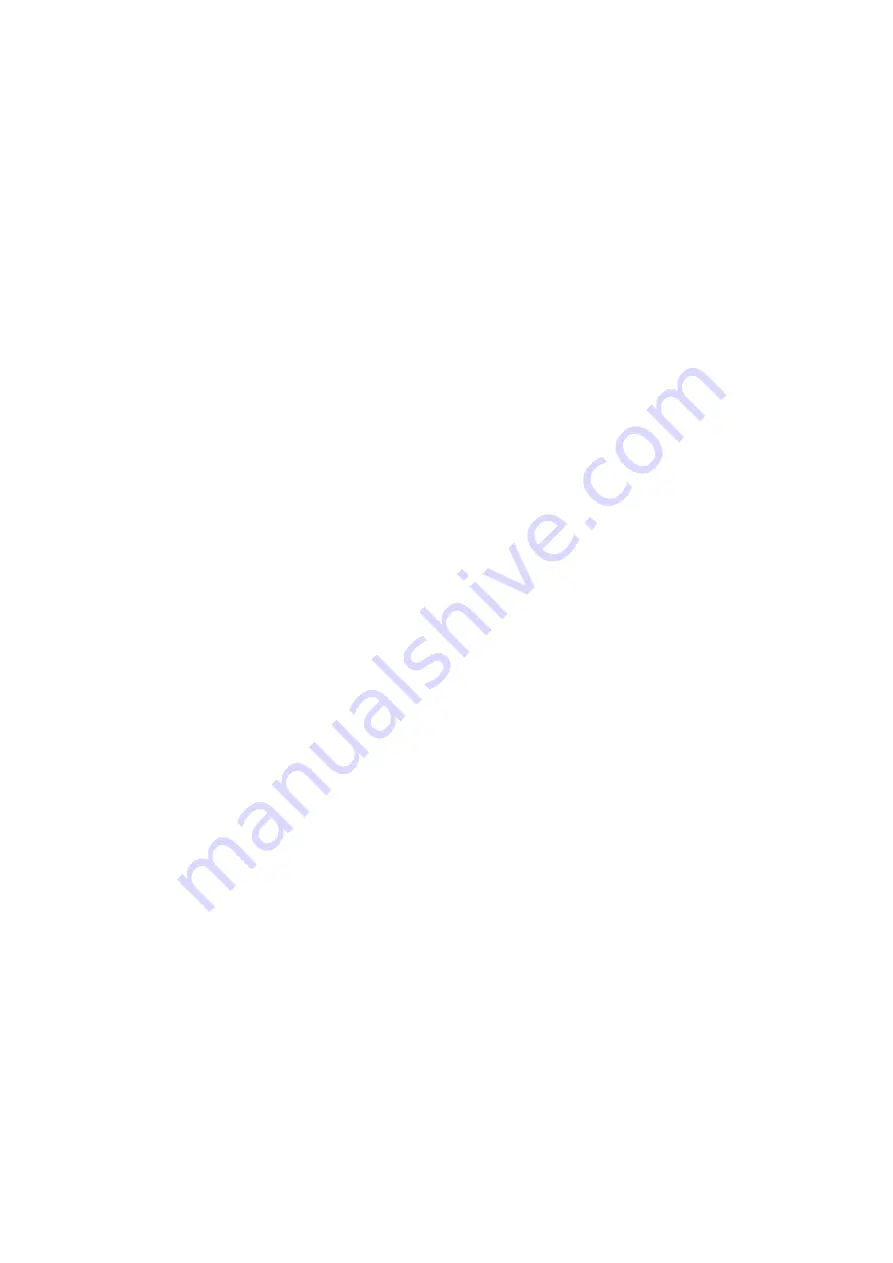
8/07
Art nr K0006129
12
-
Do not cement the base blocks 1 (Fig. 2A) to the floor or
protective floor plate. Important!
