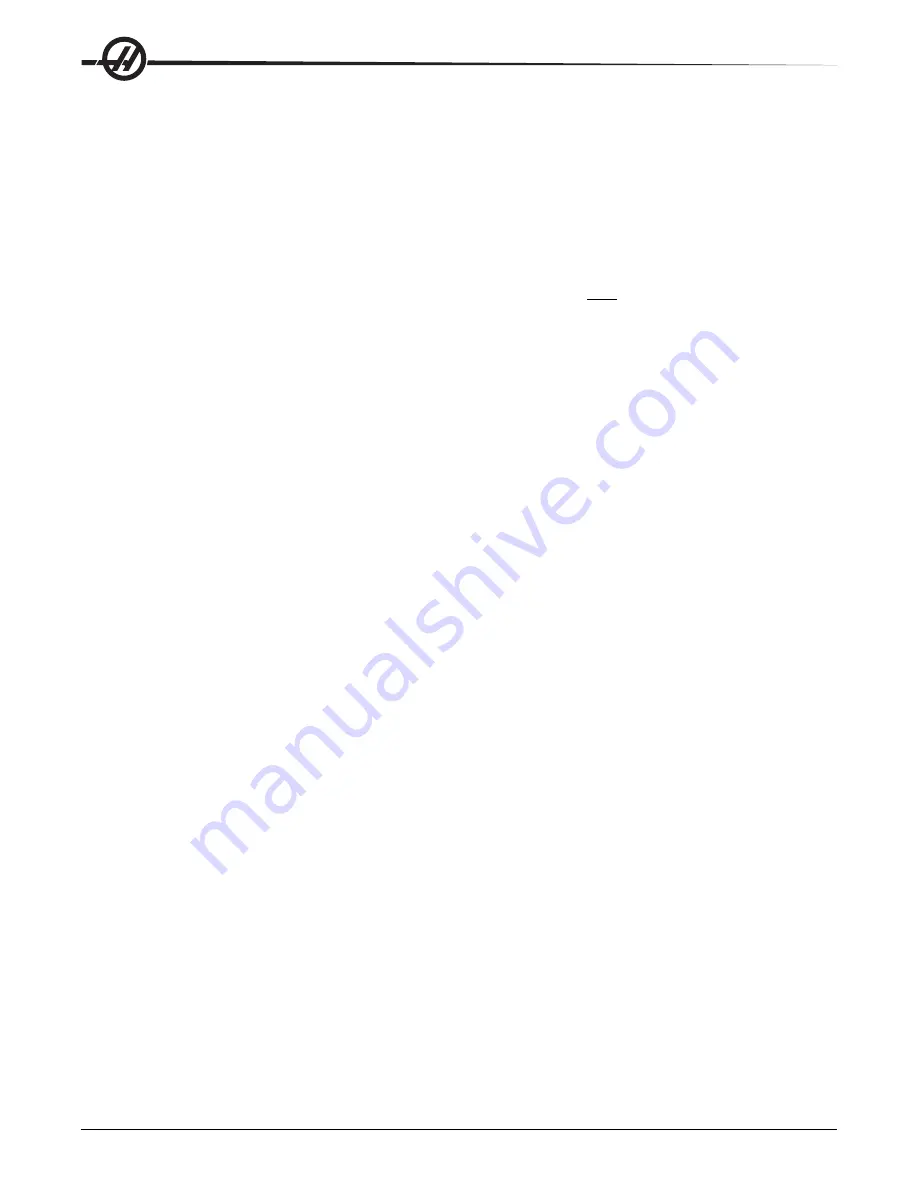
1 0 6
4&5 Axis Programming
96-8000 rev R June 2007
Work coordinate numbers are usually entered as positive numbers.
Work coordinates are entered into the table as a number only. To enter an X value of X2.00 into G54, cursor to the X
column and enter 2.0.
Five-axis Programming Notes
Use a tight synchronization cut across resolution of geometry in the CAD/CAM system will allow smooth flowing
contours and a more accurate part.
Positioning the machine to an approach vector should only be done at a safe distance above or to the side of the
workpiece. When in the rapid mode, the axes will arrive at the programmed position at different times; the axis with
shortest distance from target will arrive first, and longest distance last. A high feed rate will force the axes to arrive
at the commanded position at the same time avoiding the possibility of a crash.
G Codes
Fifth-axis programming is not affected by the selection of inch (G20) or metric (G21); the A and B axes are always
programmed in degrees.
G93 inverse time must be in effect for simultaneous 5-axis motion. In G93 mode, the maximum feed rate will
include the combination of all axis motion in one block of code. The limit is set by the control and looks at encoder
steps programmed for all axes in a block of code.
Limit your post processor (CAD/CAM software) if possible; the maximum speed in G93 mode is 32 degrees per
minute. This will result in smoother motion, which may be necessary when fanning around tilted walls.
M Codes
Important! It is highly recommended that the A/B brakes be engaged when doing any non 5-axis
motion. Cutting with the brakes off can cause excessive wear in the gear sets.
M10/M11 engages/disengages the A-axis brake
M12/M13 engages/disengages the B-axis brake
When in a 4 or 5 axis cut, the machine will pause between blocks. This pause is due to the A and/or B axis brakes
releasing. To avoid this dwell and allow for smoother program execution, program an M11 and/or M13 just before the
G93. The M-codes will disengage the brakes, resulting in a smother motion and an uninterrupted flow of motion.
Remember that if the brakes are never re-engaged, they will remain off indefinitely.
Settings
A number of settings are used to program the 4th and 5th axis. See settings 30, 34 and 48 for the 4th axis and 78,
79 and 80 for the 5th axis.
Setting 85 should be set to .0500 for 5-axis cutting. Settings lower than .0500 will move the machine closer to an
exact stop and cause uneven motion.
G187 can also be used in the program to slow the axes down.
CAUTION! When cutting in 5-axis mode poor positioning and over-travel can occur if the tool length offset (H-code)
is not canceled. To avoid this problem use G90 G40, H00 and G49 in your first blocks after a tool change. This
problem can occur when mixing 3-axis and 5-axis programming; restarting a program or when starting a new job
and the tool length offset is still in effect.
Feed Rates
A feed-rate must be commanded for each line of 4 and/or 5 axis code. Limit the feed-rate to less than 75IPM when
drilling. The recommended feeds for finish machining in 3-axis work should not exceed 50 to 60 IPM with at least
.0500" to .0750" stock remaining for the finish operation.
Rapid moves are not allowed; rapid motions, entering and exiting holes (full retract peck-drill cycle) are not sup-
ported.
When programming simultaneous 5-axis motion, less material allowance is required and higher feedrates may be
permitted. Depending on finish allowance, length of cutter and type of profile being cut, higher feed rates may be
possible. For example, when cutting mold lines or long flowing contours, feedrates may exceed 100 IPM.
Summary of Contents for Mill
Page 12: ...96 8000 rev R June 2007 Safety 5 ...
Page 14: ...96 8000 rev R June 2007 Safety 7 LATHE WARNING DECALS ...
Page 15: ...8 Safety 96 8000 rev R June 2007 ...
Page 17: ...10 Introduction 96 8000 rev R June 2007 ...
Page 117: ...110 4 5 Axis Programming 96 8000 rev R June 2007 ...
Page 199: ...Settings 192 96 8000 rev R June 2007 ...