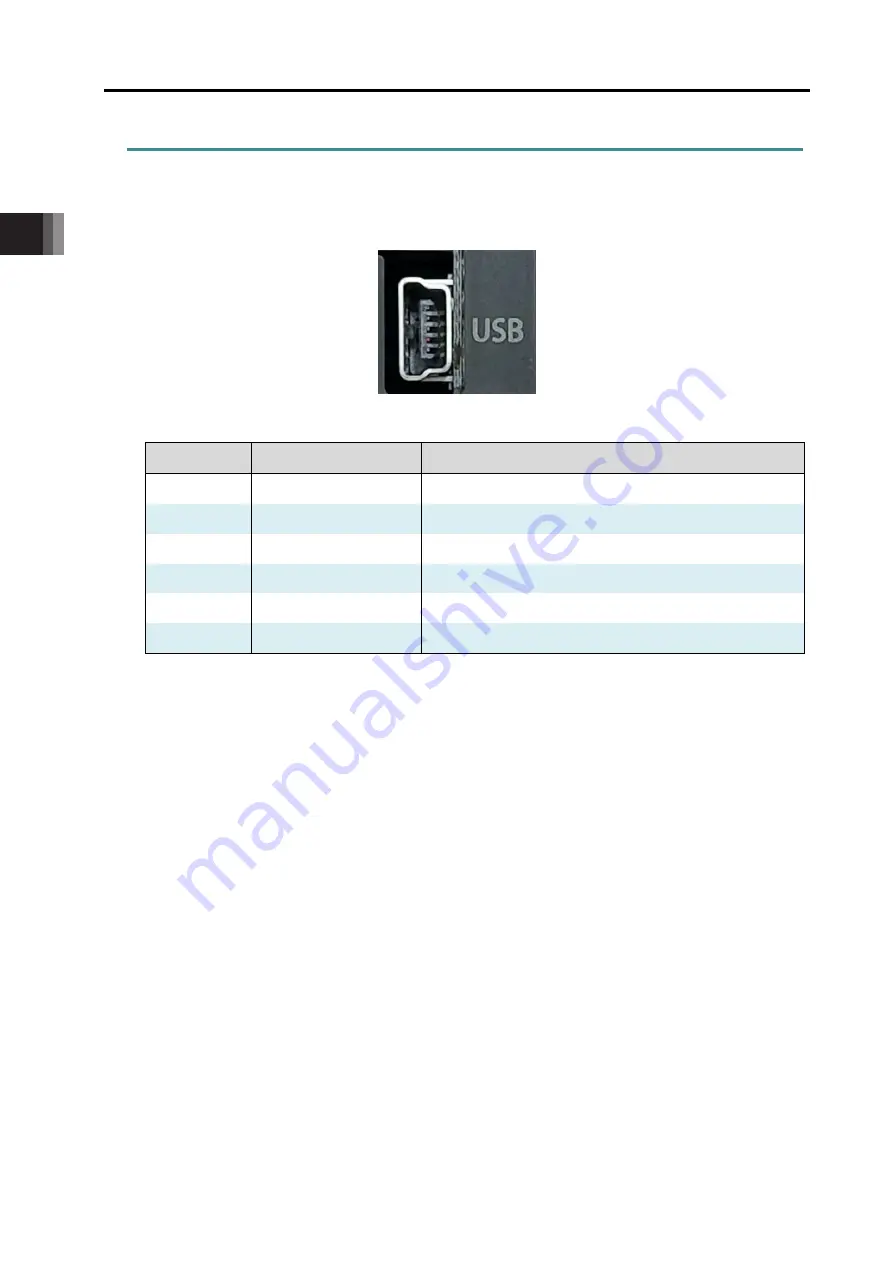
Chapter 2 EC Gateway Unit
2.4 Part Names/Functions and External Dimensions
2-10
ME0394-1A
2.4.5 USB connector
It is a connector to be connected to the PC software or gateway parameter configuration tool.
For use, it is necessary to install the USB connection driver for RCON.
For how to install the driver, refer to “PC software Instruction Manual (ME0155)”.
Connector name: 51387-0530 (Molex)
Pin No.
Signal name
Description
1
VBUS
USB power
2
D-
USB signal line -
3
D+
USB signal line +
4
NC
Not connected
5
GND
0 V
Shell
GND
0 V
5
1
Summary of Contents for Rec
Page 2: ......
Page 133: ...Parameter 6 1 Parameter list 6 1 6 2 Parameter Details 6 2 R E C Chapter 6 ...
Page 156: ......
Page 157: ......
Page 158: ......