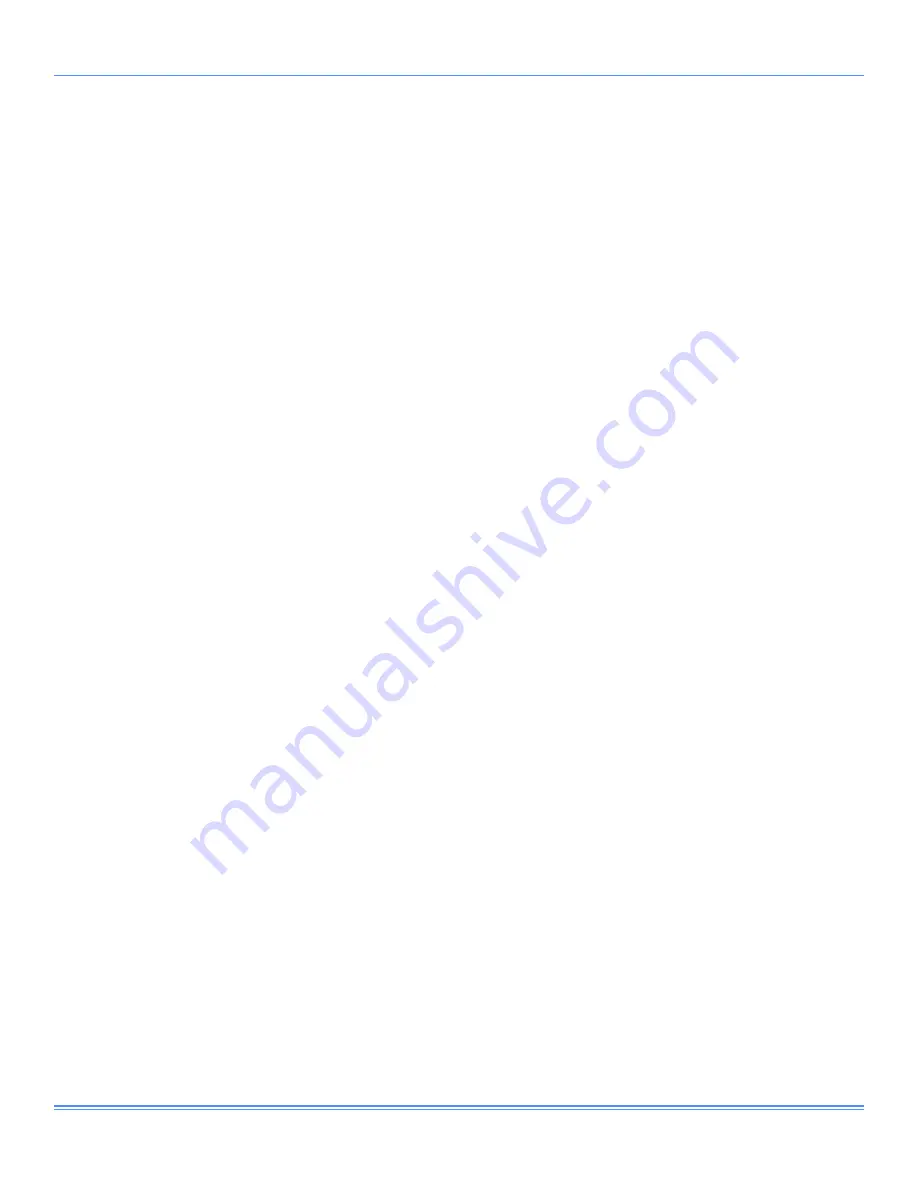
Johnson Controls
5513350-JTG-1018
117
Guide Specifications (Continued)
3.
Filter Transducer -
A filter transducer shall be pro
-
vided and wired to the rooftop's control panel. The
unit controller shall display the pressure drop across
the filter[s]. Single transducer shall be provided to
measure pressure drop across both filter banks.
[Transducers shall be provided to measure pressure
drop across each filter bank].
