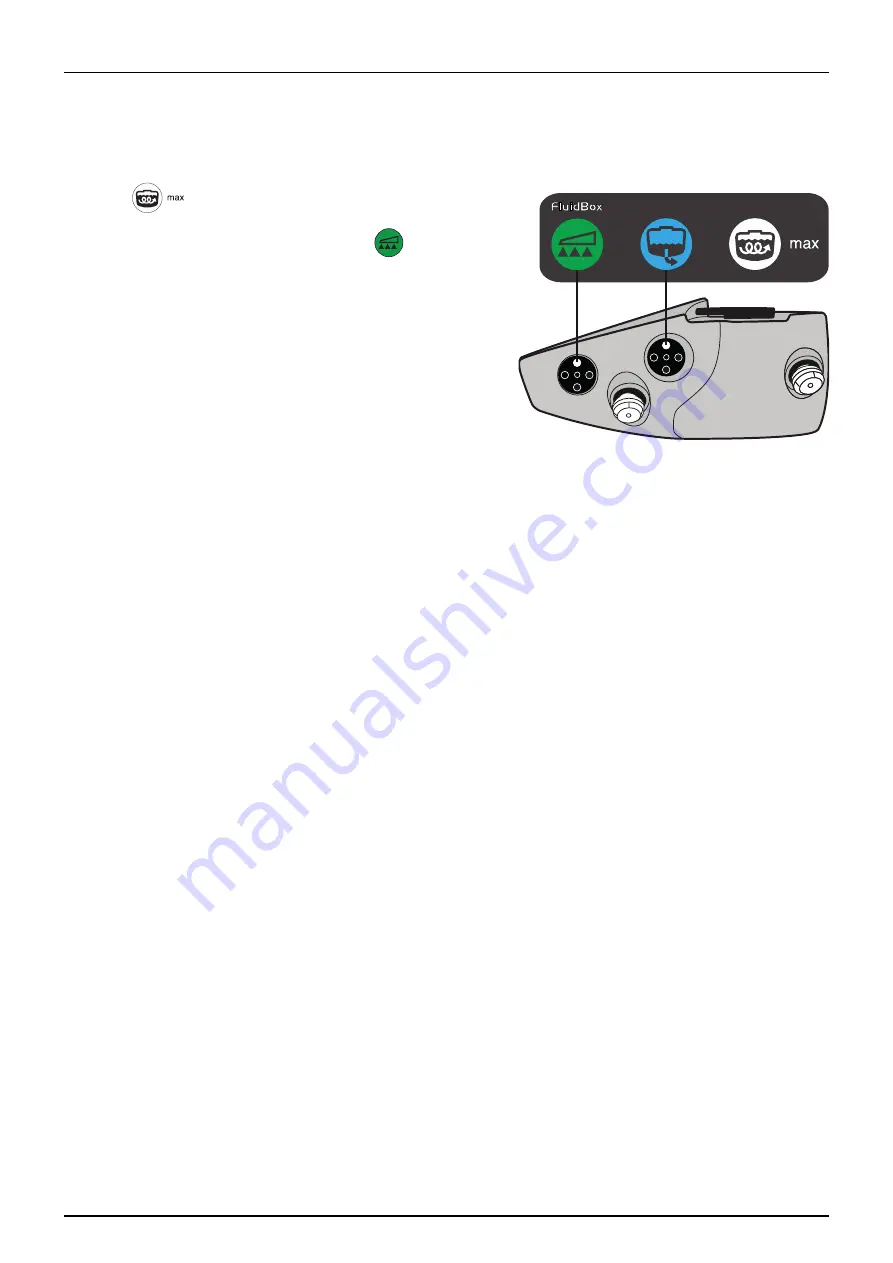
5 - Operation
114
μ
ATTENTION! If the suction SmartValve is not shifted to suction from a clean water supply, the hopper rinsing device
uses spray liquid for rinsing the hopper! Cleaning the TurboFiller must always be done, when the spray job is ended,
and together with cleaning the entire sprayer. A cleaning after the last filling, and before spraying, does not ensure a
clean TurboFiller!
10.
Close the TurboFiller suction valve, when the hopper has been rinsed. Close the lid.
11.
Press
to turn On agitation, or enable AutoAgitation in the
controller.
12.
When the spray liquid is well agitated, press
to turn the
pressure SmartValve towards “spraying” position. The agitation
continues during spraying of the crop.
μ
ATTENTION! If foaming is a problem, turn down the agitation.
Summary of Contents for NAVIGATOR VPZ
Page 4: ...1 EU Declaration 4...
Page 72: ...3 Description 72...
Page 135: ...6 Maintenance 135 Lubrication Plan Boom Wings 10...
Page 174: ...6 Maintenance 174...
Page 182: ...7 Fault Finding 182...
Page 195: ...8 Technical Specifications 195 Hydraulic Diagrams Hydraulics for Boom of 21 24 Meters...
Page 196: ...8 Technical Specifications 196 Hydraulics for Boom of 27 28 Meters...
Page 198: ...8 Technical Specifications 198...
Page 204: ...HARDI INTERNATIONAL A S Herthadalvej 10 DK 4840 N rre Alslev DENMARK...