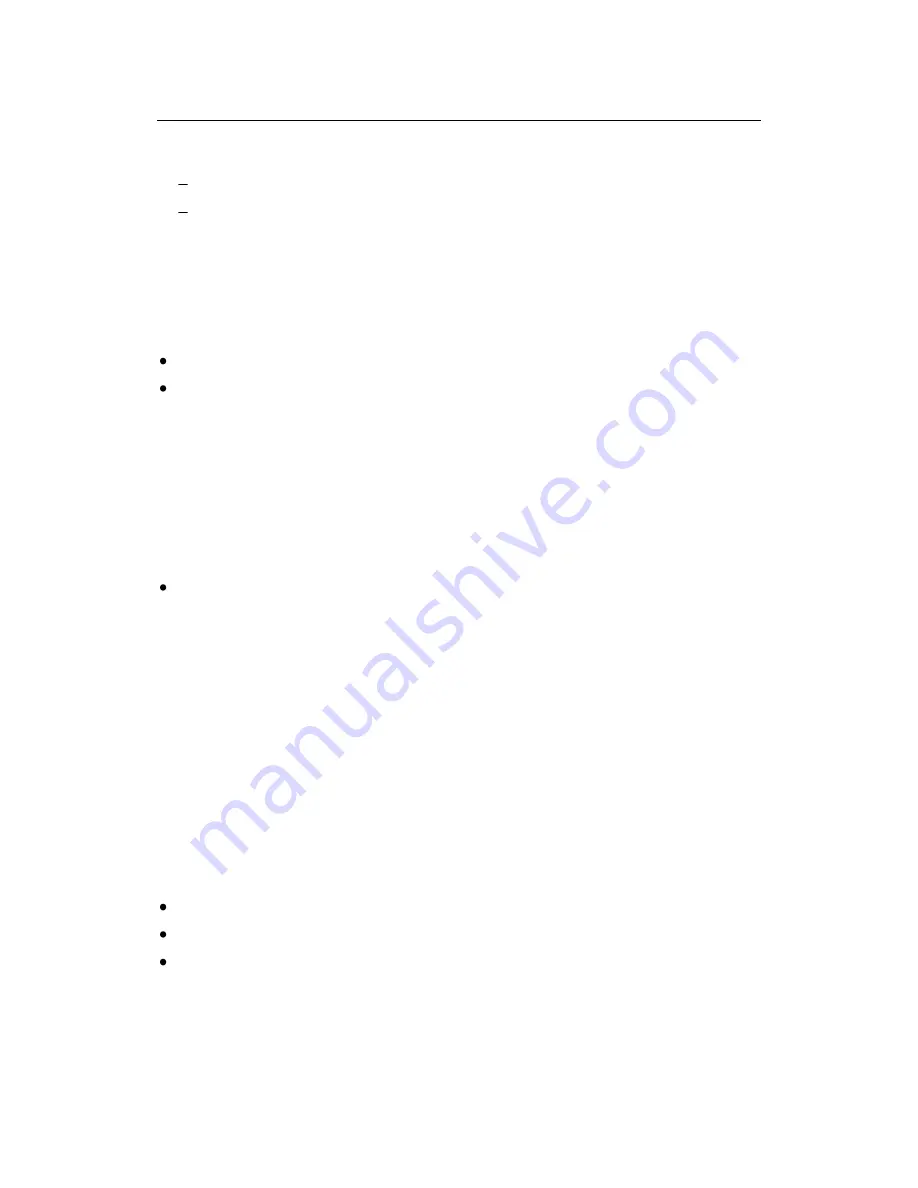
Seapath 320
32
M300-62/rev.2
Pitch
Roll
Pitch and Roll mounting angles should ideally be confirmed against MRU logs, for
instance during Gyro calibration.
3.3.3
GNSS antennas
The following is to be surveyed:
Position (X,Y,Z), centre of the antenna #1 disc (or otherwise defined sensor point).
Angular offset between the line from centre antenna #1 to centre antenna #2 and the
vessel centre line (CL).
Note
This offset should be confirmed against a Seapath GPS heading log,
typically during gyro calibration.
3.3.4
Gyro
If a gyro compass is interfaces to the Seapath system, the following is to be surveyed:
The offset between the gyro compass heading and the vessel centre line (CL).
Note
The heading offset to be surveyed to an accuracy better than 1°.
Static gyro calibration/verification (heading log) and DGNSS health check should be
done after all DGNSS and gyro systems are installed and fully operational. This can be
performed in dock or alongside.
Dynamic gyro calibration/verification and attitude control (heading, roll, pitch control)
must be performed at sea.
3.3.5
Survey accuracy
The Seapath 320 product must be surveyed to the following accuracy level. If not, the
performance of the product will be degraded.
Lever arm vector from CRP to GNSS antenna position (X, Y, Z): < 0.1 metre.
Lever arm vector from CRP to MRU (X, Y, Z): < 0.1 metre.
MRU 5 misalignment angles (Roll, Pitch, Yaw) with the vessel axes: < 0.1°.
Summary of Contents for Seapath 320
Page 1: ...Seapath 320 Installation Manual ...
Page 20: ...Seapath 320 4 M300 62 rev 2 ...
Page 42: ...Seapath 320 26 M300 62 rev 2 ...
Page 98: ...Seapath 320 82 M300 62 rev 2 ...
Page 100: ...Seapath 320 84 M300 62 rev 2 5 1 Processing and HMI Units ...
Page 101: ...Installation Manual M300 62 rev 2 85 ...
Page 102: ...Seapath 320 86 M300 62 rev 2 5 2 Antenna bracket ...
Page 103: ...Installation Manual M300 62 rev 2 87 5 3 MRU and mounting bracket ...
Page 104: ...Seapath 320 88 M300 62 rev 2 ...
Page 105: ...Installation Manual M300 62 rev 2 89 5 4 MRU junction box ...
Page 107: ...Installation Manual M300 62 rev 2 91 5 6 6 U cabinet dimensions ...
Page 108: ...Seapath 320 92 M300 62 rev 2 ...
Page 126: ...Seapath 320 110 M300 62 rev 2 ...
Page 127: ...Installation Manual M300 62 rev 2 111 ...
Page 128: ...Seapath 320 112 M300 62 rev 2 ...
Page 129: ...Installation Manual M300 62 rev 2 113 ...
Page 130: ...Seapath 320 114 M300 62 rev 2 ...
Page 133: ...Installation Manual M300 62 rev 2 117 APPENDIX D COAX CABLE SPECIFICATION ...
Page 134: ...Seapath 320 118 M300 62 rev 2 ...
Page 135: ...Installation Manual M300 62 rev 2 119 APPENDIX E RG 214 SPECIFICATIONS ...
Page 136: ...Seapath 320 120 M300 62 rev 2 ...
Page 152: ...Seapath 320 136 M300 62 rev 2 ...