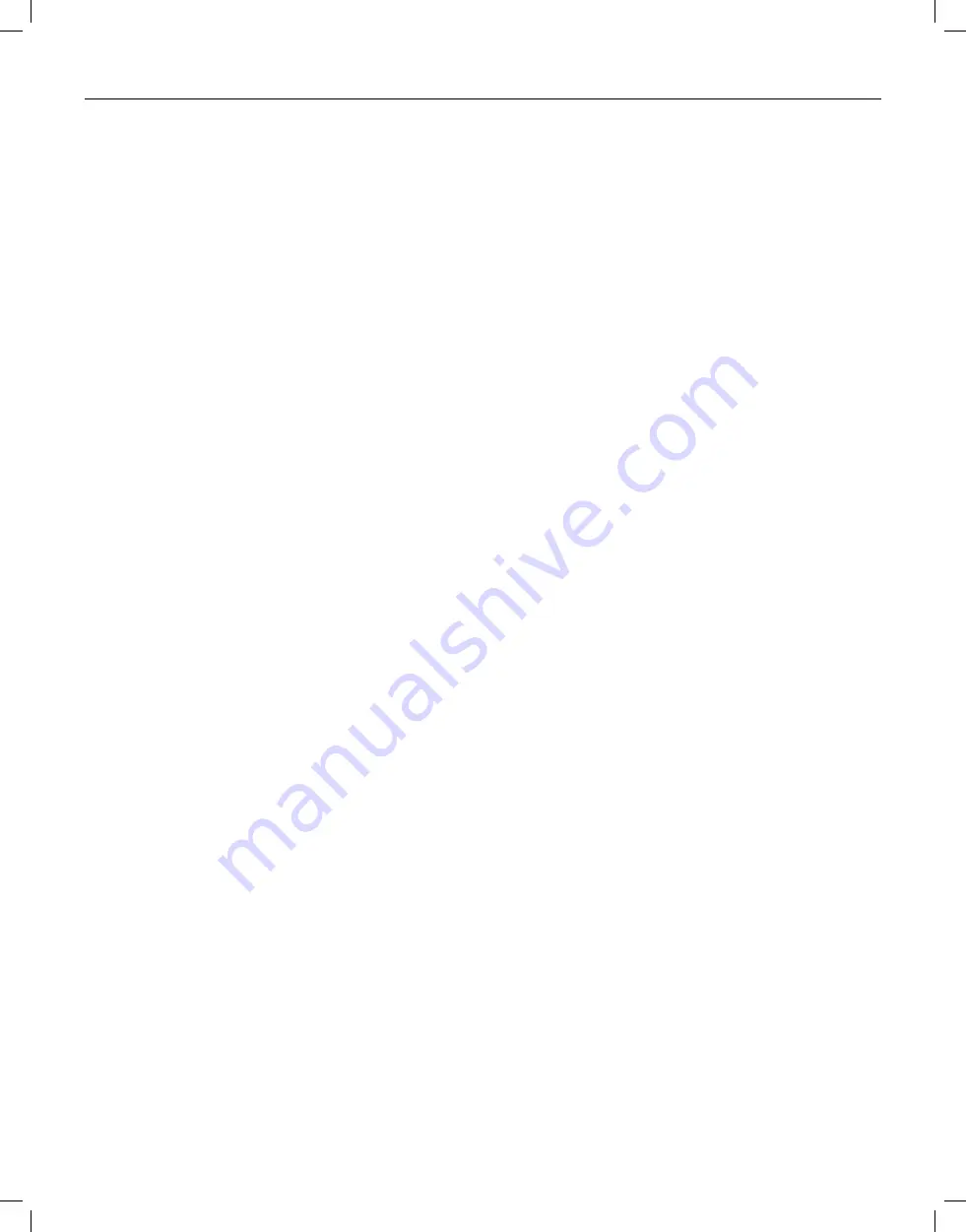
24
APP-001f
SEPT 2016
TOUCHSCREN DISPLAYS 7777
LOSS OF LOW-PRESSURE PUMPED-LIQUID.
If the
liquid line solenoid valve remains energized for more than
30 minutes, it indicates there is insufficient low-pressure
pumped-liquid available to maintain an adequate level in
the flooded evaporator of the purger. The purger will not
purge air until this is corrected.
REASON 1:
Liquid line solenoid valve (B) is not opening
or the seat/orifice is blocked.
Check:
Make sure the liquid line solenoid valve (B) is
energized. If not, check for voltage at the solenoid coil.
