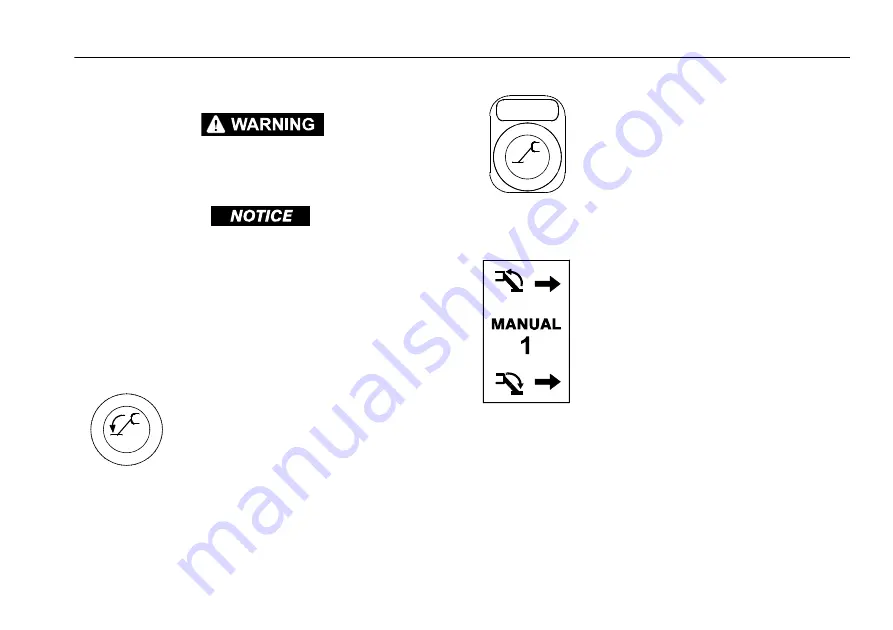
SECTION 4 - MACHINE OPERATION
3121773
– JLG Lift –
4-11
4.6
OUTRIGGER OPERATION
BE CERTAIN OUTRIGGER PADS ARE SET ON A FIRM AND HORIZONTAL SUR-
FACE. DO NOT SET OUTRIGGER PADS ON INCLINED, VERTICAL, OR SLIPPERY
SURFACES.
THE OUTRIGGERS WILL NOT OPERATE UNLESS THE BOOM AND JIB ARE COM-
PLETELY LOWERED, RETRACTED AND ALIGNED WITH THE BASE.
NOTE:
Base and boom/jib must be aligned and stowed
before this function will operate, see Section 4.4, BASE
AND BOOM/JIB ALIGNMENT.
Setting Outriggers From the Platform/Remote Console
(Reference Figure 4-3. on page 4-16 for item number location)
Either
- Press and hold the outrigger auto-
set and level button 7
(item 7)
until OK
appears on the platform LCD display;
AUTO
7
or
Operate each outrigger separately by
pressing button 2
(item 2)
to select which
outrigger to control
(each outrigger is num-
bered 1 thru 4, see decal, each press of but-
ton 2 displays the outrigger selected on the
LCD display)
. Press button 1
(item 1)
to
retract or button 7
(item 7)
to set that out-
rigger. The OK will appear on the display
when the outriggers are set properly and
the unit is level.
MANUAL
SELECT
2
Note:
To cycle back to outrigger auto-set
mode, press button 2 (item 2) until the
LCD display shows the normal operating
icons.
To
order
go
to
Discount-Equipment.com