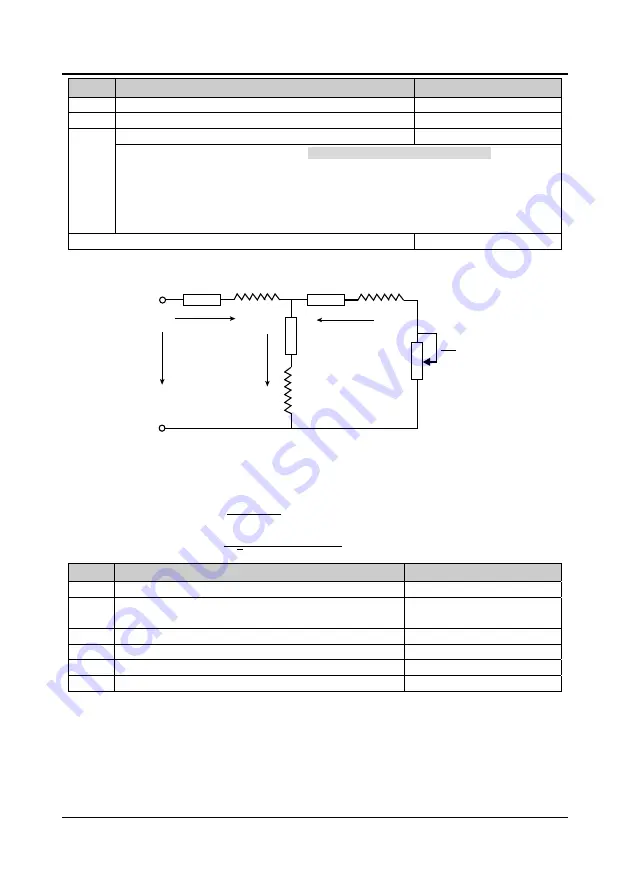
Chapter 6 Function Introduction
Shenzhen Hpmont Technology Co., Ltd.
―
60
―
HD5L Series Controller User Manual V1.4
Ref. Code
Function Description
Setting Range [Default]
F06.14
No weighing current coefficient
0 - 9999 [3000]
F06.15
No weighing speed-loop KP
1 - 9999 [2000]
F06.16
No weighing speed-loop KI
1 - 9999 [2000]
F06.14 - F06.16 are used to adjust the effect of no weighing auto-compensation (F06.00 = 4).
•
The system response can be expedited through increasing F06.14 - F0616, but system oscillation and
overshoot may occur if the value of F06.14 - F0616 is too high.
•
Generally, it can smoothly start elevator via adjusting F06.14 when debugging.
•
Increase F06.14 to avoid sliding vehicle at starting moment. Decrease F06.17 to avoid shake at starting
moment.
F06.17 - F06.20 Unused
6.2.8
F07: Asyn. motor Parameters
The relationship between rated torque current, excitation current and rated current of motor is:
Rated
torque
current
F07
.
05
F07
.
02
Excitation
current
F07
.
11
1
F07
.
05
2
F07
.
02
Mutual
inductance
F07
.
10
F07
.
01
2
√
3π
F07
.
03
F07
.
11
F07
.
09
Ref. Code
Function Description
Setting Range [Default]
F07.00
Rated power of asyn. motor
0.2 - 500.0kW [Depend on HD5L]
F07.01
Rated voltage of asyn. motor
0V - Controller rated voltage
[Depend on HD5L]
F07.02
Rated current of asyn. motor
0.0 - 999.9A [Depend on HD5L]
F07.03
Rated frequency of asyn. motor
1.00 - 100.00 [50.00Hz]
F07.04
Rated Rpm of asyn. motor
1 - 24000 [1440rpm]
F07.05
Power factor of asyn. motor
0.001 - 1.000 [Depend on HD5L]
L
m
R1=F07.07 (Stator resistance)
R2=F07.08 (Rotor resistance)
Io=F07.11 (Excitation current)
R1
R2
LI
I1
I2
S
1-S
R2
LI
LI=F07.09 (Leakage inductance)
Lm=F07.10 (Mutual inductance)
S=Slip ratio
U1
Io