Action:
Replace the coil if it is burned-out, otherwise
clean or replace the valve. See also the Caution section
on page 28.
REASON 2:
Liquid line restricted.
Check:
Look for closed shut-off valves in the pumped-
liquid line, plugged strainers, or the plastic shipping cap
still in the liquid line flange.
Action:
Inspect piping for a closed shut-off valve. Open
the shut-off valves, clean the strainer, or remove the
shipping cap. See also the Caution section on page 28.
NONCONDENSIBLES ARE NOT BEING
RELEASED.
(See also page 23;
Touchscreen displays 3333
)
REASON 1:
Noncondensibles not present in system.
Check:
Compare the refrigerant liquid temperature
from condenser exit with the condensing pressure. The
pressure/temperature relationship should be within 2 or
3 psig (0.14 to 0.21 bar).
ACTION:
None at this time.
REASON 2:
Metering valve plugged.
Symptom:
The purger appears to be operating properly,
however, the low-pressure liquid-return line is not frosted.
Action:
Fully open the metering valve to flush out any
particles. Then, close the valve and reopen two turns.
REASON 3:
Foul gas line is flooded with liquid.
Symptom:
The bottom of the liquid drainer often remains
frosted.
Check:
Inspect condenser and foul gas piping. In many
cases, the problem is liquid refrigerant being drawn from
the purge point. To prevent this from happening, select
purge point locations above liquid surfaces and make
sure purge point lines are installed so that only vapor, and
not liquid, can be drawn in. Refer to Piping Instructions
in Section 2 of this bulletin.
Action:
Correct condenser and foul gas piping.
AMMONIA INSTEAD OF NONCONDENSIBLES
RELEASED FROM PURGER.
REASON 1:
Purge gas solenoid valve (C) leaking at seat.
Symptom:
A slow leak of noncondensibles to the bubbler.
Check:
Look for dirt or a worn seat in the purge gas
solenoid valve (C).
Action:
Remove, clean, or replace the solenoid tube
plunger or valve. See also the Caution section on page 28.
REASON 2:
Oil in purger.
Symptom:
No frost around the low side oil drain valve.
Action:
Remove oil through both the low side and high
side drain valves (See Figure 1) per safe refrigeration
procedures. See also the Caution section on page 28.
REASON 3:
Refrigeration compressors are stopped.
Symptom:
After the refrigeration compressors are stopped,
the purger releases ammonia into the water bubbler for
about 1/2 hour until either the 2222 alarm or the 3333
alarm is displayed.
Action:
The purger should not be operated when the
refrigeration compressors are stopped. It is recommended
to install a customer supplied, externally mounted, power
relay to de-energize the purger when the refrigeration
compressors are stopped.
WATER IS NOT BEING RELEASED
REASON 1:
Water not present in system.
Check:
Perform a water analysis of the vessel from which
the low-pressure pumped liquid is supplied. Divide ppm
by 10,000 to convert to percent.
Action:
None at this time.
REASON 2:
The water concentration sensor is defective.
Check:
Press the STATUS button on the Touchscreen
and record the water solution percentage, the evaporator
liquid temperature, and the low side pressure readings.
Compare the evaporator liquid temperature with the low
side pressure reading. The water concentration sensor
should read approximately 2% water for every 1 °F (0.6
°C) that the evaporator liquid temperature is warmer than
the temperature of pure saturated ammonia corresponding
to the low side pressure reading. The evaporator liquid
temperature must be 12 °F (7 °C) warmer than the
temperature of pure saturated ammonia corresponding to
the low side pressure reading before the APPT will enter
CONCENTRATING WATER mode.
Action:
Replace the water concentration sensor if defective.
See also Caution section, page 28.
REASON 3:
The low liquid level sensor is defective or
out of calibration.
Check:
The heaters will not energize, and the APPT will
not release water, if the low liquid level sensor indicates
no liquid is present. Remove the cover of the electrical
enclosure on the low liquid level sensor. The red LED
inside will be on if it senses liquid, and off if it senses
gas. If the sensor has frost where the sensor enters the
vessel, but the red LED is off, the sensor may be defective.
If there is no frost, either no liquid is present, or the
sensor is logged with oil and the oil must be drained. To
recalibrate, ensure liquid level is below level of sensor.
Remove sensor housing cover and turn calibration screw
clockwise slowly till LED illuminates. Then turn screw two
full turns counterclockwise.
Action:
Replace the low liquid level sensor if defective.
See also Caution section, page 28.
SECTION 5 SERVICE, TROUBLESHOOTING, & PARTS