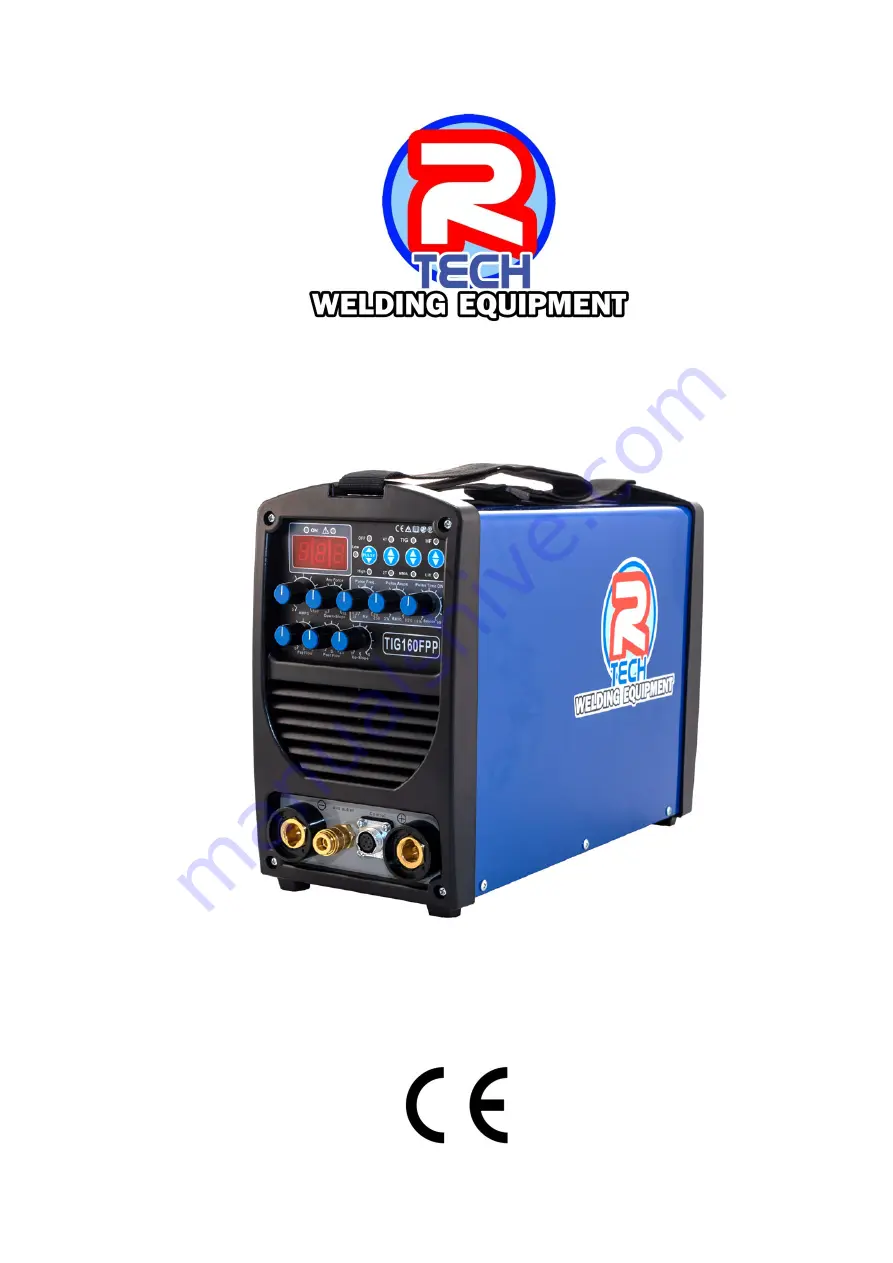
email: [email protected]
Tel: 01452 733933 Fax 01452 733939
TIG160FPP DC TIG WELDER 240V
OPERATION INSTRUCTIONS
Version 2020-12
email: [email protected]
Tel: 01452 733933 Fax 01452 733939
TIG160FPP DC TIG WELDER 240V
OPERATION INSTRUCTIONS
Version 2020-12