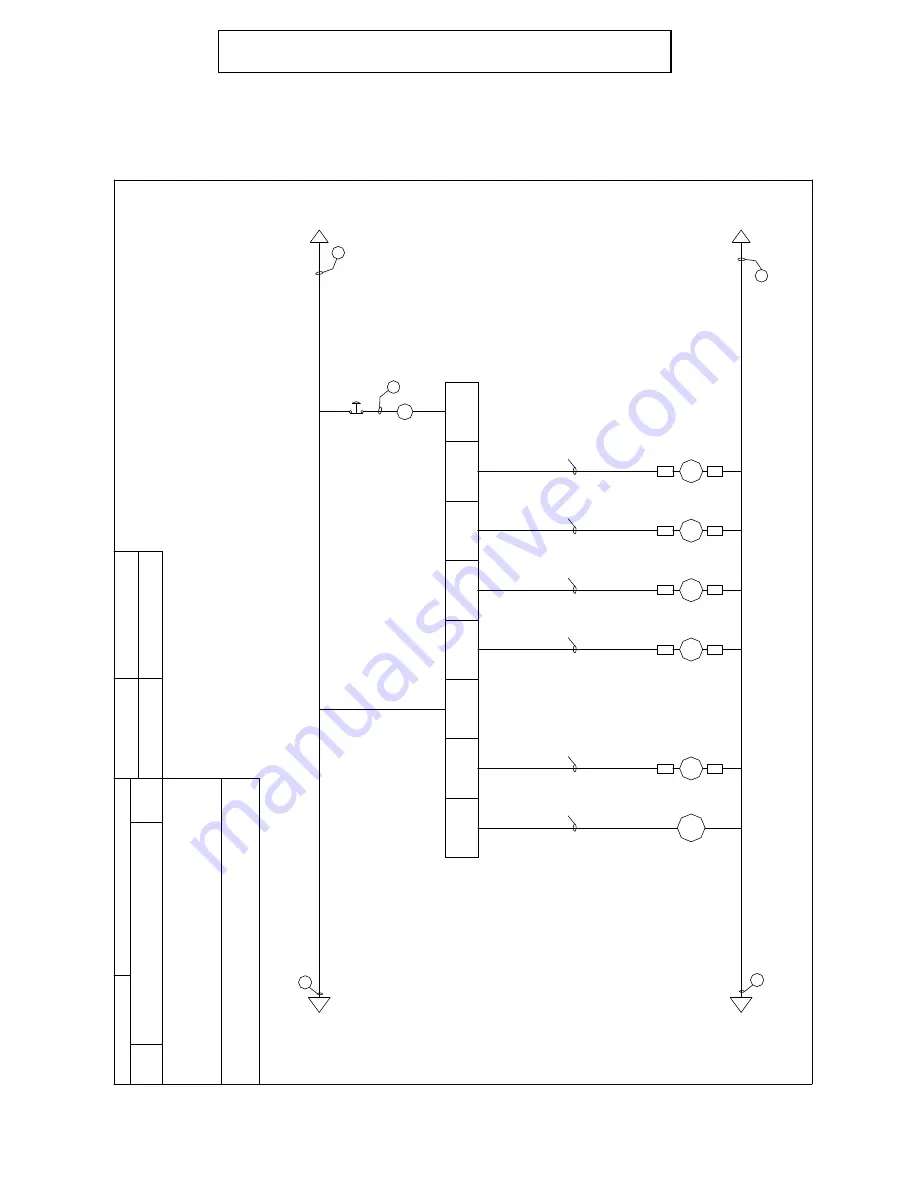
41
WFS 101545 Operations Manual
A1
A1
A1
C4
Y6
Y5
PLC OUTPUTS
Y2
Y3
Y4
PB-10
E-STOP
TB2
C3
Y1
W
F
S
1
0
15
4
5
E
L
E
C
T
R
IC
A
L
S
C
H
E
M
A
T
IC
W
IT
H
P
LC
V
1
S
H
E
E
T
O
F
1
35
7
R
O
U
T
E
3
A
, B
O
W
, N
H
0
3
3
04
H
S
T
S
P
IN
D
LE
S
L
LC
7
A
R
E
V
3
1
2-
0
1
-2
0
21
D
W
G
N
o
.
W
F
S
2
5
0
0
3
A
S
IZ
E
T
IT
LE
D
R
A
W
N
C
.V
A
L
E
N
Z
E
D
A
T
E
D
A
T
E
C
H
K
D
3
+24
TO SHEET
4
TO SHEET
4
-0
2
FROM SHEET 2
+24
COM
FROM SHEET 2
SL-1
SONALERT
AUDIBLE ALARM
Y4
Y2
Y1
3
A2
C-3
C-2
A2
CHILLER
CONTACTOR
PUMP 2
CONTACTOR
PROCESS
A2
C-1
PUMP 1
CONTACTOR
RECIRCULATING
2
4
A2
Y2
C-2
A1
A2
Y6
A1
CR-2
Y5
PUMP 3
CONTACTOR
SPINDLE
CHILLER
ZONE 1 SOLENOID
ELECTRICAL SCHEMATIC
SHEET 3 OF 7