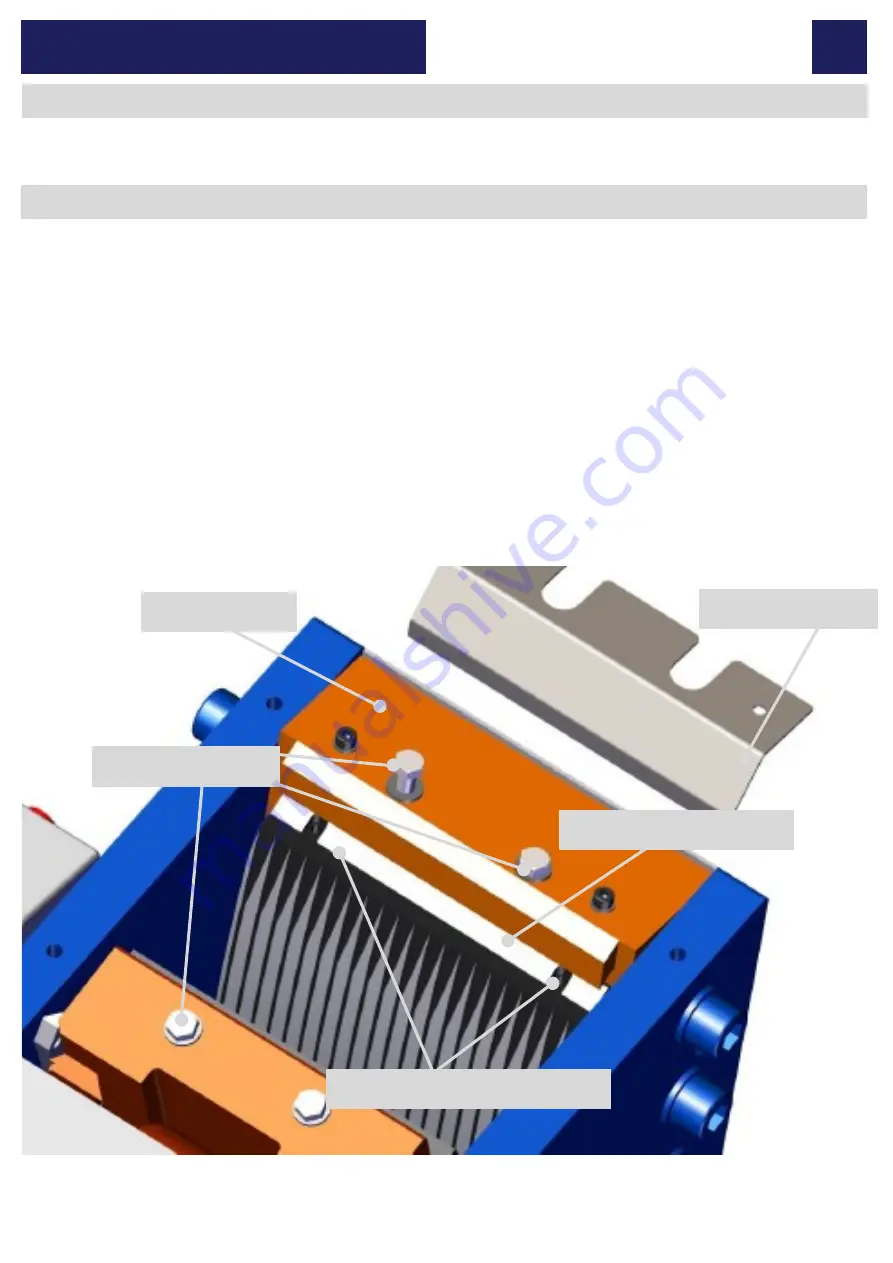
Check there is no blockage in the feed hopper. Isolate power to clear any blockage and check that the sample size is correct,
no larger than 110 mm. On top of the LMFC250 there is a feeder mounted, transporting the ore towards the LMFC250.
LMFC250 FINE CRUSHER MANUAL
6.5.5
Required jaw gap unattainable –
Replacing Jaw Plates
Follow the steps, if the required jaw gap is unattainable and the jaw plates and/or side liners need to be replaced or rotated.
Step 1:
Ensure the machine is isolated from power, remove the hopper, material deflective plate and flywheel cover and clean
the jaw plate area of the machine.
Step 2:
Turn the flywheel by hand to open the jaw gap to its maximum opening.
Step 3:
Remove the side liner plates by simply levering them free and lifting them out from their position in the frame.
Step 4:
loosen, but do not remove the four (4) long M12 draw bolts in the fixed front jaw plate and the pitman moving jaw pla-
te. Turn out one bolt, of the front fixed jaw plate, completely and then screw it back in three (3) full turns. Undo the other bolt,
but stop when the head of the first bolt drops down to reach the top of the front body plate. The front fixed jaw plate and the T
clamp supporting it have now been lowered to allow removel of the jaw plate.
Step 5:
Repeat Step 4 above for the moving jaw plate to enable removal.
6.5.4
Material not feeding into Crusher
Front Body Plate
Jaw Plate Draw Bolts
Material Divert Plate
Jaw Plate has dropped down
Bolt holes for Jaw Removal Eyebolts
Fig 6. Loosening jaw plate draw bolts.
5
5
5
29