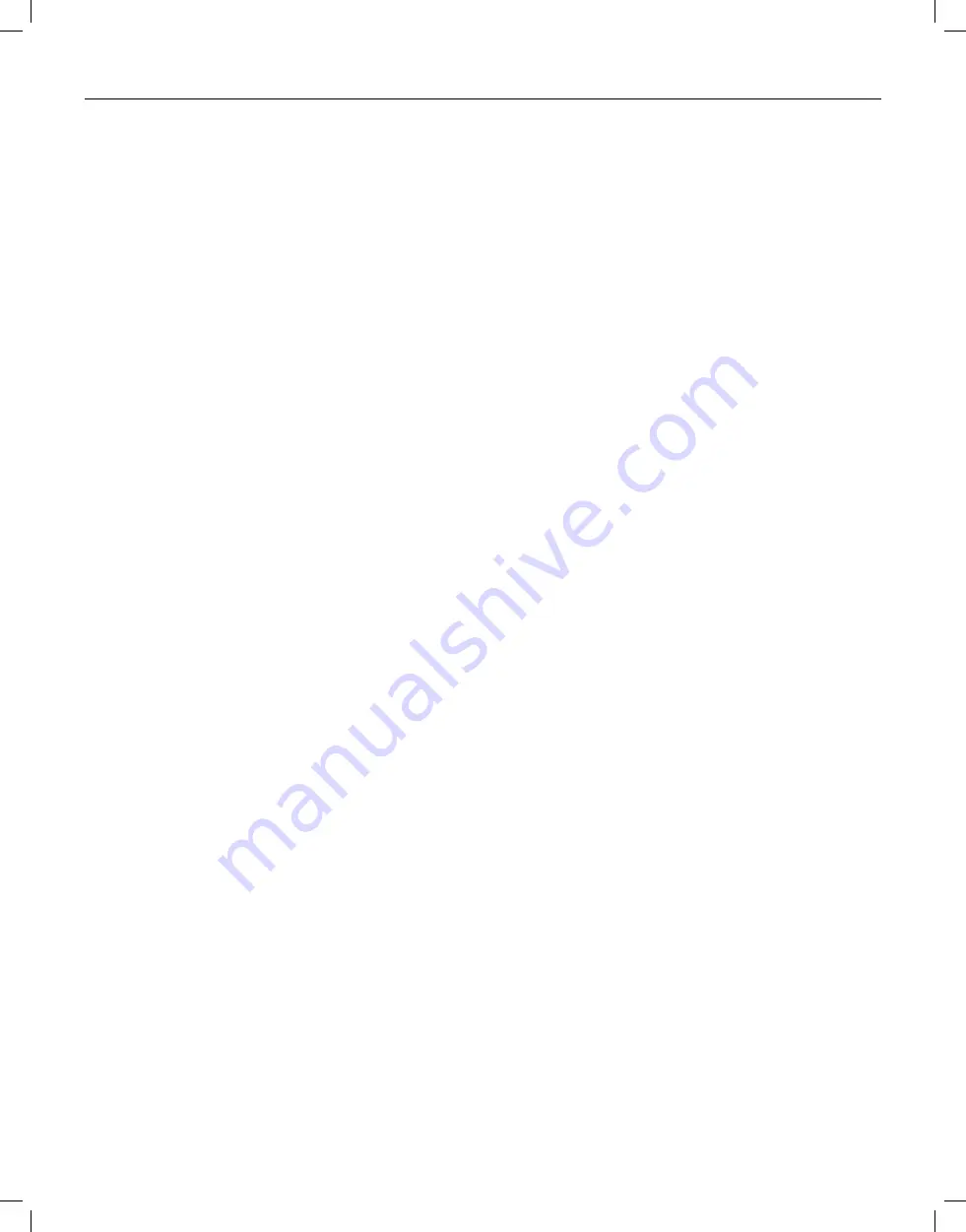
25
APP-001f
SEPT 2016
PLC TIMEOUT
This message means that the APPT Touchscreen is not
communicating with the APPT PLC.
REASON 1:
The cable from the display is not connected
to the PLC. The cable is shipped disconnected to make
it easier to wire the purge points during initial installation.
