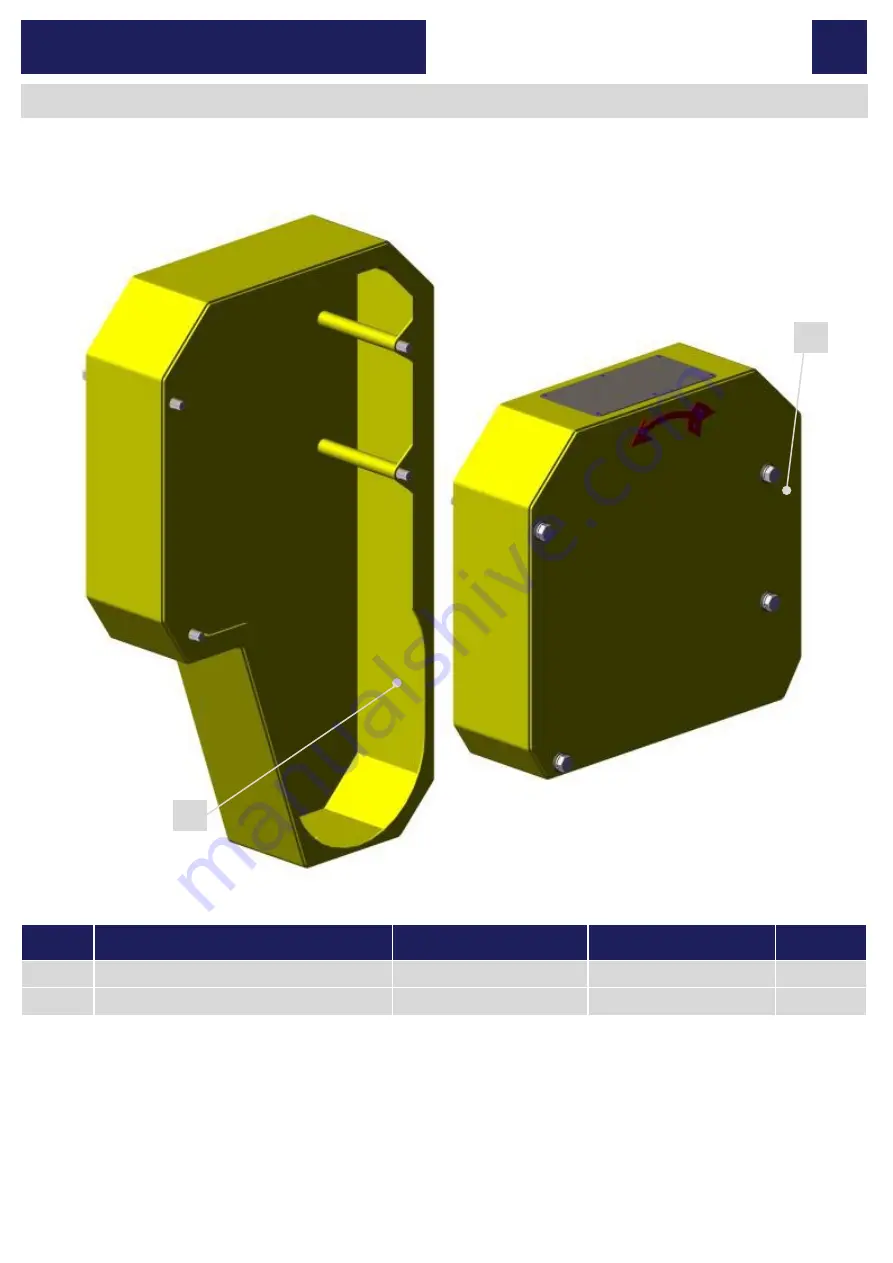
LMFC250 FINE CRUSHER MANUAL
Item
Description
Item No. / Type
Supplier
Quantity
24
Drive side cover
012
-
002
-
061
LAARMANN
1
25
Fly wheel cover
012
-
002
-
060
LAARMANN
1
The Parts List, quantities and location of parts which may be required for use on the LMFC 250 Drive Side and Flywheel
Covers.
9.3.2
Parts of the Drive Side & Flywheel Covers
1
2
3
4
13
16
5
12
14
6
9
10
11
8
7
17
15
25
24
Fig 13. Drive side & flywheel covers.
5
5
5
40