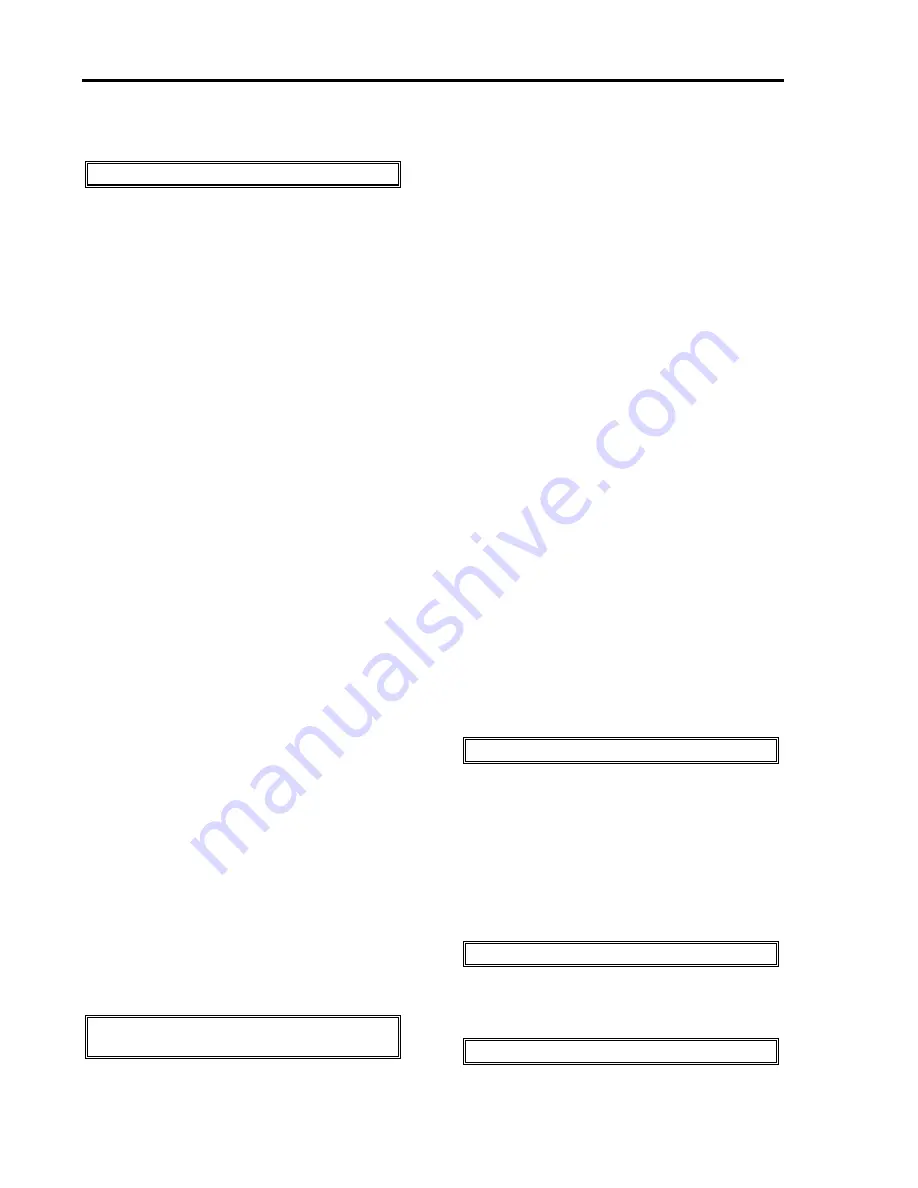
C
HAPTER
3 - O
PERATION
BDS5
3-2
The motor should be still. If your motor is
oscillating, disable the BDS5 by typing:
DIS
3.2.1 If You Get ERROR 17,
FEEDBACK LOSS
If the BDS5 generates ERROR 17, FEEDBACK
LOSS, then a lead in the resolver cable is probably
broken. First, verify that the cable is wired correctly
using the procedure in "Checking the Resolver Cable"
in section 2.7.10.
