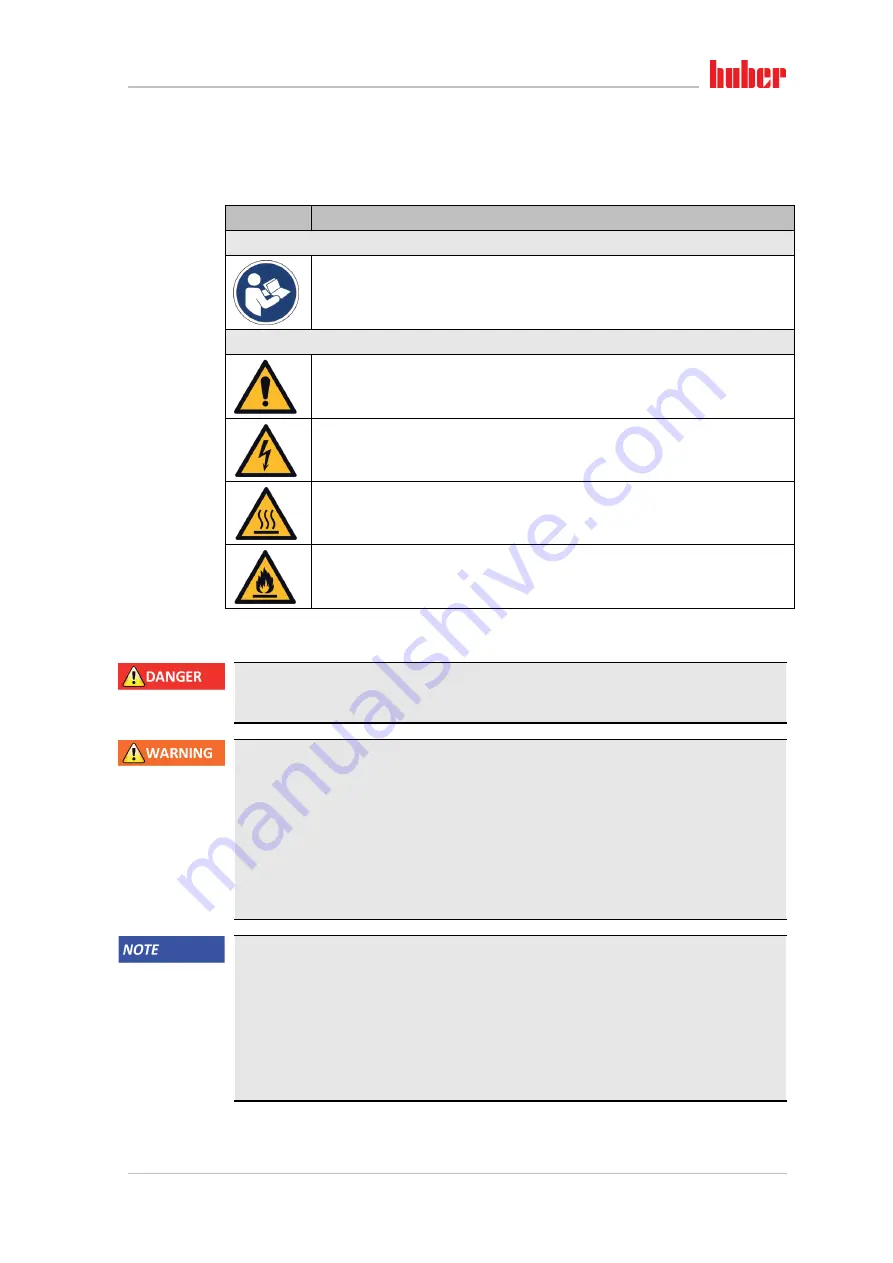
Introduction
Chapter 1
OPERATION MANUAL
V2.4.0en/08.12.20//17.12
CC®-Immersion circulator
13
1.2.2
Representation of safety identifiers
The following pictograms are used as safety identifiers. The table gives an overview of the safety
identifier used here.
Identifier
Description
Mandatory sign
- Observe the instructions
Warning sign
- General warning sign
- observe the instructions
- Warning of electrical voltage
- Warning of hot surface
- Warning of flammable substances
1.2.3
Proper operation
Operating the temperature control unit in a potentially explosive area
DEATH THROUGH EXPLOSION
Do NOT install or start up the temperature control unit within an ATEX zone.
Improper use
SERIOUS INJURY AND PROPERTY DAMAGE
Store the operation manual where it is easy to access in close proximity to the temperature
control unit.
Only adequately qualified operators may work with the temperature control unit.
Operators must be trained before handling the temperature control unit.
Check that the operators have read and understood the operation manual.
Define precise responsibilities of the operators.
Personal protective equipment must be provided to the operators.
Be sure to follow the responsible body’s safety rules to protect life and limb and to limit dam-
ages!
Modifications to the temperature control unit by third-parties
DAMAGE TO THE TEMPERATURE CONTROL UNIT
Do not allow third parties to make technical modifications to the temperature control unit.
The EU declaration of conformity becomes invalid if any modifications are made to the tem-
perature control unit without the approval of Huber.
Only specialists trained by Huber may carry out modifications, repairs or maintenance work.
The following must be observed without fail:
Only use the temperature control unit in a fault-free condition!
Have the start-up and repairs carried out by specialists only!
Do not ignore, bypass, dismantle or disconnect any safety devices!
Overview