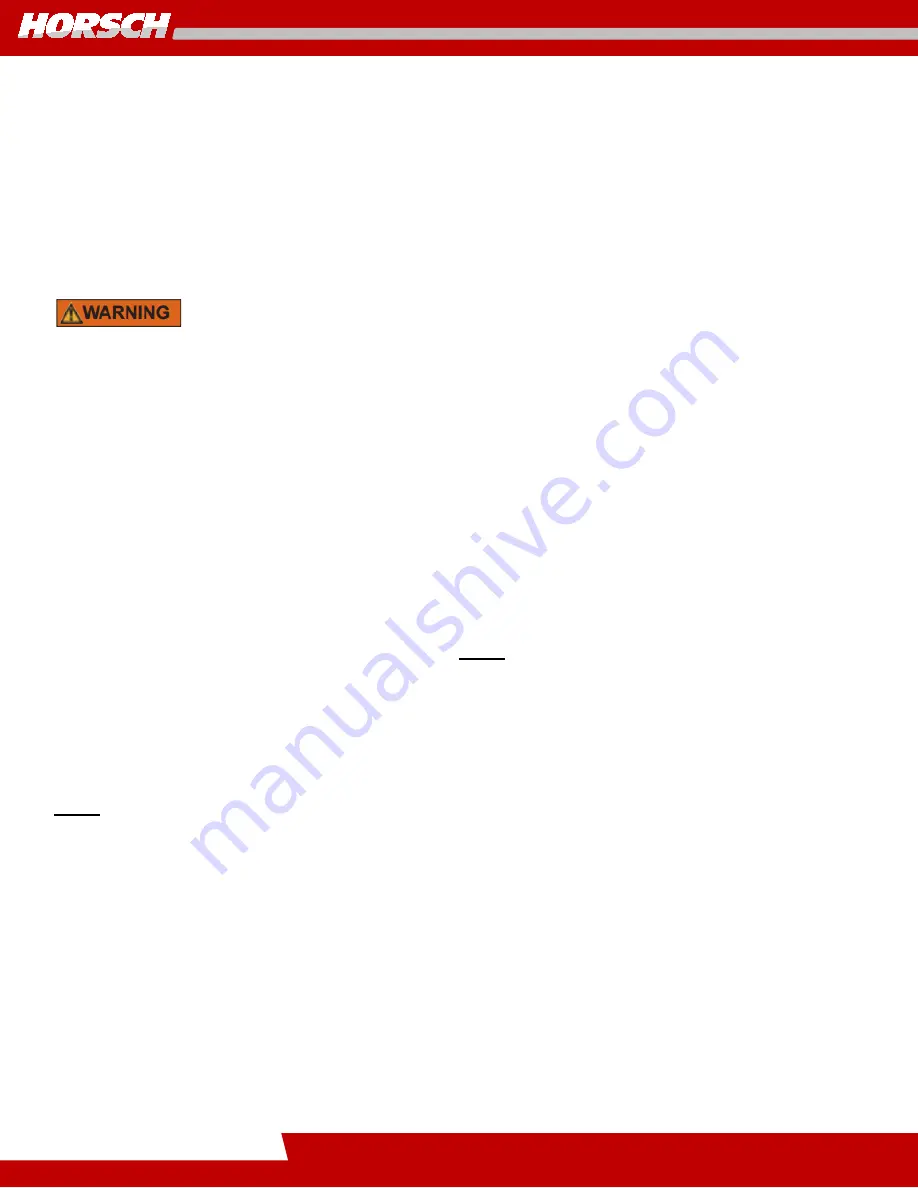
60 Maestro SW Owner’s Manual – Ver. 2.4 11/2018
www.horsch.com
Parking the Machine
Thoroughly clean the tanks and fertilizer
equipment. Corrosion to components is at
higher risk when left uncleaned.
Park the drill in a shed or under a roof so that no
moisture can accumulate in the tanks, metering
unit or seed tubes.
With negative drawbar load, the machine may tilt
back and cause severe injury to persons. Lower
the machine correctly before unhitching!
Parking
1. Always park the machine horizontally on
firm ground. Shut down the tractor.
2. Secure the machine with wheel chocks
against rolling away.
