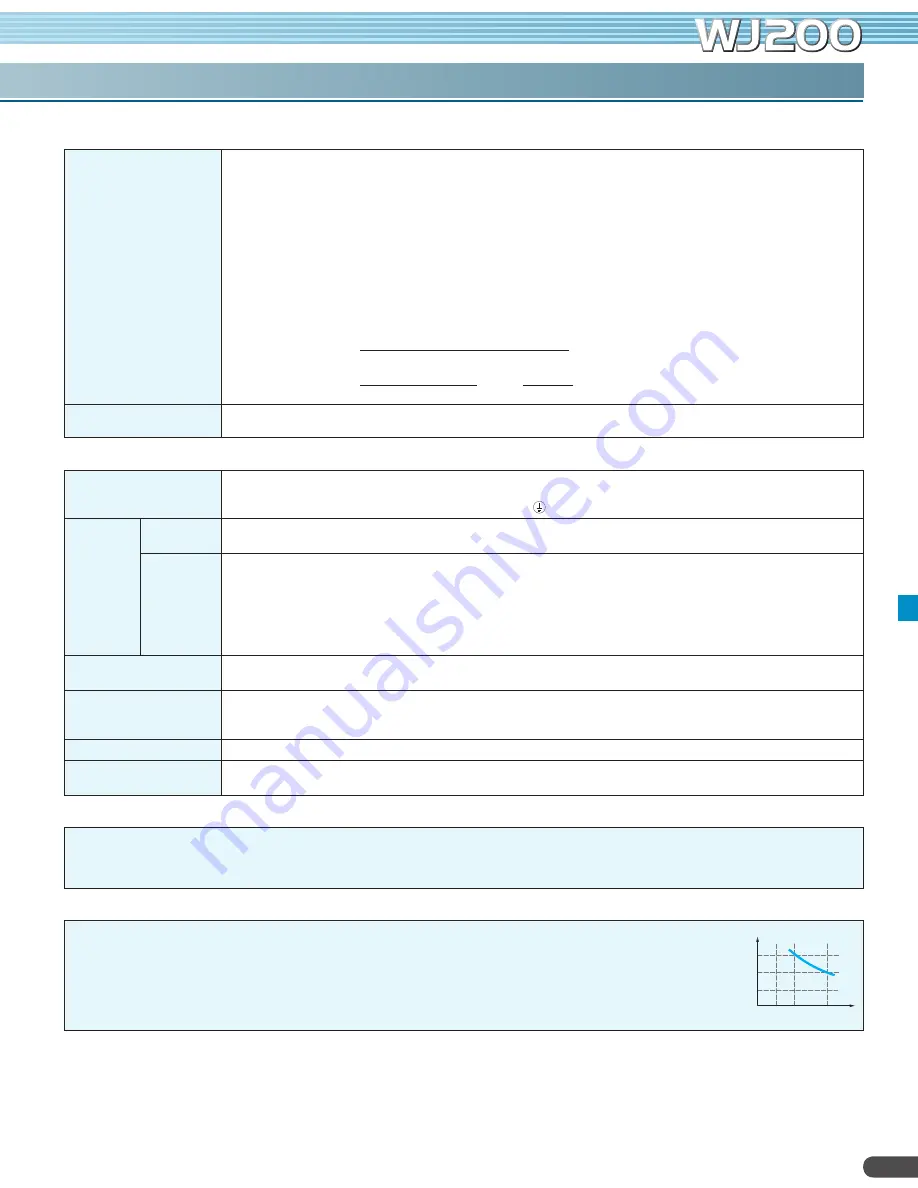
27
Installation of an AC reactor
on the input side
In the following examples involving a general-purpose inverter, a large peak current flows on the main power supply side, and is able to destroy
the converter module. Where such situations are foreseen or the connected equipment must be highly reliable, install an AC reactor between the
power supply and the inverter. Also, where influence of indirect lightning strike is possible, install a lightning conductor.
(A) The unbalance factor of the power supply is 3% or higher. (Note)
(B) The power supply capacity is at least 10 times greater than the inverter capacity (the power supply capacity is 500 kVA or more).
(C) Abrupt power supply changes are expected.
Examples:
(1) Several inverters are interconnected with a short bus.
(2) A thyristor converter and an inverter are interconnected with a short bus.
(3) An installed phase advance capacitor opens and closes.