After the purge points are wired, the cable should be
connected to the PLC.
Action:
Connect the cable if disconnected.
REASON 2:
DIP switches on the PLC are in the wrong
positions.
Check:
The four DIP switches on the PLC should be:
1-on, 2-off, 3-on, 4-off.
Action:
Move the switches to the correct positions.
REASON 3:
The PLC is defective.
Check:
On the PLC, lower right corner, there are 3 LEDs,
PWR/CPU/LOW BATTERY. Check that the PWR and CPU
LEDs are ON.
Action:
If these lights are not on, try turning the purger
off then back on. If this does not restart the PLC, replace
the PLC.
PURGER TURNS-OFF DUE TO BLOWN FUSE
This is the result of a short circuit either on the purger
itself, or from a shorted purge point solenoid. To isolate
the short circuit, turn off power to the APPT, disconnect
all modules on the PLC, replace the 2A or 3A fuse if
necessary, and perform the following.
REASON 1:
A short circuit on the APPT sensors.
Check:
Reconnect the PLC module for temperature, and
verify the fuse does not blow. Reconnect the PLC module
for the milliamp circuits, and verify the fuse does not
blow. Reconnect the PLC module for the level sensors,
and verify the fuse does not blow. If the fuse does blow,
the location of the short circuit is located.
Action:
Replace the shorted sensor. See also Caution
section, page 28.
REASON 2:
A short circuit on the APPT solenoid coils.
Check:
Reconnect the PLC module for the APPT solenoid
coils, and verify the fuse does not blow. If the fuse does
blow, one of the solenoid coils on the purger, or the heater
relay is shorted.
Action:
Replace the shorted solenoid coil or relay.
REASON 3:
A shorted purge point solenoid coil.
(This step is not applicable to model APPTC.)
Check:
Reconnect the PLC module(s) for the purge point
solenoid coils. Press the PURGE POINT ADV button to
sequence through each purge point, and verify the fuse
does not blow. If the fuse does blow, that purge point
solenoid coil is shorted.
Action:
Replace the shorted purge point solenoid coil.
SERVICE REQUIRED OR ERROR HEATER FAULT
The Touchscreen will indicate “SERVICE REQUIRED” or
“ERROR HEATER FAULT” when there is a fault detected
within the “CONCENTRATING WATER” mode. The APPT
will be locked from operation until the fault is rectified.
Liquid solenoid will energize to ensure a safe condition.
REASON 1:
PLC not receiving signal from thermocouple
module.
Check:
Thermocouple module is completely plugged
into PLC.
Action:
Remove thermocouple module to ensure pins
aren’t broken, reinsert the module completely into PLC
confirming it is completely plugged into PLC and green
connector strip is completely plugged into module.
REASON 2:
PLC is reading thermocouple is open or
shorted.
Check:
Measure each thermocouples’ signal prior to wire
connected to module.
Action:
Using a Thermocouple Type J reader, verify
temperature on Touchscreen is within 5° of thermocouple
reader.
REASON 3:
Heater fuse is burned out.
Check:
Measure 15A (115V) or 8A (230V) fuse for continuity.
Action:
Replace fuse appropriately if burned out.
REASON 4:
One or both of the heaters are bad not
providing enough heat to boil ammonia off.
Check:
With APPT de-energized, electrical resistance
of heaters to be 9-10 ohm for 115V APPT, 35-40 ohm for
230V APPT.
Action:
Replace the defective heater if measured
resistance is double the value or both heaters if measured
resistance is open circuit.
REASON 5:
Heater contactor is not closing.
Check:
Measure the voltage at the outlet of contactor,
it should be 115V or 230V depending on purger voltage.
Action:
Replace contactor if bad.
REASON 6:
Capacitors installed with pressure transducers
are missing or bad.
Check:
Capacitors installed across PLC module terminals
50 to 51 and 48 to 51. Remove capacitor, measure 0.1
micro Farad.
Action:
Install if capacitors are missing or bad.
REASON 7:
Bad PLC or module.
Action:
Contact Factory.
SECTION 5 SERVICE, TROUBLESHOOTING, & PARTS