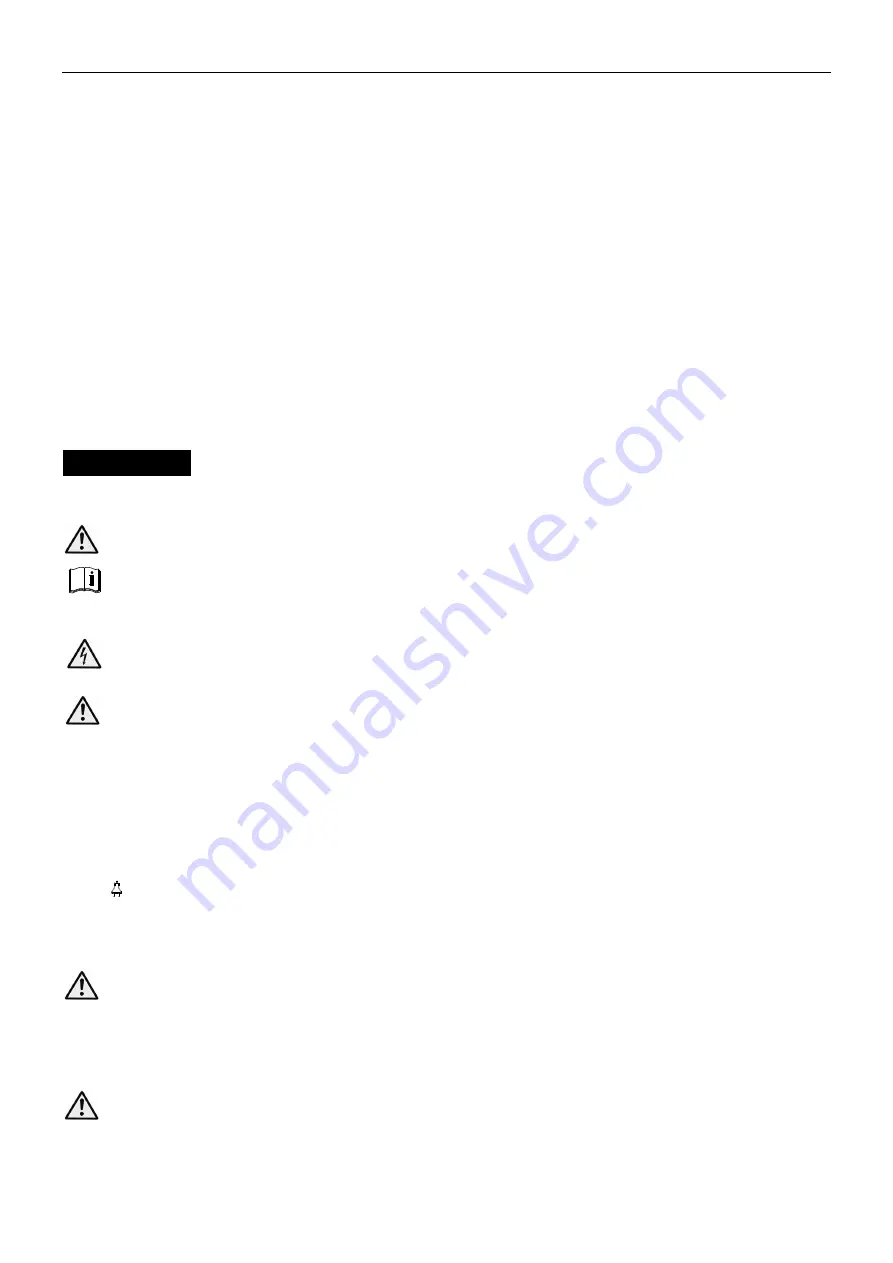
en
20
6.1.9
Float switch
Depending on the type of pump installed, one or more float switches may be fitted. The float switches are already installed and
calibrated.
There may be a float switch located above the other ones in the pumping station. This is used to signal the presence of an excessive
liquid level in the tank. In this case, an electric command and control panel must be installed.
6.1.10
Mounting the cover
Make sure the gaskets of the cover lie at the bottom of its housing before screwing the cover to the tank.
Check that the gasket does not slip in the thread when tightening.
When installing the product inside buildings, fully tighten the cover to ensure liquid and gases cannot leak from the station.
