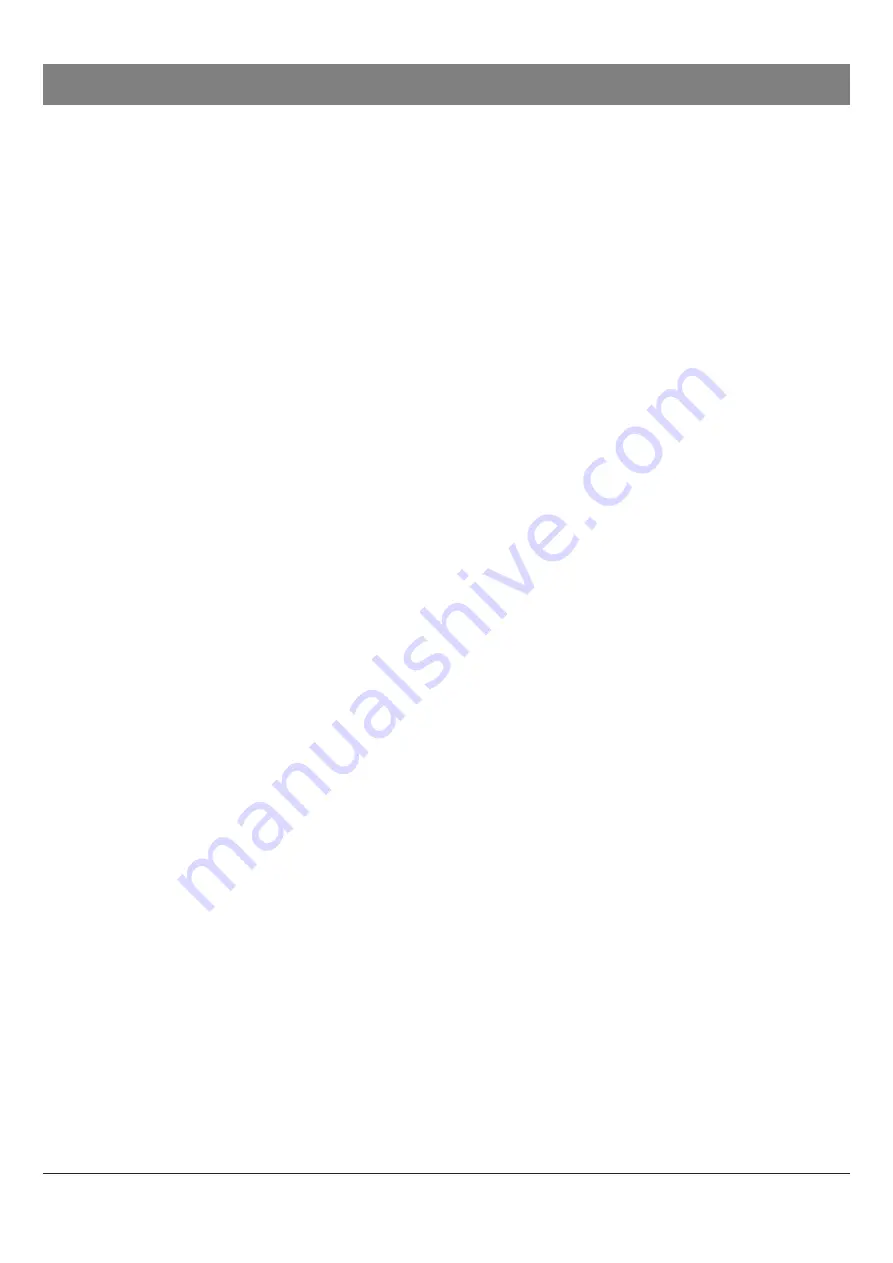
2 / 61
Table of Contents
2019/11
010-917_SON_EN
1 Introduction
4
1.1
Product description, general ............................................................................................. 4
1.2 Use....................................................................................................................................4
1.3
System types .................................................................................................................... 5
1.4
Overview of article numbers ............................................................................................. 5
1.5
Type plate ......................................................................................................................... 6
1.6
Scope of delivery .............................................................................................................. 7
1.7
General information on these operating and maintenance instructions ............................ 7
1.8
Assemblies and functional characteristics ........................................................................ 8
1.9
Illustrations and dimensions ............................................................................................. 9
1.9.1 Illustration system types - C ............................................................................................. 10
1.9.2 Illustration system types - D .............................................................................................. 11
1.9.3 Illustration system types - E .............................................................................................. 12
1.9.4 Illustration system types - F .............................................................................................. 13
1.9.5 Control unit ....................................................................................................................... 14
2 Safety
16
2.1
Intended use ..................................................................................................................... 16
2.2
Personnel selection and qualification
............................................................................... 16
2.3
Organisational safety measures ....................................................................................... 16
2.4
Hazards caused by the product ........................................................................................ 17
2.4.1 Risk caused by electric current and cables ...................................................................... 17
2.4.2 Risk caused by heat development at the pump(s) ............................................................ 17
2.4.3 Danger of slipping when the system is emptied ............................................................... 17
2.4.4 Risk of infection when coming into contact with the wastewater ...................................... 17
3 Installation
18
3.1
Recommendations for the set-up location / operation ...................................................... 18
3.2
Setting up / installing the grease separator system .......................................................... 18
3.2.1 Fitting the inlet and outlet .................................................................................................. 19
3.2.2 Fitting or removing the pump ............................................................................................ 19
3.2.3 Mounting the refill inlet
...................................................................................................... 20
3.2.4 Installing the screw-type valve - E .................................................................................... 20
3.2.5 Installing the solenoid valves - F ....................................................................................... 20
3.2.6 Installing the SonicControl
sensor (option) - F .................................................................. 21
3.2.7 Mounting the remote control - F ........................................................................................ 22
3.3
Mounting and initialising the control unit .......................................................................... 22
3.3.1 Control unit for system type D .......................................................................................... 22
3.3.2 Control unit for system type E ........................................................................................... 26
3.3.3 Control unit for system type F ........................................................................................... 28