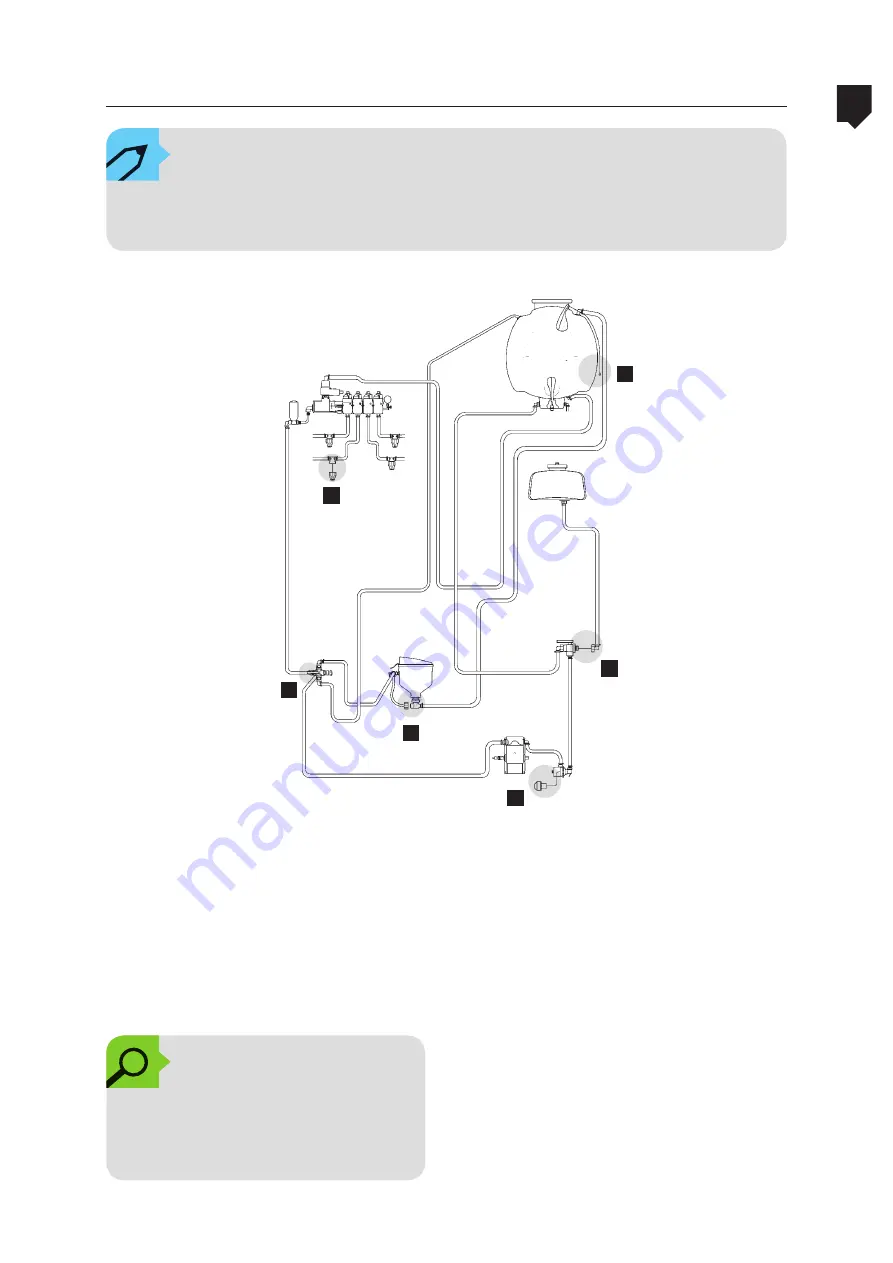
5-93
5
M
A
INTE
NAN
CE
ADVANCE 2000
Winter storage
NOTE:
In areas where temperatures drop to 0° or less, the water accumulated in the spray
pump can freeze and cause serious damage.
Procedures:
1. Drain the spray tank through the dis-
charge valve (A).
2. Remove the suction filter cap (B).
3. Run the sprayer for about 30 seconds at
between half and low speed.
4. Disconnect the inlet hose of the auxiliary
tank bypass valve (C).
5. Remove the in-line filter cap (D).
6. Operate the flow bypass valve lever (E) to
drain the circuit.
7. Reinstall the components in their place.
8. Repeat this operation at the end of each
working day during winter time to avoid
problems in future spray applications.
OBSERVATION:
To avoid damage to compo-
nents, do not run the sprayer
over the recommended time.
E
F
D
B
C
A
Summary of Contents for Advance 2000 AM-18
Page 2: ......
Page 4: ......
Page 6: ......
Page 8: ......
Page 28: ......
Page 44: ......
Page 46: ......
Page 52: ......
Page 54: ......
Page 72: ......
Page 74: ......
Page 104: ......
Page 108: ......
Page 110: ......
Page 115: ...ADVANCE 6 115 Technician visits record Date No of Hours Problems Technician Retailer...
Page 116: ......
Page 118: ......