Service 1-800-522-7658
131
6.
Next, connect the DC voltage lead to pin 6 (yellow wire) and verify
there is ± 24 Volt DC ± 5 Volts DC, as shown in Figure 7-10. The presence of
24 Volt DC on this yellow wire tells the motor to start.
Figure 7-10
Measuring 24 VDC voltage
7.
Next, move the meter’s + DC voltage lead to pin 5 (purple wire) [the meter’s lead
is still connected to pin 8 (brown wire)]. Note the DC voltage, since the motor’s
speed is determined by the pulse width modulated signal on this contact. A
voltage noted in step 6 signifies 100% pulse width duty cycle, while a DC voltage
of 0 volts would indicate a 0% PWM level. Depending on the particular ECM
motor, the motor speeds for the 0% PWM levels and 100% PWM levels will differ
but the 0% level represents the “night setback” blower speed and the 100% level
indicates the max speed ever required by the motor under total filter loading. The
actual DC voltage measured will be between 0 V and 24 Volts DC, and that voltage
indicates roughly the % duty cycle being sent to the motor at this time. For
example:
A total voltage of 22 VDC, and a signal voltage of 15 VDC would indicate 15 VDC
measured/22V DC @ 100% = 68% duty cycle.
Another example, would be 18 VDC/22 DC @ 100%, would correspond to an 81%
PWM signal.