4.
Differential Pressure Gauge -
A flush mounted,
factory-installed differential pressure gauge shall be
provided to measure pressure drop across both filter
banks. [Flush mounted, factory-installed differential
pressure gauges shall be provided to measure pres-
sure drops across each filter bank.] Manufacturer
shall provide fully functional gauges complete with
tubing.
Evaporator Section
1.
Cooling Coil -
Evaporator coils shall be direct ex-
pansion type with interlaced circuiting to assure com
-
plete coil face activity during part-load operation. Coil
tubes shall be copper with internally enhanced tubes.
Tubes shall be enhanced mechanically, expanded to
bond with the aluminum [copper] fins. All coils shall
be pressure-tested at a minimum of 450 psig.
[Evaporator coils shall be protected by the E-Coat
10-1 four coat process. Coils shall be dipped in a
phenolic coating, that shall provide substantial resis-
tance to corrosion of aluminum and copper.]
2.
IAQ Drain Pan -
The main coil drain pan shall be dou-
ble-sloped with a condensate connection through the
base rail of the unit. Drain pans for cooling coils [and
humidifier] shall meet the requirements of ASHRAE
62.1. Drain pans shall be constructed of stainless
steel. [Provide a condensate overflow switch in the
primary drain pan.]
3.
Intermediate Drain Pan -
Coils with finned height
greater than 48 inches (40 and 50 ton units) shall
have an intermediate drain pan extending the entire
finned length of the coil. The intermediate pans shall
have drop tubes to guide condensate to the main
drain pan.
4.
UV Lights [Optional] -
Surface decontamination of
the evaporator coil and drain pan shall be provided
using UV lights. The UV lights shall be installed in
the downstream side of the evaporator coil/drain pan.
The UV lights (tubes) shall be shipped loose in pro
-
tective packaging for installation by the contractor.
Supply Fan Section
1.
Fan -
The fan section shall be equipped with a SWSI
airfoil plenum wheel. Plenum fan shall be direct drive.
An access door shall be provided on the opposite
side of the control panel for fan/motor access.
2.
Fan Motor -
Fan motors shall be NEMA design
ball-bearing types with electrical characteristics and
horsepower as specified. Motors shall be nominal
1,800 RPM, ODP type [TEFC type].
3.
Mountings -
Fan and fan motor shall be internally
mounted and isolated on a full width isolator support
channel using 1-inch [2-inch] springs [and seismic
restraint].
4.
Variable Air Volume (VAV) Fan Control -
VAV
supply fan control shall be accomplished by using
a VFD and supply fan motor combination matched
with supply fan to generate design performance at
appropriate fan speed. The VFD shall include an in-
tegral DC line reactor to reduce harmonic distortion
in the incoming and outgoing power feeds. If a DC
line reactor is not provided, an AC line reactor shall
be provided.
5.
Single Zone VAV (SZVAV) -
In cooling mode, refrig-
eration capacity or compressor stages are cycled ON
or OFF to maintain DA temperature (DAT). In heating
mode, additional stages are cycled ON or modulated
to maintain DAT setpoint. The supply fan speed is
modulated to maintain zone temperature setpoint. The
unit uses either a BAS signal, RA temperature (RAT),
or a zone temperature sensor to determine zone tem-
perature and deviation from setpoint.
6.
Redundant VFD [Optional] -
Direct drive plenum
(DDP) supply fans shall be provided with a 100%
redundant VFD. Redundant VFD shall automatically
operate in the event that the primary VFD fails.
7.
All VFDs shall be factory tested and matched with
each unit.
8.
VFD Reactor [Optional] -
A 3% impedance AC line
reactor shall be provided for the supply fan VFD.
9.
Shaft Grounding Rings [Optional]
on motors shall
be provided to prevent electrical bearing fluting dam-
age by safely diverting harmful shaft voltages and
bearing currents to ground, increasing the motor lon-
gevity.
10.
Inlet Guards [Optional]
shall be provided on inlet of
supply fan.