Do not touch cemented joints until they have dried out. Poor joints can
cause parts of the masonry surround to work loose.
2B.6.1. ASSEMBLY
(Figs. 2A and 2B)
General:
-
Mix only half of the mortar at a time. Otherwise there is a risk that
the mixture will begin to harden before the work of assembling
and cementing the surround has been completed.
-
Make sure that the individual blocks stand firm on top of one
another. Scrape off any lumps of mortar before cementing the
blocks together.
-
The rear edges of the blocks must be aligned with one another
,so that the metal sheets that form the rear panel can be fitted
flush against all the blocks.
-
All joints must be even and properly sealed. Remember that the
cemented joints won’t be visible once the surround has been
finished with a textured coating.
-
Take care to centre the blocks accurately on top of one another.
-
Do not touch the joints until the mortar has dried.
-
Do not press the blocks together so hard that the previous joint
opens up.
A
Place the base blocks (1) on the floor so that there is a gap
of at least 8 cm between the rear edge and the wall. Make
sure that the blocks are placed perfectly parallel to one
another and at right angles to the wall. The distance
between the outside edges of the base blocks must be 86
cm.
B
Apply a layer of mortar to the top edges of the blocks.
C
Centre the block that supports the fire-box (2) on top of the
base blocks so that the outside edges project an
equal
distance on both sides. (The rear edge must be perfectly
aligned with the rear edge of the base blocks.)
E
Put the fire-box (3) in place so that it is the same distance
from both outside edges of the block on which it is standing.
The rear edge of the fire-box must be aligned with the
recessed part of the block (approx. 9 cm inward from the
rear edge of the base blocks). Screw the heat reflector (4)
and the upper rear panel (3) together as shown in Figs. 3A
and 3B. Press the “short” end of the flue pipe (10) into the
opening on the rear of the fire-box so that the metal plates
(4) and (3) are held in place between the fire-box and the
chimney. It is still possible to make minor adjustments to the
position of the fire-box if required. Slide the “long” end of the
flue pipe into the hole in the chimney breast. Adjust so that
the “swollen” joint at the short end of the pipe abuts the flue
opening in the fire-box. Leave the metal plates hanging
loose for the time being.
F
Apply a layer of cement to the supporting block (2) in those
places where the side blocks will stand. Take care not to
get any mortar in the holes which will be used to
accommodate the metal fixing pins in the side blocks.
G
Place the side blocks (4) with the concave surfaces facing
outwards and the angled edges facing forwards so that the
metal pins slot into the holes in the supporting block below
(2). There must be an expansion gap of at least 1 cm
between the side blocks and the fire-box. If necessary, the
fire-box must be repositioned slightly to provide this gap.
H
Apply a layer of mortar to the top edges of the side blocks
(4).
I
Place the cornice (5) on top of the side blocks with the
angled edge facing downwards, making sure that the metal
pins in the side blocks fit into place in the holes on the
underside of the cornice. Ensure that there is no mortar in
the holes. Check to make sure that the rear edges of all the
blocks are perfectly aligned.
J
Support the front of the cornice (5) with a piece of wood (12)
as shown in Fig. 2B. Make sure that all the joints are strong.
(If possible, it is now advisable to let the cemented blocks
dry and harden to ensure that the construction is strong
enough before proceeding with any further work.)
K
Apply a layer of mortar to the top edge of the cornice (5).
L
Place the base block for the hood (6 ) centrally on the
cornice (5), ensuring that the rear edges of both blocks are
perfectly aligned.
M
Apply a layer of mortar to the top edge of hood base (6).
N
Place the top block for the hood (7) centrally on the hood
base (6), ensuring that the rear edges of both blocks are
perfectly aligned.
O
Apply a layer of mortar to the top edge of hood top (7).
P
Place the top block (8) centrally on the hood top (7),
ensuring that the rear edges of both blocks are perfectly
aligned. The other edges should project slightly along the
sides and at the front.