If the cable appears to be wired correctly, use an
oscilloscope to verify that the sine (Connector C3,
Pin 7) and the cosine (Connector C3, Pin 9) are
present. Note that the amplitudes of both these
signals vary with motor position, so you will need to
rotate the motor by hand to force sine and cosine to
their maximum values. Expect a sine wave with a
maximum peak-to-peak level of about 6.5 Volts at
8 kHZ.
If both sine and cosine are present on the connector
and your BDS5 continues to generate ERROR 17,
your unit may be malfunctioning; contact the factory.
3.2.2 If You Get ERROR 14, POWER
BUS
ERROR 14, "POWER BUS," is generated when the
BDS5 detects either an undervoltage or an
overvoltage. If the BDS5 cannot be enabled because
ERROR 14 continually reoccurs, it is probably
because of undervoltage. Return to "Checking the
AC Line Voltage" and "Checking the DC BUS
Voltage" beginning in section 2.7.11 to ensure that
the DC Bus is present.
If this error occurs only when the system is powered
up, it is probably because your program attempts to
enable the BDS5 before bus voltage is present.
OK2EN is a switch that is ON when your BDS5 can
be enabled without generating a fault. You can delay
enabling the BDS5 until bus voltage is present by
modifying your program to wait for OK2EN to be
ON.
TIL OK2EN EQ ON
EN
If the error occurs occasionally, it could be
overvoltage or undervoltage. Overvoltage is usually
caused by regenerative energy from a deceleration
which forces the DC BUS voltage to rise above the
BDS5 overvoltage level--about 200 VDC for
115 VAC line voltage systems and about 400 VDC
for 230 VAC. If the error occurs only during
deceleration, it is probably an overvoltage error. This
can be corrected by reducing the deceleration rate
(although often, it must be reduced dramatically) or
by adding increased regeneration capability. Contact
Industrial Drives Application Engineering to add
regeneration capability.
Undervoltage is caused by the loss of the AC Line.
The undervoltage detection level is set well under 100
VDC (70 VAC) so that low line (from "brown out")
almost never causes an undervoltage fault. Your
system may include protective circuits that remove
power from the BDS5 when a problem is detected
elsewhere in the system. This can cause the BDS5 to
generate ERROR 14 and lead you to suspect the
BDS5 of causing the original problem. If the
problem occurs only rarely, you may have to
purchase or rent a device to monitor the DC BUS
voltage to determine the cause.
3.2.3 If Your BDS5 System is
Unstable...
If the motor was oscillating, you need to retune your
system. First, try to stabilize the system with the
TUNE command. Type:
TUNE 10 2
Enable the drive. If your system is stable, you can
skip ahead to the next section. If you want to
improve the response, see Section 3.5 for details on
the TUNE command.
If your system is not stable, disable the BDS5. You
need to detune the system. First, disable the position
loop. Type:
PL OFF
Disable the integrating velocity loop (in other words,
enable the proportional velocity loop). Type:
PROP ON
Summary of Contents for BDS5
Page 2: ......
Page 3: ...BDS5 INSTALLATION AND SETUP MANUAL Old Number M93101 ISSUE 4 New Number MB5000H...
Page 4: ......
Page 8: ......
Page 10: ......
Page 18: ......
Page 20: ......
Page 62: ...CHAPTER 2 INSTALLATION BDS5 2 26...
Page 73: ...BDS5 CHAPTER 4 MAINTENANCE...
Page 74: ...CHAPTER 4 MAINTENANCE BDS5...
Page 78: ...CHAPTER 4 MAINTENANCE BDS5 4 4...
Page 86: ...APPENDIX A WARRANTY INFORMATION BDS5 A 2...
Page 88: ...APPENDIX B DRAWINGS BDS5 B 2 THIS PAGE INTENTIONALLY LEFT BLANK...
Page 116: ......