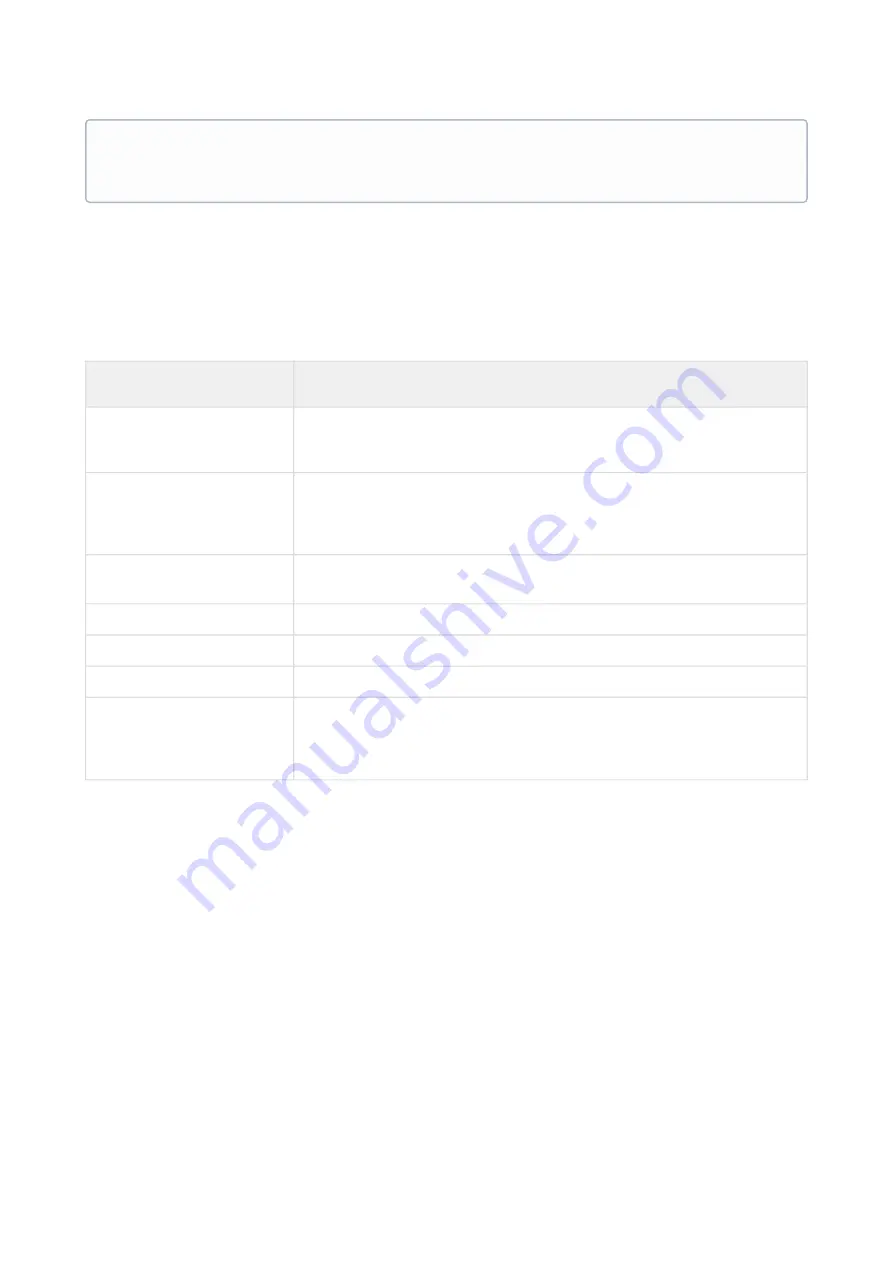
Everest XCR - Product manual |
Wiring and Connections
INGENIA | 2020-10-01 00:04:38
61
9.6.2. Absolute Encoder 1
The Everest XCR servo drive
absolute encoder 1 can be used as
position, velocity, and commutation
feedback
device
. This sensor generates digital data that represent the encoder actual position. From the position
information, speed and direction of motion is calculated. The position is not lost even if the encoder is powered
down, which means
that it is not necessary to move to a reference position as with incremental type encoders. The
following table shows the absolute encoder inputs electrical specifications.
Specification
Value
Type of inputs
Differential / Single ended
ESD protected
ESD capability
IEC 61000-4-2 (ESD) ± 30 kV (air), ± 30 kV (contact)
IEC 61000-4-5; tp = 8/20
μ
s 12 A, 200 W
Maximum operating voltage
range
-0.5 ~ 5.5 V
Operating frequency
100 kHz to 10 MHz (user configurable)
Receiver hysteresis
min 50 mV typ 80 mV (DATA+ - DATA-)
Termination
220
Ω
differential on data line
Fail safe bias resistors
ENC_x+ (positive input) 500
Ω
to 5 V
ENC_x- (negative input) 500
Ω
to 2.5 V (equivalent)
Next Figure shows how to connect a single SSI or
BISS-C
absolute encoder to the Everest XCR servo drive.
Velocity control with Halls
Due to the inherent low resolution of motor mounted Hall sensors, they are not recommended for velocity
feedback in low speed applications.