3. Unfold the machine.
4. Lower the seed toolbar.
5. Disconnect hydraulic and electrical
connections. Attach to the hydraulic
hose holder and electrical plug holder
located on the front hitch.
6. Use the front mounted lift jack to raise the
machine weight off the tractor rear
drawbar slightly.
7. Remove the hitch pin to unhitch the
machine.
NOTE: The machine may be parked and
unhitched in a folded position, providing
extra precaution is taken, but is not
recommended.
Cleaning
Always wear the required protective equipment
when cleaning. Harmful dusts or chemicals may
have deposited in the area of pneumatics and
hydraulics of the machine, along with the
metering units.
1. Empty the tanks.
2. Clean metering units, SOD system,
hoses and liquid fertilizer system.
3. Open the covers on the end of the toolbar
for the vacuum system. Use compressed
air to thoroughly clean any seed and
dressing residues.
Storage (end of season)
1. Park the machine in an undisturbed area,
out of the way of other equipment.
2. Follow procedures above for proper
cleaning.
3. Follow procedures above for proper
parking of the machine.
4. Follow procedures above for proper
unhitching of the machine.
NOTE: In colder off-season climates, it may
be necessary to winterize the liquid system
with RV antifreeze to avoid possible damage
to hoses and pump.
Summary of Contents for Maestro SW 1630
Page 2: ...2 Maestro SW Owner s Manual Ver 2 4 11 2018 www horsch com...
Page 3: ...Maestro SW Owner s Manual Ver 2 4 11 2018 3 www horsch com...
Page 10: ...10 Maestro SW Owner s Manual Ver 2 4 11 2018 www horsch com...
Page 11: ...Maestro SW Owner s Manual Ver 2 4 11 2018 11 www horsch com Section 1 General Information...
Page 14: ...14 Maestro SW Owner s Manual Ver 2 4 11 2018 www horsch com...
Page 16: ...16 Maestro SW Owner s Manual Ver 2 4 11 2018 www horsch com...
Page 18: ...18 Maestro SW Owner s Manual Ver 2 4 11 2018 www horsch com...
Page 20: ...20 Maestro SW Owner s Manual Ver 2 4 11 2018 www horsch com...
Page 22: ...22 Maestro SW Owner s Manual Ver 2 4 11 2018 www horsch com...
Page 26: ...26 Maestro SW Owner s Manual Ver 2 4 11 2018 www horsch com Notes...
Page 27: ...Maestro SW Owner s Manual Ver 2 4 11 2018 27 www horsch com Section 2 Safety...
Page 29: ...Maestro SW Owner s Manual Ver 2 4 11 2018 29 www horsch com...
Page 30: ...30 Maestro SW Owner s Manual Ver 2 4 11 2018 www horsch com...
Page 38: ...38 Maestro SW Owner s Manual Ver 2 4 11 2018 www horsch com Notes...
Page 39: ...Maestro SW Owner s Manual Ver 2 4 11 2018 39 www horsch com Section 3 Specifications...
Page 50: ...50 Maestro SW Owner s Manual Ver 2 4 11 2018 www horsch com Notes...
Page 51: ...Maestro SW Owner s Manual Ver 2 4 11 2018 51 www horsch com Section 4 Hydraulics...
Page 54: ...54 Maestro SW Owner s Manual Ver 2 4 11 2018 www horsch com Notes...
Page 55: ...Maestro SW Owner s Manual Ver 2 4 11 2018 55 www horsch com Section 5 Operation...
Page 77: ...77 Maestro SW Owner s Manual Ver 1 1 09 2016 www horsch com Maestro Metering Disks Components...
Page 91: ...91 Maestro SW Owner s Manual Ver 1 1 09 2016 www horsch com Possible Faults Remedy...
Page 102: ...102 Maestro SW Owner s Manual Ver 1 1 09 2016 www horsch com Notes...
Page 103: ...Maestro SW Owner s Manual Ver 2 4 11 2018 103 www horsch com Section 6 Optional Equipment...
Page 120: ...120 Maestro SW Owner s Manual Ver 2 4 11 2018 www horsch com Notes...
Page 121: ...Maestro SW Owner s Manual Ver 2 4 11 2018 121 www horsch com Section 7 Maintenance Service...
Page 130: ...130 Maestro SW Owner s Manual Ver 2 4 11 2018 www horsch com Notes...