To prevent the unauthorised opening of the cover, secure it to the station using the supplied screws and washers. Pass the screw
through the slot on the outer edge of the cover and screw into the relative housing in the tank. The washer should be interposed
between the screw head and the upper surface of the cover. There may be a lock attached directly to the cover. In this case use the
supplied key to open and close the cover.
6.1.11
Mounting the extension
When installing the product inside buildings, a 300 mm high extension can be fitted.
The extension uses the same gasket as the one on the cover. Refer to the section on mounting the cover for tightening the extension
with the gasket.
After tightening the extension, make sure it cannot come loose. Use the screws supplied with the extension. Make a Ø 3 mm hole in
the extension thread area and then tighten.
Up to 2 extensions may be installed.
6.1.12
Electrical connections
Electrical connections may only be performed by a qualified installer in compliance with current regulations.
Make sure that the supply type, voltage and frequency match the ratings of the electric pump and electric
panel shown on the respective rating plates. Provide suitable short circuit protection on the supply line.
Before making electrical connections, read the manuals of the electric pump and electric panel (where
applicable), the instructions and any wiring diagrams.
Before proceeding with any operations, make sure that all the connections (even those that are potential-
free) are voltage-free.
Electric pumps can be fitted with a thermal protection incorporated in the motor (motor protector). Take
care as the electric pump could start suddenly after the motor winding has cooled.
Unless otherwise specified in local bylaws, the supply line must be fitted with:
•
a short circuit protection device.
•
a high sensitivity residual current circuit breaker (30 mA) for additional protection from electrocution in case of inefficient
grounding.
•
a general switch with a contact aperture of at least 3 mm.
Ground the system in compliance with current regulations.
The stations are supplied with an electric cable. Connect the cable to the mains power supply.
When installing the product inside a building, pass the cables through the grommets on the tank. In case of underground
installation, the additional cable passage can be used. On the station, identify the location of the cable duct, marked with the
symbol
. Open the duct, connect the piping and thread the cables inside. Make sure the piping is watertight.
Make sure there is enough cable inside the tank to allow the pump to be removed.
Connect to the mains power supply.
6.2
Initial start-up
Before starting the station and the electric pump, check that there are no residues or other materials in the
system and tank that can prevent correct operation.
In this phase, leave the check valve on the inlet piping closed and fill the lifting station with clean water. Open the check valve on the
outlet piping, check the piping is perfectly watertight and make sure the electric pump works correctly. Also check that the electric
pump is primed.
Open the check valve on the inlet piping and make sure the station works correctly.
The flow of liquid from the various users must not prevent the float switches in the basin from operating
correctly.
For three-phase electric pumps, check the correct direction of rotation of the impeller. Also check the electric pump manual.
Make sure that the cut-in levels of the float switches are correct. If necessary adjust them according to effective system requirements.
WARNING
Summary of Contents for Lowara Doublebox Plus Series
Page 47: ...el 47 8 4 2 5 5 1 5 1 1 60 cm 3 1 5 1 2 Singlebox Plus Doublebox Plus 100 kg 3 1 5 1 3...
Page 49: ...el 49 6 1 6 1 6 1 7 6 1 8 6 1 9 6 1 10 6 1 11 300 mm 3 mm 2 6 1 12 30 mA...
Page 50: ...el 50 3 mm 6 2 2 6 2 1 0 7 m s 2 3 m s 6 3 2 7 7 1...
Page 51: ...el 51 7 2 PVC 7 3 8 7 vortex...
Page 52: ...el 52 9 10...
Page 85: ...ru 85 8 4 2 5 5 1 5 1 1 60 3 1 5 1 2 Singlebox Plus Doublebox Plus 100 3 1 5 1 3 6...
Page 87: ...ru 87 6 1 6 1 6 1 7 6 1 8 6 1 9 6 1 10 6 1 11 300 3 2 6 1 12 30 3...
Page 88: ...ru 88 6 2 2 6 2 1 0 7 2 3 6 3 2 7 7 1 7 2...
Page 89: ...ru 89 7 3 8 7 vortex...
Page 90: ...ru 90 9 10...
Page 118: ...it en fr pt es el de nl sv fi ru pl da tr 118...
Page 121: ...it en fr pt es el de nl sv fi ru pl da tr 121...
Page 123: ...it en fr pt es el de nl sv fi ru pl da tr 123 SINGLEBOX PLUS DOUBLEBOX PLUS...