In cases (A), (B) and (C), it is recommended to install an AC reactor on the main power supply side.
Note: Example calculation with V
RS
= 205V, V
ST
= 201V, V
TR
= 200V (V
RS
: R-S line voltage, V
ST
: S-T line voltage, V
TR
: T-R line voltage)
Unbalance factor of voltage = X 100
= X 100 = X 100 = 1.5 (%)
Using a private power generator
An inverter run by a private power generator may overheat the generator or suffer from a deformed output voltage waveform of the generator.
Generally, the generator capacity should be five times that of the inverter (kVA) in a PWM control system, or six times greater in a PAM control system.
(
1) High-frequency components are included in the input / output of the inverter main circuit, and they may cause interference in a transmitter, radio, or sensor if used near the inverter.
The interference can be minimized by attaching noise filters (option) in the inverter circuitry.
(2) The switching action of an inverter causes an increase in leakage current. Be sure to ground the inverter and the motor.
Wiring connections
(1) Be sure to connect main power wires with R (L1), S (L2), and T (L3) terminals (input) and motor wires to U (T1), V (T2), and W (T3) terminals (output).
(Incorrect connection will cause an immediate failure.)
(2) Be sure to provide a grounding connection with the ground terminal ( ).
Wiring between
inverter and
motor
Electro-magnetic
contactor
When an electromagnetic contactor is installed between the inverter and the motor, do not perform on-off switching during running operation.
Thermal relay
When used with standard applicable output motors (standard three-phase squirrel-cage four-pole motors), the WJ200 Series does not need a
thermal relay for motor protection due to the internal electronic protective circuit. A thermal relay, however, should be used:
• during continuous running outside a range of 30 to 60 Hz.
• for motors exceeding the range of electronic thermal adjustment (rated current).
• when several motors are driven by the same inverter; install a thermal relay for each motor.
• The RC value of the thermal relay should be more than 1.1 times the rated current of the motor. Where the wiring length is 10 m or more, the
thermal relay tends to turn off readily. In this case, provide an AC reactor on the output side or use a current sensor.
Installing a circuit breaker
Install a circuit breaker on the main power input side to protect inverter wiring and ensure personal safety. Choose an inverter-compatible circuit breaker.
The conventional type may malfunction due to harmonics from the inverter. For more information, consult the circuit breaker manufacturer.
Wiring distance
The wiring distance between the inverter and the remote operator panel should be 20 meters or less. When this distance is exceeded, use CVD-E (current-
voltage converter) or RCD-E (remote control device). Shielded cable should be used on the wiring. Beware of voltage drops on main circuit wires.
(A large voltage drop reduces torque.)
Earth leakage relay
If the earth leakage relay (or earth leakage breaker) is used, it should have a sensitivity level of 15 mA or more (per inverter).
Phase advance capacitor
Do not use a capacitor for power factor improvement between the inverter and the motor because the high-frequency components of the inverter
output may overheat or damage the capacitor.
Max. line voltage (min.) – Mean line voltage
Mean line voltage
Because a DC bus capacitor deteriorates as it undergoes internal chemical reaction, it should normally be replaced every 10 years. (10 years is not the
guaranteed lifespan but rather, the expected design lifeplan.) Be aware, however, that its life expectancy is considerably shorter when the inverter is
subjected to such adverse factors as high temperatures or heavy loads exceeding the rated current of the inverter.
JEMA standard is the 5 years at ambient temperature 40
º
C used in 12 hours daily. (according to the “Instructions for Periodic Inspection of General-
Purpose Inverter” (JEMA))
Also, such moving parts as a cooling fan should be replaced. Maintenance inspection and parts replacement must be performed by only specified trained personnel.
V
RS
− (V
RS
+ V
ST
+ V
TR
) /3
(V
RS
+ V
ST
+ V
TR
) /3
205− 202
202
[Main power supply]
Notes on Peripheral Equipment Selection
High-frequency Noise and Leakage Current
Lifetime of Primary Parts
50
40
30
Am
bi
en
t t
em
pe
ra
tu
re (
º
C)
2.5
5
10
Capacitor lifetime (years)
Information in this brochure is subject to change without notice.
For Correct Operation
Stöwer Antriebstechnik GmbH, Enneststrasse 3, 51702 Bergneustadt, tel: 02261-40970, Fax: 02261-41309