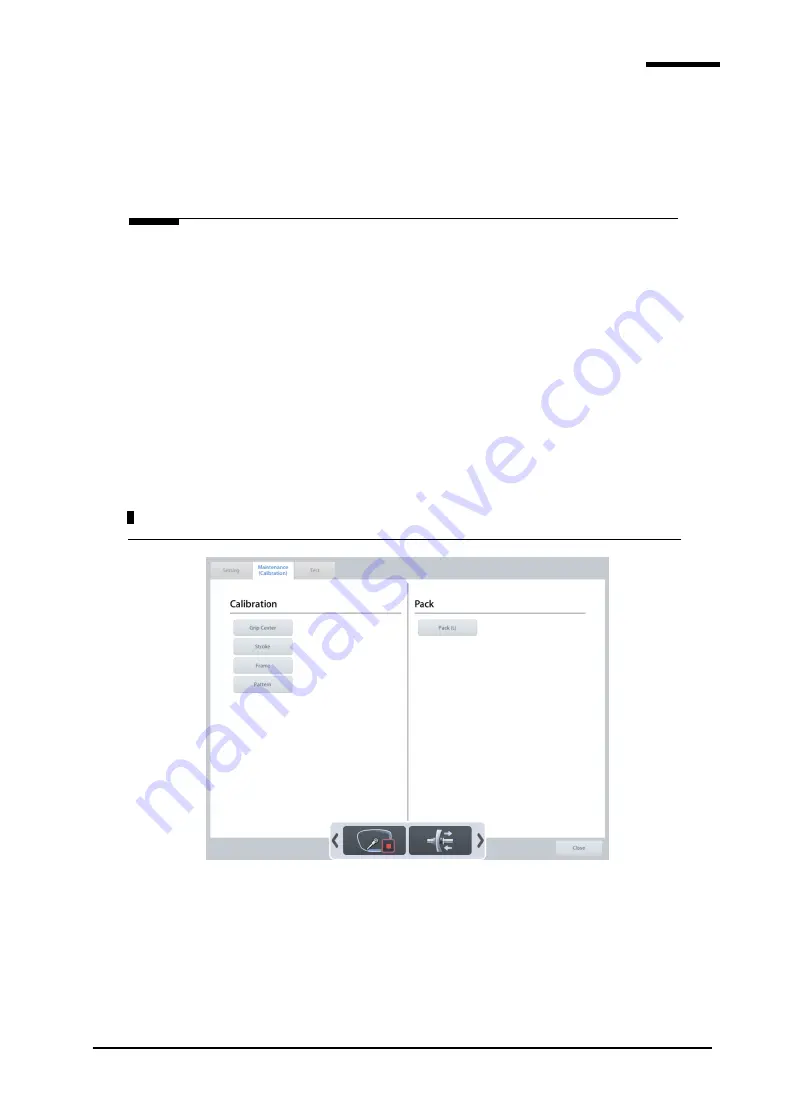
139
HPE-410
System Maintenance
8.1.
Automatic Calibration of Built-in Frame Reader
Automatic Calibration of Frame Reader is required with the following cases,
•
When the Size or Axis value of the traced data seems to have a problem,
•
When the Frame Reader seems to have a problem in operating normally.
Automatic calibration of frame reader consists of three parts: Stroke, Frame, Pattern. If any changes in
Stylus occur, Stroke calibration must be executed at first. The order of calibration is like this: Stroke ->
Frame -> Pattern.
Calibration Screen
8
Summary of Contents for HPE-410
Page 1: ...PATTERNLESS EDGER HPE 410 USER MANUAL...
Page 149: ...149 HPE 410 8 4 6 Clamp You can check clamp Clamp test Clamp sensor state 1 2...
Page 166: ...166 10 3 Drawings of System 10 3 1 Drawings of Edger...
Page 167: ...167 HPE 410 10 3 2 Drawings of Blocker HMB 8000 10 3 3 Drawings of Blocker CBK 4000...