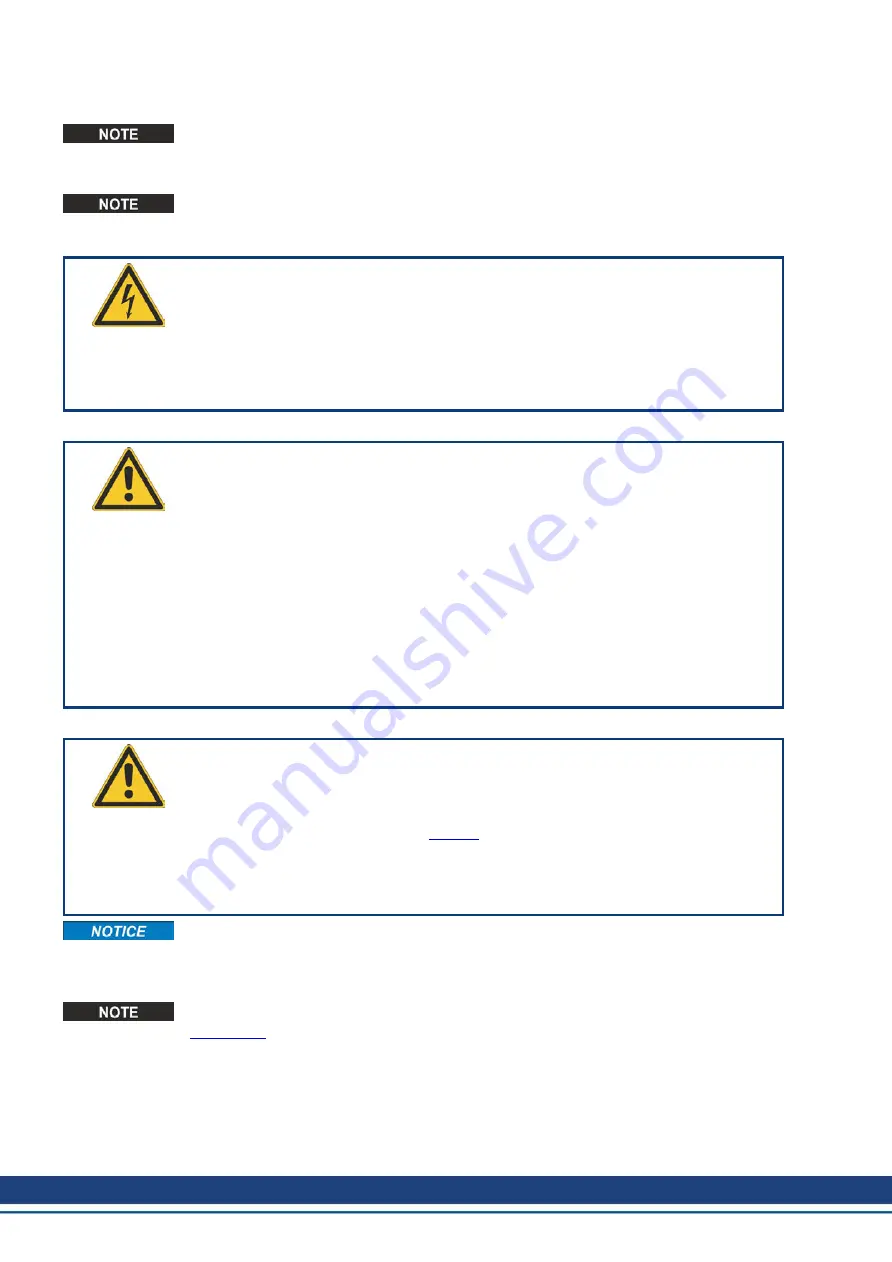
S700 Safety Guide | 2 English
2.6 Setup
For step-by-step setup guidance refer to the
Instructions Manual
.
2.6.1 Important Notes
Before testing and setup, the manufacturer of the machine must generate a risk assessment
for the machine and take appropriate measures so that unforeseen movements cannot cause
injury or damage to any person or property.
DANGER
The equipment produces potentially lethal voltages up to 900 V. Risk of
electric shock. Only professional personnel with extensive knowledge in
the fields of electrical engineering and drive technology are allowed to
test and set up the servo amplifier. Check that all connection components
that are live in operation are safely protected against bodily contact.
WARNING
There is a danger of electrical arcing when disconnecting connectors,
because capacitors can still have dangerous voltages present up to 10
minutes after switching off the supply power.
Risk of burns and blinding. The contacts become damaged.
Never undo any electrical connections to the servo amplifier while it is
live. Wait at least 10 minutes after disconnecting the servo amplifier from
the main supply power before touching potentially live sections of the
equipment (e.g. contacts) or undoing any connections.
To be sure, measure the voltage in the DC Bus link and wait until it has
fallen below 60V.
WARNING
The drive might restart automatically after power on, depending on the
parameter setting. Risk of death or serious injury for humans working in
the machine. If the parameter
is set to 1, then place a warning sign
to the machine (Warning: Automatic Restart at Power On) and ensure, that
power on is not possible, while humans are in a dangerous zone of the
machine.
If the servo amplifier has been stored for longer than 1 year, then the DC bus link capacitors
will have to be re-formed. To do this, disconnect all the electrical connections.
Supply the servo amplifier for about 30 minutes from single-phase 230VAC to the terminals
L1 / L2. This will re-form the capacitors.
The adaptation of parameters and the effects on the control loop behavior are described in the
of the setup software.
66
Kollmorgen | September 2015
Summary of Contents for S700 Series
Page 14: ...S700 Safety Guide 1 Deutsch 1 3 3 Antriebssystem mit S701 S724 14 Kollmorgen September 2015 ...
Page 15: ...1 3 4 Antriebssystem mit S748 S772 S700 Safety Guide 1 Deutsch Kollmorgen September 2015 15 ...
Page 40: ... S700 Safety Guide 1 Deutsch 40 Kollmorgen September 2015 ...
Page 52: ...S700 Safety Guide 2 English 2 3 3 Motion system with S701 S724 52 Kollmorgen September 2015 ...
Page 53: ...2 3 4 Motion system with S748 S772 S700 Safety Guide 2 English Kollmorgen September 2015 53 ...
Page 78: ... S700 Safety Guide 2 English 78 Kollmorgen September 2015 ...
Page 116: ... S700 Safety Guide 3 Français 116 Kollmorgen September 2015 ...
Page 154: ... S700 Safety Guide 4 Italiano 154 Kollmorgen September 2015 ...
Page 167: ...5 3 3 Приводная система с S701 S724 S700 Safety Guide 5 Русский Kollmorgen September 2015 167 ...
Page 168: ...S700 Safety Guide 5 Русский 5 3 4 Приводная система с S748 S772 168 Kollmorgen September 2015 ...
Page 194: ... S700 Safety Guide 5 Русский 194 Kollmorgen September 2015 ...
Page 214: ... S700 Safety Guide 6 Appendix 214 Kollmorgen September 2015 ...
Page 215: ... S700 Safety Guide Kollmorgen September 2015 215 ...