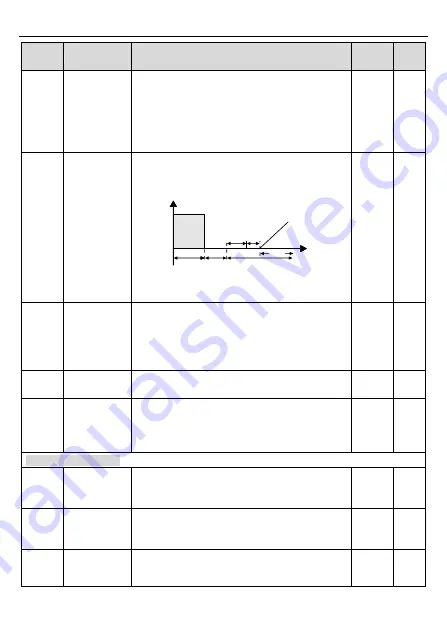
Goodrive20-EU series VFD
Function parameters
45
Function
code
Name
Detailed instruction of parameters
Default
value
Modify
P01.21
Restart after
power off
This function can enable the VFD to start or not
after power off and power on.
0: Disabled
1: Enabled, if the starting need is met, the VFD
will run automatically after waiting for the time
defined by P01.22.
0
○
P01.22
The waiting
time of restart
after power off
The function determines the waiting time before
the automatic running of the VFD when powering
off and powering on.
Output frequency
Running
Power off
Power on
Running
t
t1
t2
t1=P01.22
t2=P01.23
Setting range: 0.0
– 3600.0s (valid when
P01.21=1)
1.0s
○
P01.23
Start delay
time
The function determines the brake release after
the running command is given, and the VFD is in
a stand-by state and wait for the delay time set
Setting range: 0.0
– 60.0s
0.0s
○
P01.24
Delay of
stopping speed
Setting range: 0.0
– 100.0s
0.0s
○
P01.25
0Hz output
Select the 0Hz output of the VFD.
0: No voltage output
1: With voltage output
2: Output at stop DC brake current
0
○
P02 Group Motor 1
P02.01
Rated power of
async-motor
0.1
– 3000.0kW
Depend
on
model
◎
P02.02
Rated
frequency of
async-motor
0.01Hz
50.00Hz
◎
P02.03
Rated speed of
async-motor
1
– 36000rpm
Depend
on
model
◎
Summary of Contents for GD20-004G-2-EU
Page 1: ......
Page 168: ...6 6 0 0 1 0 0 4 8 4 201912 V1 6...