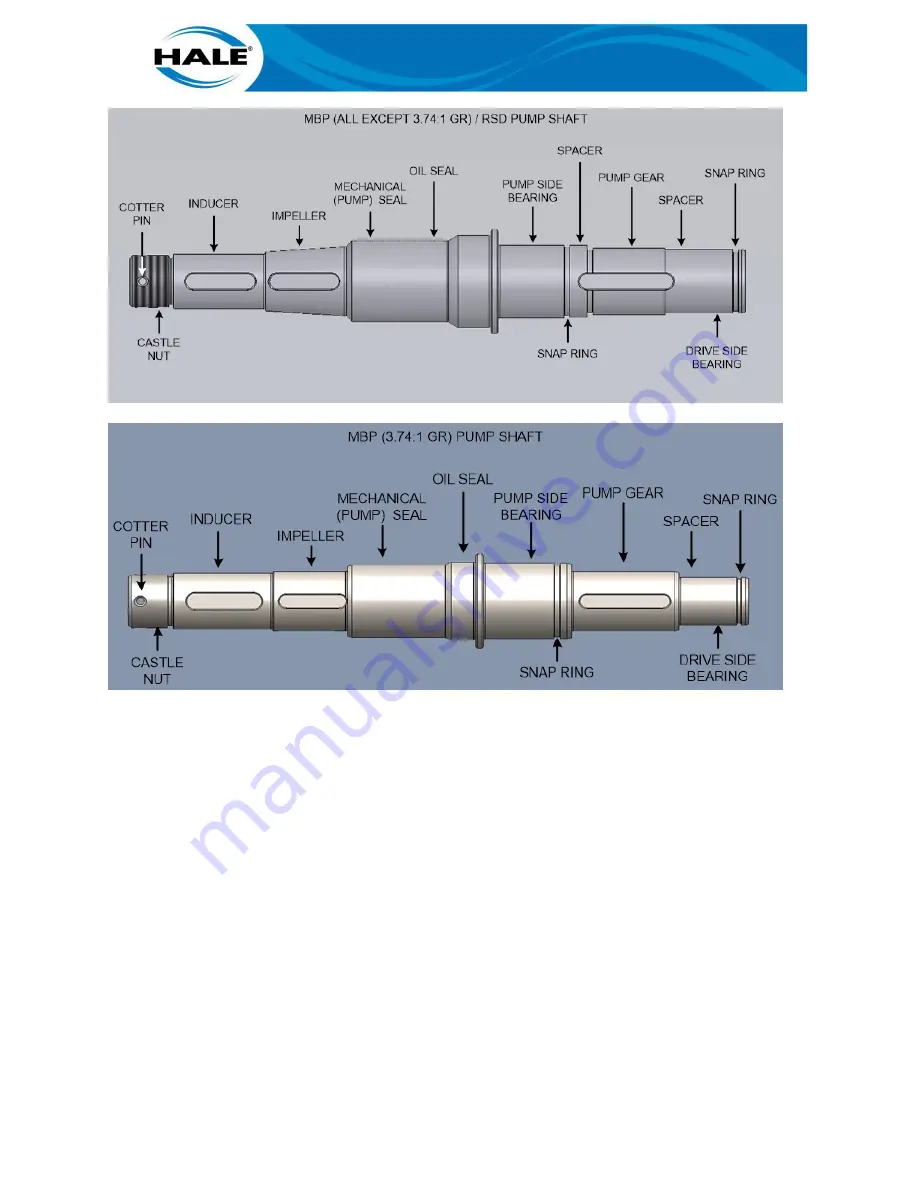
136
Figure 50. MBP/RSD Pump Shaft
A.
Prepare new pump shaft for installation.
Install pump side bearing on pump shaft.
1.
NOTE
The preferred method of assembly is to heat the bearing and cool the pump shaft to
allow a slip fit. Using a bearing heater, heat bearing to 250
℉
(121 °C) (Do NOT ex-
ceed 8 hrs.). Using dry ice in an alcohol bath, cool shaft to –65
℉
(–54 °C) (Do NOT
exceed 1 hr.). Use appropriate PPE to handle/assemble bearing and shaft.
a)
Lubricate pump shaft and bearing center bore with gear oil.
b)
Configure press bolster plate with opening/bore hole or cribbing so shaft passes
thru bearing. (NOTE: The plate must support the inner race to prevent bearing
damage during assembly, bearing-to-shaft is an interference fit.)
c)
Place bearing on press bolster plate.
Summary of Contents for AP
Page 2: ......
Page 28: ......
Page 71: ...59 Figure 19 One Piece Volute AP CBP MBP Figure 20 Three Piece Volute RSD...
Page 73: ...61 Figure 21 AP Pump Exploded View...
Page 74: ...62 Figure 22 CBP Pump Exploded View...
Page 75: ...63 Figure 23 MBP Pump Exploded View...
Page 76: ...64 Figure 24 RSD Pump Exploded View...
Page 77: ...65 Figure 25 Gearbox Exploded View All Except 3 74 1 GR...
Page 78: ...66 Figure 26 Gearbox Exploded View 3 74 1 GR...
Page 158: ...146 THIS PAGE INTENTIONALLY BLANK...
Page 174: ...C 12 THIS PAGE INTENTIONALLY BLANK...
Page 176: ...D 2 DATE HOURS RUN MAINTENANCE PROBLEM PART S USED REASON REPLACED INITIALS...