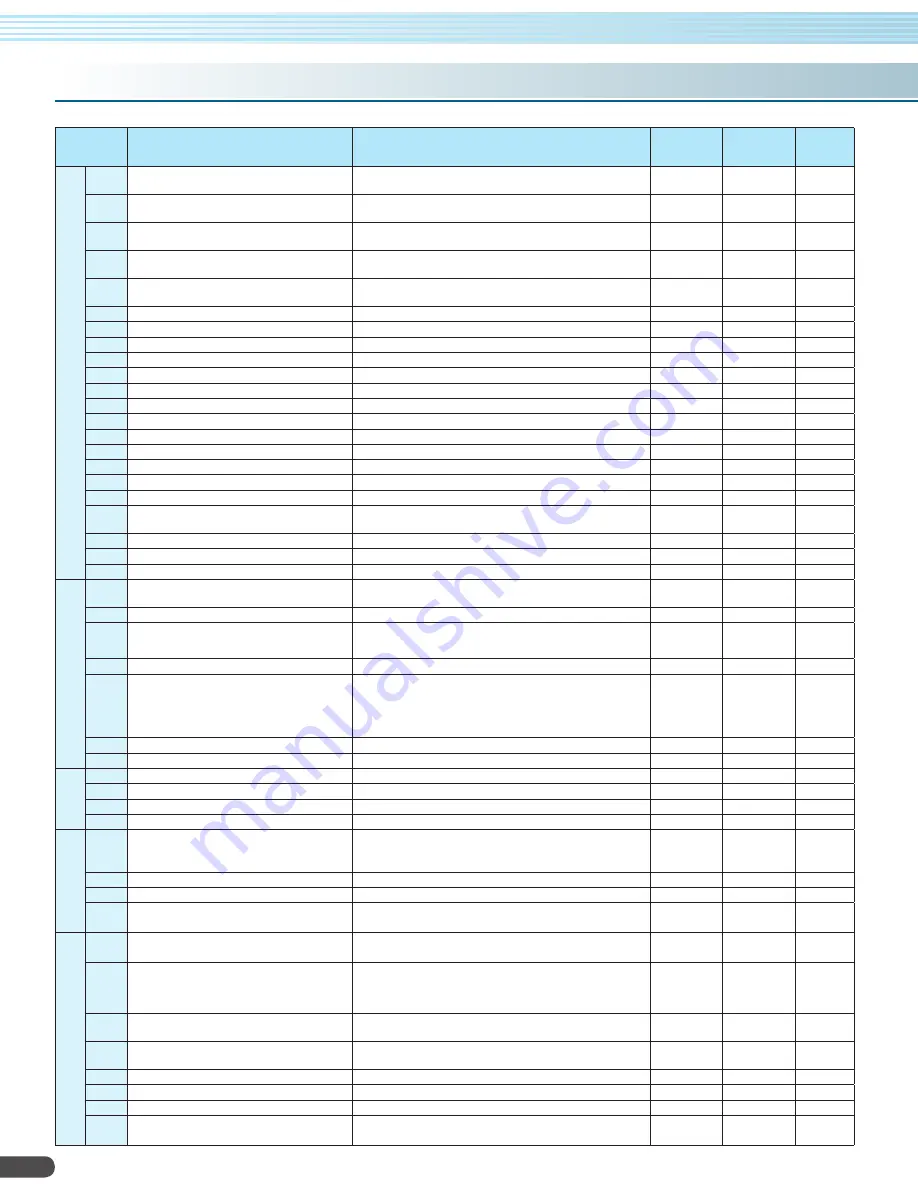
18
Function List
Code
Function Name
Setting Range
Setting During
Operation
(allowed or not)
Change During
Operation
(allowed or not)
Default
Setting
Le
ve
ls a
nd o
ut
pu
t t
er
m
in
al s
ta
tu
s
C038
Output mode of low load detection signal
00 (output during acceleration/deceleration and constant-speed operation) /
01 (output only during constant-speed operation)
×
○
01
C039
Low load detection level
Set range: 0 to 200% of inverter rated current [A]
○
○
Rated current
of inverter
C040
Output mode of overload warning
00 (output during acceleration / deceleration and constant-speed operation) /
01 (output only during constant-speed operation)
×
○
01
C041
Overload level setting
Set range: 0 to 200% of inverter rated current [A]
○
○
115% of
Rated current
C241
Overload level setting, 2nd motor
Set range: 0 to 200% of inverter rated current [A]
○
○
115% of
Rated current
C042
Frequency arrival setting for acceleration
0.00 to 99.99 / 100.0 to 400.0 [Hz]
×
○
0.00
C043
Frequency arrival setting for deceleration
0.00 to 99.99 / 100.0 to 400.0 [Hz]
×
○
0.00
C044
PID deviation level setting
0.0 to 100.0 [%]
×
○
3.0
C045
Frequency arrival signal for acceleration (2)
0.00 to 99.99 / 100.0 to 400.0 [Hz]
×
○
0.00
C046
Frequency arrival signal for deceleration (2)
0.00 to 99.99 / 100.0 to 400.0 [Hz]
×
○
0.00
C047
Pulse train input scale conversion for EO output
0.01 to 99.99
○
○
1.00
C052
PID FBV function high limit
0.0 to 100.0 [%]
×
○
100.0
C053
PID FBV function variable low limit
0.0 to 100.0 [%]
×
○
0.0
C054
Over-torque / under-torque selection
00 (Over torque) / 01 (under torque)
×
○
00
C055
Over / under-torque level (Forward powering mode)
0 to 200 [%]
×
○
100
C056
Over / under-torque (Reverse regen. mode)
0 to 200 [%]
×
○
100
C057
Over / under-torque (Reverse powering mode)
0 to 200 [%]
×
○
100
C058
Over / under-torque level (Forward regen. mode)
0 to 200 [%]
×
○
100
C059
Signal output mode of Over / under torque
00 (output during acceleration / deceleration and constant-speed operation) /
01 (output only during constant-speed operation)
×
○
01
C061
Electronic thermal warning level setting
0 to 100 [%]
×
○
90
C063
Zero speed detection level setting
0.00 to 99.99 / 100.0 [Hz]
×
