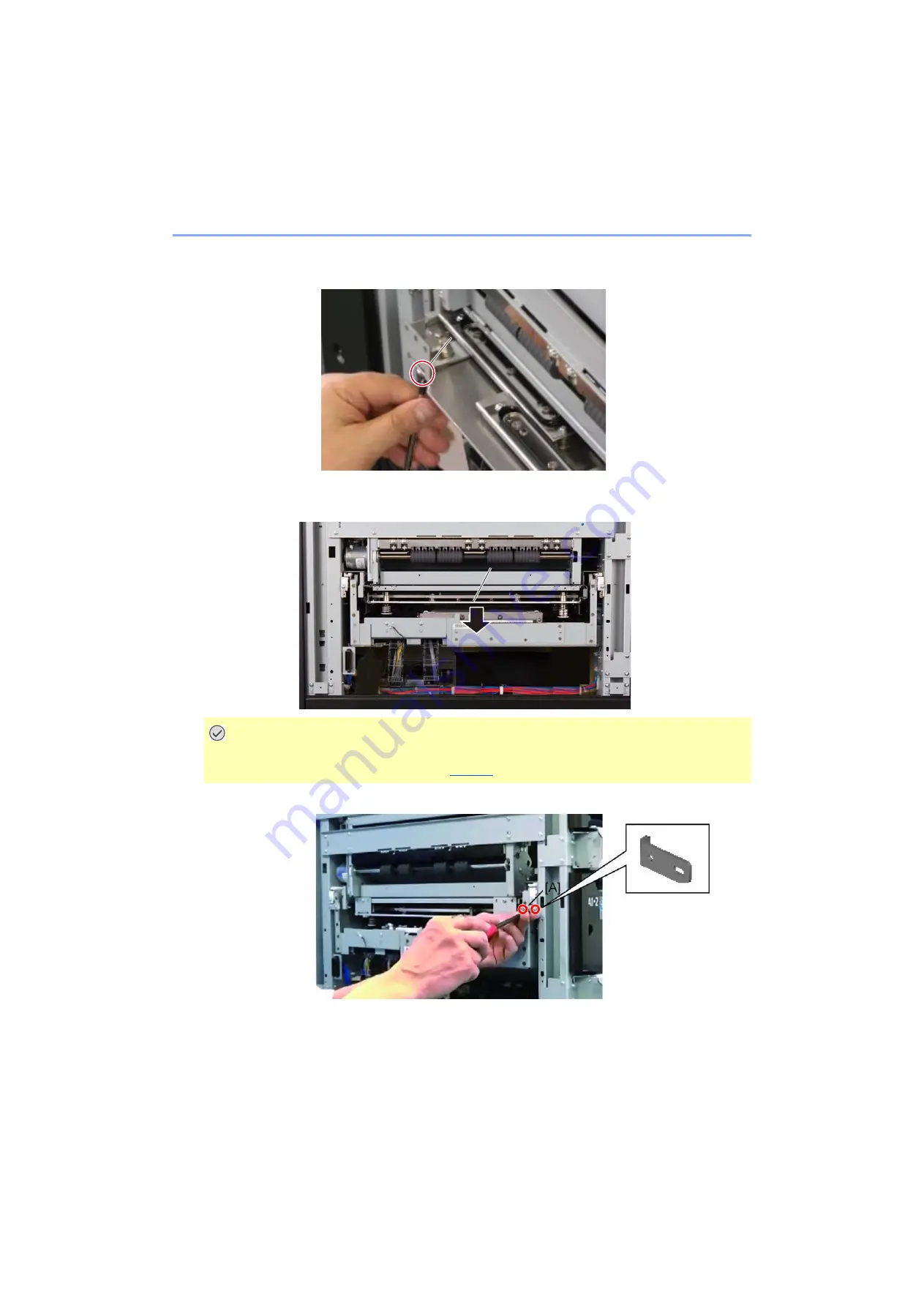
6-37
Machine transportation after setup > Procedure for the main unit transportation (Truck transportation)
[CONFIDENTIAL]
20
Remove the screw from the lower side of cap rear plate [A] with a screwdriver then
remove the plate. (Screw x1)
21
Re-install the cap unit [A] until you feel a click.
•
Confirm if the center of the shaft [B] matches with center of position [C].
22
Remove the treatment front plate [A]. (Screw x2)
IMPORTANT
If forgetting to remove the cap plate, C2100 will occur.
C2100: Treatment carriage HP sensor error (See
for the corrective action of service call)
[A]
[A]