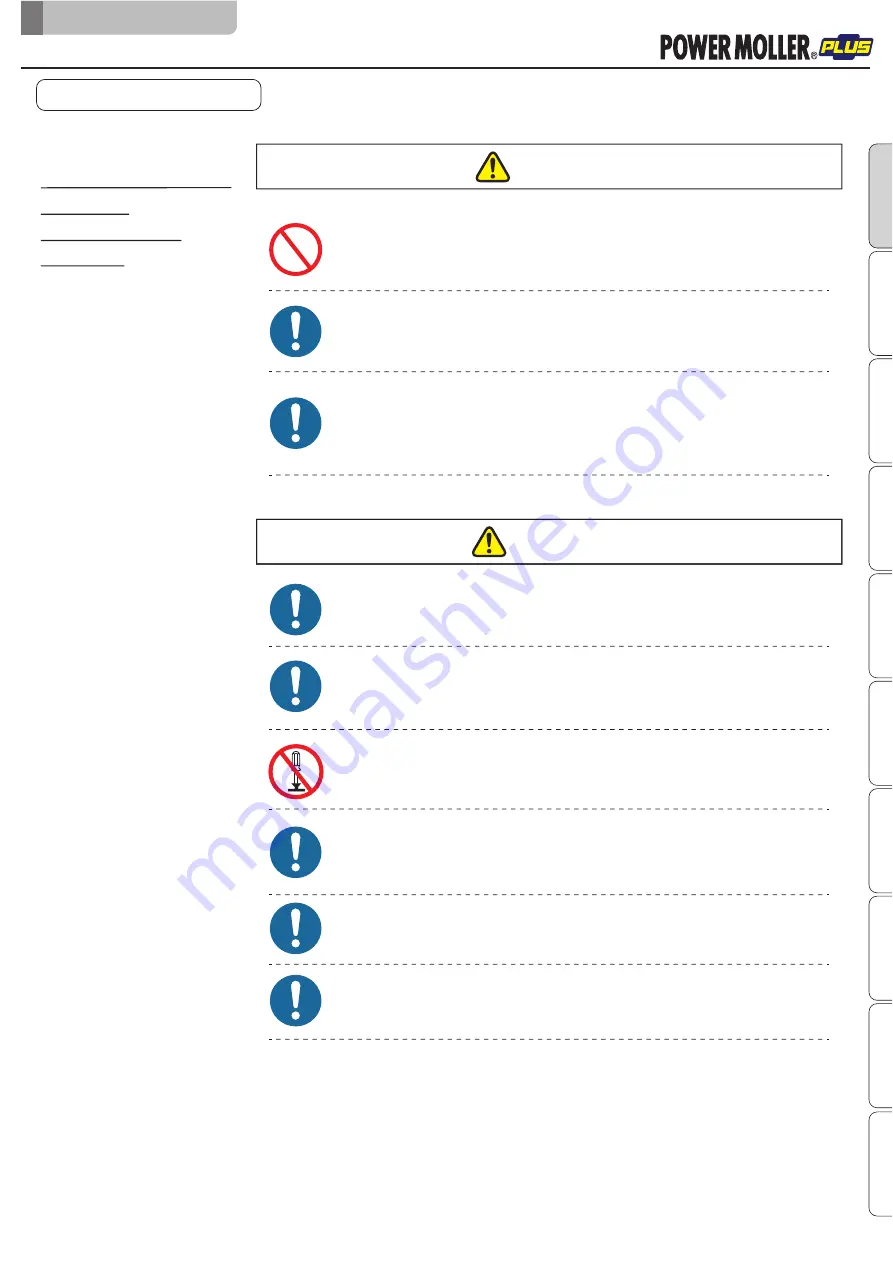
11
CAUTION
At the time of maintenance and inspection, post warning
labels so as to prevent unauthorized persons from turning on
the power.
For maintenance and inspection, wear protective equipment, such
as gloves.
Failure to follow this could result in hands getting injured by metal parts.
Do not disassemble sections and/or parts other than those
specified.
Failure to follow this could result in malfunction and/or unexpected accidents.
Make sure to prepare maintenance parts designated by ITOH
DENKI.
Using parts other than those designated by us could result in malfunction.
Failure to follow this could result in unexpected accidents.
Secure the working space for maintenance around this product.
Working in the forced position could result in unexpected accidents.
If any abnormalities are found, do not use this product until
the causes have been eliminated completely.
Using this product with unattended abnormalities could result in not only damage
to the devices, but also unexpected accidents.
Perform maintenance and inspection in a “Pollution Degree 2”
environment, as defined in IEC60664-1.
When disassembling the product, make sure to fully understand
the maintenance and inspection contents before working.
3-5.
Precautions on start-up
inspection/
maintenance and
inspection
Precautions on start-up inspection
MABS technical document
3. Safety precautions
Safety precautions
Advanced preparation
Product check
Structures
Installation/Wiring
Control/Operation
Maintenance/Inspection
Troubleshooting
Appendix
IB-E06F-M1 settings
WARNING
Have specialists (or people who have acquired sufficient skills)
perform maintenance and inspection under instructions by
management supervisors.
Original notice - U1.1