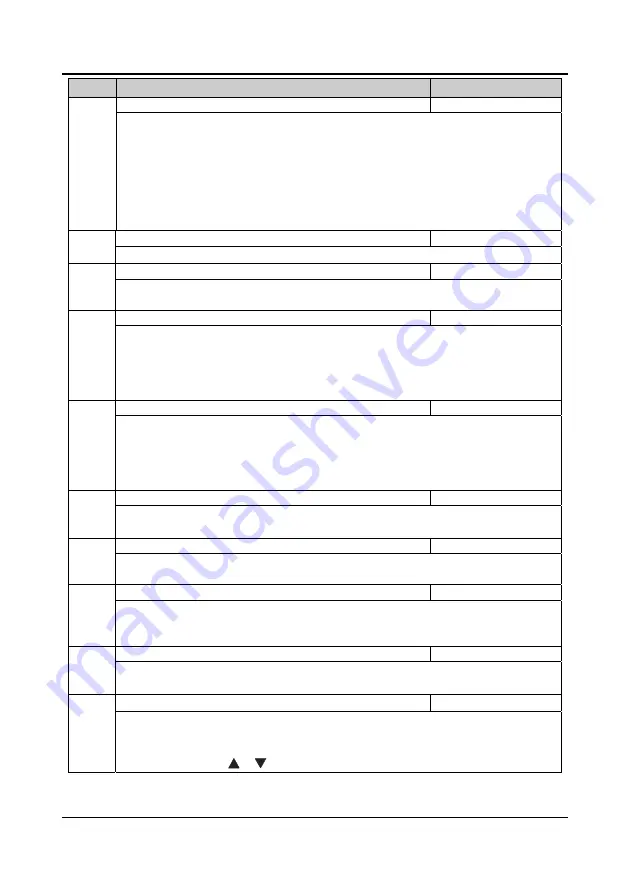
Chapter 6 Function Introduction
Shenzhen Hpmont Technology Co., Ltd.
―
58
―
HD31 Series User Manual V1.1
Ref. Code
Name Description
Setting Range [Default]
P02.26
T12 time pressure
0.0 - P05.03
×
10 [0.0 kg/cm
2
]
Used for time setting of multi-time pressure water supply and the pressure setting of the corresponding
time.
•
Principle of time setting: T1 ≤ T2 ≤ T3 ≤ T4 ≤ T5 ≤ T6 ≤ T7 ≤ T8 ≤ T9 ≤ T10 ≤ T11 ≤ T12.
•
T1 refers to the beginning of T1 till beginning of T2; T2 refers to the beginning of T2 till the beginning of
T3, and so forth. T12 refer to the beginning of T12 till the beginning of T1.
•
The beginning time of a certain period may be the same as its' previous one. In this case, the previous
one joins to this period.
•
There is only one period per day if T1 = T2 = T3 = T4 = T5 = T6 = T7 = T8 = T9 = T10 = T11 = T12.
P02.27
Upper limit of pressure closed-loop
0 - upper limit [50.00Hz]
Max. frequency of closed-loop regulator output.
P02.28
Proportional gain of pressure closed-loop (Kp)
0.00 - 10.00 [0.01]
Defines the proportional gain, decides the adjustment intensity of the regulator: the bigger KP is, the
higher intensity will be.
P02.29
Integration time of pressure closed-loop (Ti)
0.01 - 10.00 [0.10s]
Defines the integration time (Ti), and decides the speed of integration adjustment. The regulator makes
adjustment for the tolerance of feedback / setting pressure.
•
When the tolerance of feedback / setting pressure is 100%, the integral regulator, with the continuous
adjustment of P02.29, reaches the max. pressure (overlook the effect of P02.28 and P02.30).
•
The shorter integration time is, the faster adjustment speed will be.
P02.30
Differential time of pressure closed-loop (Td)
0.00 - 1.00 [0.00s]
Differential time decides the intensity of integration adjustment. The regulator makes adjustment for the
tolerance change of the feedback / setting pressure.
•
The adjustment of the derivative adjustment is max. pressure if the feedback pressure changes 100%
within P02.30 (overlook the effect of P02.28 and P02.29).
•
The longer integration time is, the higher adjustment intensity will be.
P02.31
Sampling time (T)
0.01 - 30.00 [0.50s]
Defines sampling time of feedback value. The regulator calculates once during every sampling period.
•
The longer sampling time is, the slower response will be.
P02.32 Bias
limit
0.0 - 20.0 [2.0%]
The output value of the regulator is relevant to the max. tolerance of pressure setting. Within permitted
range, the regulator stops regulating.
P02.33
Output wave filter of pressure closed-loop
0.01 - 30.00 [0.50s]
Make wave filter to the output frequency signal of the regulator, and avoid the jumping interfering signal to
influence on the system.
•
Adjustment sensitivity is affected by overlong time of wave filtering.
P02.34
Regulating characteristic of pressure closed-loop
0,1 [0]
0: Positive characteristic. When the setting is added, pressure increases.
1: Negative characteristic. When the setting is added, pressure decreases.
P02.35
Digital setting for saving selection when power failure
0,1 [1]
0: Not saving.
1: Saving.
When P02.00 = 0 and inverter is in stop/running, setted pressure is displaying. We can adjust the setted
pressure through button
or
. After power failure, adjusted pressure value can be saved by P02.35.