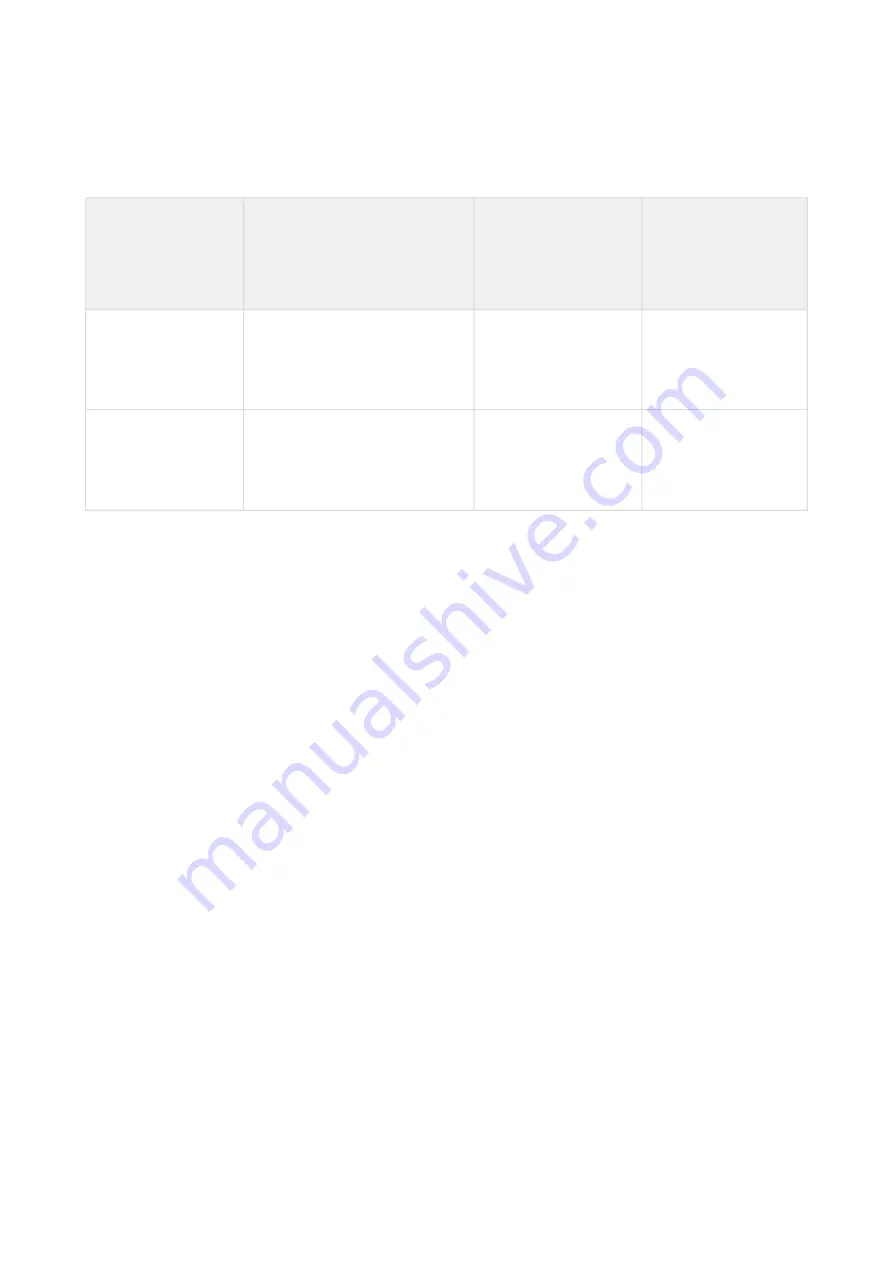
Everest XCR - Product manual |
Wiring and Connections
INGENIA | 2020-10-01 00:04:38
73
9.8. Communications
The Everest XCR provides the following network communication interfaces for configuration and operation.
Communication
Option
(Can be changed by
firmware upgrade)
J4 connector (ECAT 0)
functionality
J3 connector (ECAT 1)
functionality
J2 (I/O) connector pins
9, 11
(Default supplied)
EtherNET
standard port (default
address 192.168.2.22).
Allows configuration and tuning
using
.
Not used.
CANopen
interface
CAN_H and CAN_L.
EtherCAT INPUT
port 0.
can be accessed via
Beckhoff Twincat tool from a PC.
EtherCAT OUTPUT
port
1
CAN port not be used
when the drive is
configured as EtherCAT.
9.8.1. CANopen Interface
Everest XCR Servo Drive supports the CANopen interface, a multi-terminal communication protocol based on CAN
(Controller Area Network) bus. When the drive is configured with the CANopen interface the J4 connector ETH Port
0 should be used with a standard Ethernet port for configuration and firmware loading. The Everest XCR CAN
interface is not isolated. If your computer has no Ethernet port, you can use an Ethernet - USB adapter, like
It is possible to control a servo drive from a CAN Master or from a computer with a CAN transceiver. Some USB to
CAN transceivers that work with Everest XCR are indicated here: Kvaser Leaf SemiPro HS (
EAN:
73-30130-00242-5)
,
Kvaser Leaf Professional Rugged HS (EAN: 73-30130-00509-9), Peak Systems PCAN-USB (
IPEH-002021)
, Peak
Systems PCAN-USB opto-decoupled (IPEH-002022). Always ensure to have the drivers installed prior to connection.
An example of the required wiring for the CANopen interface
is shown in the next figure.