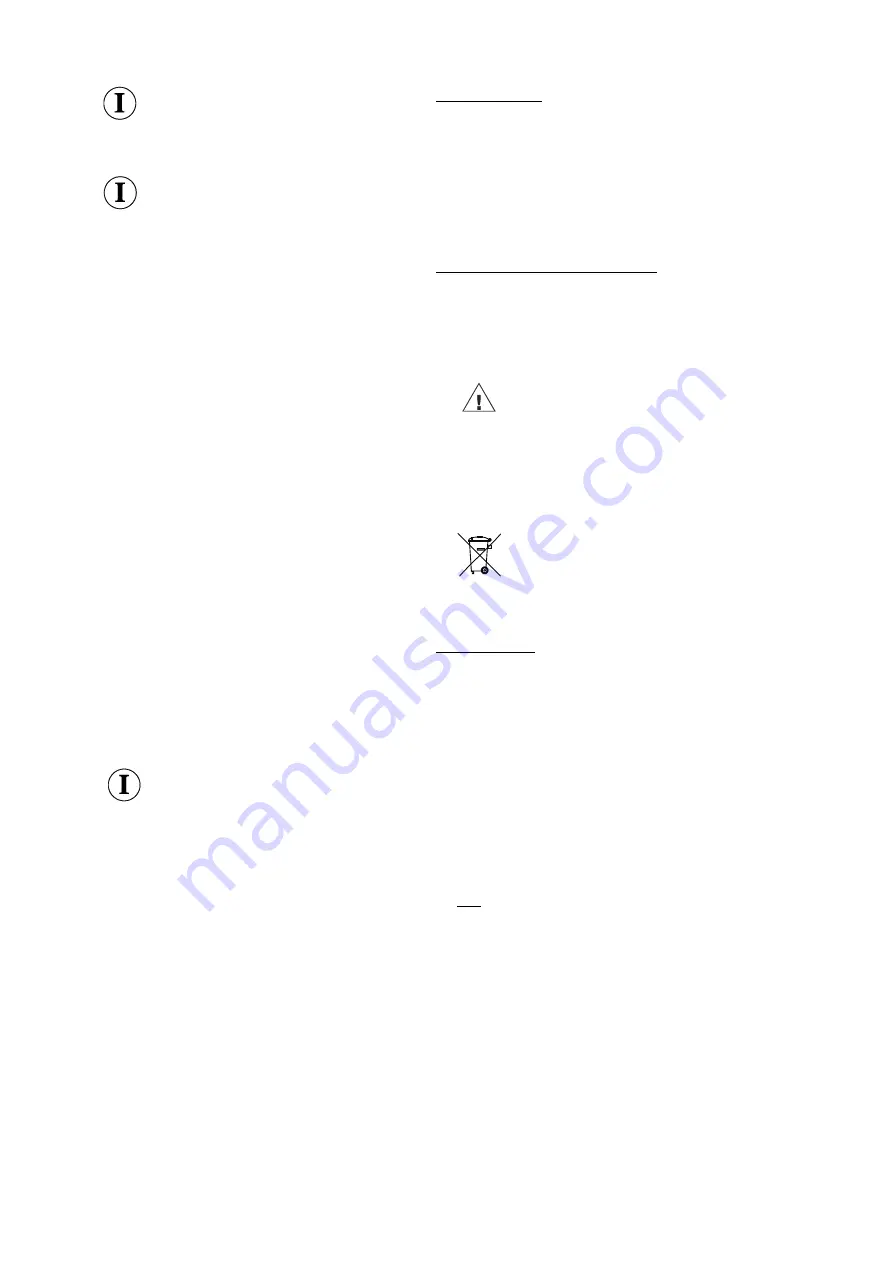
Instruction
Manual
UNP
2
page
8
_______________________________________________________________________________
Attention
Do not use bent or damaged pressing jaws.
For your job on the location we recommend the accessories shown
in picture 12.
Remark
As the tool manufacturer we offer perfectly designed
pressing jaws for all tube dimensions.
Special designs and customer solutions upon request.
5.4. Service and maintenance instruction
The reliable performance of the tool is dependent on careful
treatment and service. This represents an important condition to
safeguard a lasting connection. To safeguard this the tool have to
be maintained and serviced regularly (see chapter 4.3 for more
information).
We would like to draw your attention to the following points:
1. The electric-hydraulic pressing unit have to be cleaned and
dried after each use before being put into the transportation
case.
2. In order to guaranty a proper function of the machine the
pressing tool should be returned to the manufacturer after
10.000 pressing cycles.
3. The pin joints, the drive rolls and their guides must be oiled
regularly in small amounts.
4. Check through test crimps or have the tool manufacturer check
the tool and pressing jaws regularly for proper function.
5. Keep pressing jaws clean. Remove dirt with a brush.
6. In case of broken moldings please return the tool to an
authorised service center.
7. Check the tool components regularly for damages and proper
operation and performance of their intended functions.
8. Have damaged cords and plugs repaired by a qualified
serviceman.
In order to avoid possible malfunctions we offer you a
manufacturer service consisting of disassembly, cleaning,
exchange of possibly worn out parts assembly and final control.
Only a clean and properly functioning press system can over the
time safeguard a leaking free connection.
Within the determined use of the tool only the pressing jaws (Pos.-
#. 10) are permitted to be changed by the customers.
Attention
Do not damage the seals of the tool.
If the seals are damaged the warranty is invalidated.
5.5. Storage and transport of the crimping tool
In order to protect the tool against damages it has to be cleaned
carefully after every use and be put into the transportation case
which has to be closed safely.
Into this case you can put a pressing jaw(s) and the instruction
manual.
6. Troubleshooting
a.) The tool loses oil.
=>
Return the unit to the manufacturer. Do not open it and damage the
seal of the tool.
b.) No automatic retraction occurs.
=>
Stop the pressing process. Press the retract button (Pos.-#. 2) and the
operating switch continuously and simultaneously for about 10 sec. Will
the malfunction not be eliminated by this operation the tool has to be
returned to the manufacturer.
7. Putting out of operation/waste disposal
After intensive use even a high-quality tool has to be put of service.
The disposal of the various components of the tool have to be treated
separately. Doing that the first step is to dispose of the oil at special
delivery points.
Attention
Hydraulic oils represent a danger for the ground-water.
Uncontrolled draining of or improper disposal is under
penalty. (environmental liability law)
For the disposal of the remaining parts please reference the EC
environmental guideline.
Because of possible environmental damages we recommend to dispose
of the tool by professional companies.
Attention
Do not dispose of the unit in your residential waste
because it will finally end up on the waste dump which
would be hazardous for the environment.
A return of the old tool free of charge to the manufacturer cannot be
granted.
8. Technical Data
Weight (w/o pressing jaws): approx. 3,3 kg
Pressing force:
dependent on the pressing jaws
Thrust force:
min. 32 kN
Nominal voltage:
230V/50Hz
Nominal power:
200 W
Duty
cycle:
ED
5min/15min
Pressing time:
4s to 7s (depending on the nominal width)
Hydraulic oil:
65 ml "Shell Tellus T 15"
Environmental temperature: -20°C to +40°C
Sound level:
75 dB (A) in 1m distance
Protection class:
II
Vibrations:
<
2,5
m/s²
Dimensions:
see
Picture
2
Note
Additional copies of the of the IM are available upon request with no
charge. The part # is HE.8916_B.