Q
Check to make sure that the joints are sound and
sufficiently even so that they will not be visible when the
construction has been finished with a textured coating.
Repair any damage to the joints if necessary. Clean off any
excess mortar and ensure that the fire-box is correctly
positioned.
2B.6.2. Installing the rear panels
(Figs. 3A, 3B and 4)
The remaining metal plates can be fitted as soon as the blocks have
been assembled and while the mortar is still damp.
Test-assemble the metal plates first to make sure that they fit as
intended. Take care not to move the building blocks that now form the
fireplace surround.
The holes punched in the sheets of metal are somewhat larger than
necessary. This is to allow for a certain amount of movement in the
construction as a whole. If there is no movement in the metal plates
once the bolts have been fitted in place, the construction has been
incorrectly assembled. Check it and make any adjustments. When
correctly assembled the metal plates expand when heated to provide
extra support for the fireplace.
The metal panels are assembled as followed:
A
Fit the lower rear panel (2) in place as shown in Figs. 3A
and 3B against the back of the fire-box and fix (but do not
tighten!) the screws in the lower holes.
B
Slot the heat reflector (4) into place on top of the lower rear
panel so that the angled “wings” hold the panels edge to
edge. The pressed metal edges of the heat
reflector
should be pointing backwards towards the chimney
breast.
C
Finger-tighten the screws. The top rear panel (3) should
now rest on top of the lower rear panel (2) and the heat
reflector should be centred.
Do not tighten the screws fully
until the mortar in the fireplace surround has had time to dry
fully!
2B.7. ACCIDENTAL DAMAGE
Any accidental damage to the building blocks may be repaired with
the same type of mortar as used to cement the blocks together. These
repairs will not be visible once the surround has been finished with a
textured coating.
2B.8. DRYING TIME
The fireplace surround is complete once the mortar has dried and
hardened. This usually takes about 48 hours at room temperature. If
the temperature is lower, the drying time is longer.
Do not tighten the fixing screws of the metal panels at the rear of the
fireplace until the mortar is fully dry. Tighten the screws carefully
(approx. to 5 Nm). The metal panels must sit tight yet still have the
opportunity to expand in their holes as the fireplace becomes hot. The
panels are slightly curved in the middle so that there is still a certain
amount of “give” in the metal even after the screws have been
tightened.
When the screws have been tightened the piece of wood holding the
cornice in place at the front of the fireplace may be removed.
If the fireplace is connected to a rear flue, the hot air vent (Fig. 5:1)
can now be laid in place on top of the fireplace surround.
2B.9. SURFACE FINISH
The uneven surface of the building blocks in the fireplace surround
provides extra good adhesion for the surface finish and makes it easy
to achieve a surface that looks like antique rendering.
Any minor damage to the blocks is effectively covered up by the
textured surface finish.
There are many different textured finishes and colours to choose from
on the market. Some latex-based products are suitable as surface
finishes for masonry fireplaces, but always consult your local
specialist paint dealer before starting to apply the finish. For a smooth
surface the entire construction must be dressed with heat-resistant
plaster before the surface coating is applied.
Surface finish:
-
Prime the entire surface of the surround.
-
Apply a generous layer of surface coating with a brush or
textured roller to achieve the desired pattern. However, be more
Summary of Contents for BRAVO
Page 23: ...4 07 Art nr K0006129 23 3 2 x 6 3 8 500 C 3 9 2 Kastor 4 5 0730 99...
Page 24: ...4 07 Art nr K0006129 24...
Page 25: ...4 07 Art nr K0006129 25...
Page 26: ...4 07 Art nr K0006129 26...
Page 27: ...4 07 Art nr K0006129 27...
Page 28: ...4 07 Art nr K0006129 28...
Page 29: ...4 07 Art nr K0006129 29...
Page 30: ...4 07 Art nr K0006129 30...
Page 31: ...4 07 Art nr K0006129 31...
Page 32: ...4 07 Art nr K0006129 32...