○
0.00
C064
Heat sink overheat warning
0. to 110. [
º
C]
×
○
100
Co
m
m
un
ic
at
ion
func
tion
C071
Communication speed selection
03 (2400bps) / 04 (4800bps) / 05 (9600bps) / 06 (19200bps) / 07 (38400bps) /
08 (57600bps) / 09 (76800bps) / 10 (115200bps)
×
○
05
C072
Node allocation
1 to 247
×
○
1
C074
Communication parity selection
00 (no parity) /
01 (even parity) /
02 (odd parity)
×
○
00
C075
Communication stop bit selection
1 (1bit) / 2 (2bit)
×
○
1
C076
Communication error select
00 (tripping) /
01 (tripping after decelerating and stopping the motor) /
02 (ignoring errors) /
03 (stopping the motor after free-running) /
04 (decelerating and stopping the motor)
×
○
02
C077
Communication error time-out
0.00 to 99.99 [s]
×
○
0.00
C078
Communication wait time
0 to 1000 [ms]
×
○
0
A
dj
us
tm
ent
C081
O input span calibration
0. to 200.0 [%]
○
○
100.0
C082
OI input span calibration
0. to 200.0 [%]
○
○
100.0
C085
Thermistor input (PTC) span calibration
0. to 200.0 [%]
○
○
100.0
C091
00 (Disable) / 01 (Enable)
00
○
○
00
Co
m
m
un
ic
at
io
n
func
tion
C096
Communication selection
00 (Modbus-RTU) /
01 (EzCOM) /
02 (EzCOM [administrator])
×
×
00
C098
EzCOM start adr. of master
01 to 08
×
×
01
C099
EzCOM end adr. of master
01 to 08
×
×
01
C100
EzCOM starting trigger
00 (Input terminal) /
01 (Always)
×
×
00
Ot
he
rs
C101
UP / DWN memory mode selection
00 (not storing the frequency data) /
01 (storing the frequency data)
×
○
00
C102
Reset selection
00 (resetting the trip when RS is on) /
01 (resetting the trip when RS is off) /
02 (enabled resetting only upon tripping [resetting when RS is on]) /
03 (resetting only trip)
○
○
00
C103
Restart mode after reset
00 (starting with 0 Hz) / 01 (starting with matching frequency) /
02 (restarting with active matching frequency)
×
○
00
C104
UP / DWN clear: terminal input mode selection
00 (0Hz) /
01 (EEPROM data when power supply is turned on)
×
○
00
C105
EO gain adjustment
50 to 200 [%]
○
○
100
C106
AM gain adjustment
50 to 200 [%]
○
○
100
C109
AM bias adjustment
0 to 100 [%]
○
○
0
C111
Overload setting (2)
Set range: 0 to 200% of inverter rated current [A]
○
○
115% of
Rated current
Stöwer Antriebstechnik GmbH, Enneststrasse 3, 51702 Bergneustadt, tel: 02261-40970, Fax: 02261-41309