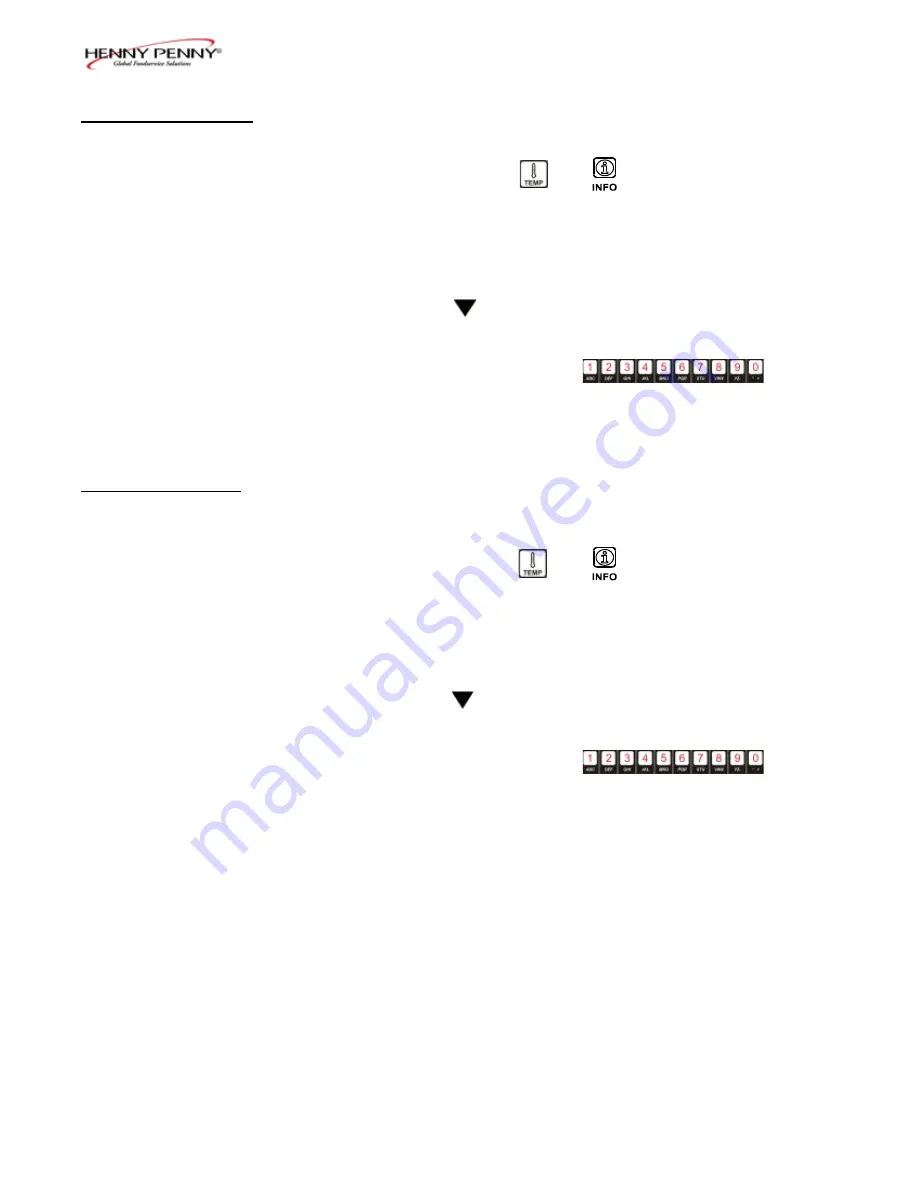
Model LVG-102, 103, 104
4-4
4-5. FILTER AFTER
The number of cook cycles between filtering the oil can easily
be programmed for all products.
1. Press and hold and buttons until LEVEL - 2
shows in the display, followed by ENTER CODE.
2. Enter code 1, 2, 3, 4 (first 4 product buttons). “PROD”
and “COMP” show in the displays.
3. Press button 4 times and “FILR AFTR” shows in the
left display.
4. Use the product buttons
to set the
number to cook cycles between filtering procedures from 0
to 99.
The length of time the fryer remains idle between cook cycles
before the controls suggest filtering.
1. Press and hold and buttons until LEVEL - 2
shows in the display, followed by ENTER CODE.
2. Enter code 1, 2, 3, 4 (first 4 product buttons). “PROD”
and “COMP” show in the displays.
3. Press button 5 times and “FILR TIME” shows in the
left display.
4. Use the product buttons
to set a
time between cook cycles from 0 to 18:00 hours.
For example, if “5:00” is programmed in the right display,
if the vat was not used for 5 hours after a cook cycle, the
controls would display “FILR NOW?” “YES NO”.
4-6. FILTER TIME
June 2008
Summary of Contents for LOV LVG-102
Page 2: ...Model LVG 102 103 104 2...
Page 21: ...Model LVG 102 103 104 3 6...
Page 71: ...Model LVG 102 103 104 8 7 1 2 1 3 4 6 5 7 8 9 10 11 12 5 13 14 15 14 17 16 4 Feb 2011...
Page 89: ...Model LVG 102 103 104 A 2 May 2016...
Page 90: ...Model LVG 102 103 104 A 3 May 2016...
Page 91: ...Model LVG 102 103 104 A 4 May 2016...
Page 92: ...Model LVG 102 103 104 A 5 May 2016...
Page 93: ...Model LVG 102 103 104 A 6 May 2016...
Page 94: ...Model LVG 102 103 104 A 7 May 2016...
Page 95: ...Model LVG 102 103 104 A 8 May 2016...
Page 96: ...Model LVG 102 103 104 A 9 May 2016...