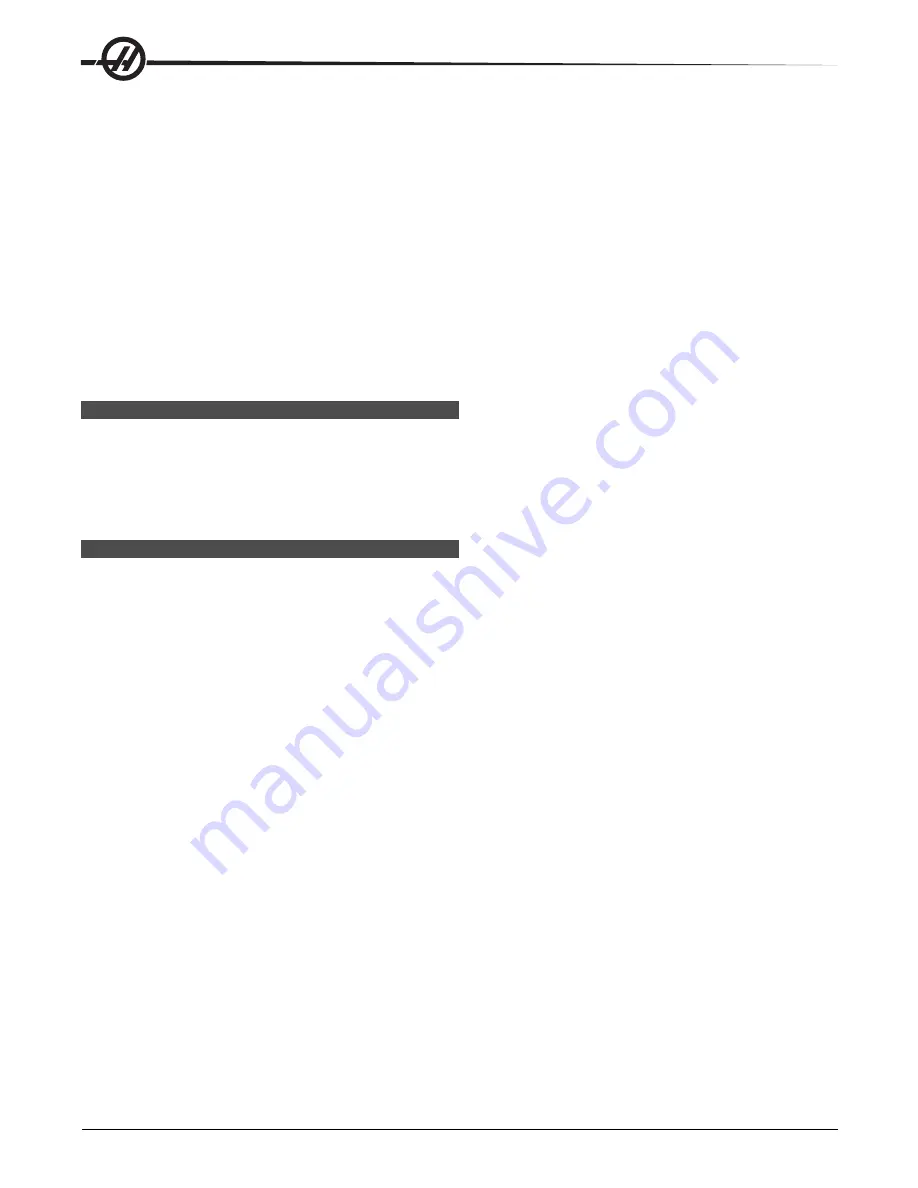
24
Introduction
96-8000 rev R June 2007
Materials
The Milling calculator includes a field called MATERIAL, which, when highlighted, allows the operator to select
a type of material from the list using the left and right arrow keys.
A recommended surface speed and chip load will be displayed based on the material chosen, as shown.
SURFACE SPEED *.*** FT/MIN RECOMMENDED **** TO *****
CHIP LOAD *.*** IN RECOMMENDED *.*** TO *.***
Also, the required horsepower will be calculated and displayed as shown below on the right.
CUT DEPTH *.*** IN REQUIRED POWER *.* HP
When in metric mode, the required power is displayed as KW (kilowatt).
Drill/Tap Chart
Pressing the Help/Calc button a third time displays a Drill and Tap chart
S
PINDLE
W
ARM
-U
P
P
ROGRAM
All spindles, which have been idle for more than 4 days, must be thermally cycled prior to operation. This
warm-up will prevent possible overheating of the spindle due to the settling of lubrication. A 20-minute warm-up
program (number O02020) has been supplied with the machine which will bring the spindle up to speed slowly,
allowing the spindle to thermally stabilize. This program may also be used daily for spindle warm-up prior to
high-speed use.
R
UN
-S
TOP
-J
OG
-C
ONTINUE
This feature allows the operator to stop a running program, jog away from the part, and then resume program
execution. The following is an operation procedure:
1. Press Feed Hold to stop the running program
2. Press X, Y or Z followed by the Handle Jog button. The control will store the current X, Y, and Z positions.
Note: Axes other than X, Y, and Z cannot be jogged.
3. The control will display the message "Jog Away". Use the jog handle, remote jog handle, jog and jog-lock
buttons to move the tool away from part. Control buttons such as AUX CLNT (optional Through Spindle Coolant
- TSC), or Coolnt to turn on/off the coolant (AUX CLNT requires that the spindle is rotating and the door is
closed). The spindle can be controlled by pressing CW, CCW, Stop, Tool Release. If necessary, tool inserts
can be changed. Caution: When the program is continued, the old offsets will be used for the return position.
Therefore, it is unsafe and not recommended to change tools and offsets when the program is interrupted.
4. Jog to a position as close as possible to the stored position, or to a position where there will be an unob-
structed rapid path back to the stored position.
5. Return to the previous mode by pressing MEM, MDI, or DNC. The control will only continue if the mode that
was in effect when stopped is re-entered.
6. Press Cycle Start. The control will display the message Jog Return and rapid X and Y at 5% to the position
where Feed Hold was pressed, then return the Z-axis. Caution: The control will not follow the path used to jog
away. If Feed Hold is pressed during this motion, the mill axes motion will pause and display the message "Jog
Return Hold". Pressing Cycle Start will cause the control to resume the Jog Return motion. When the motion is
completed, the control will again go into a feed hold state.
7. Press Cycle Start again and the program will resume normal operation.
Also see Setting 36 Program Restart.
Summary of Contents for Mill
Page 12: ...96 8000 rev R June 2007 Safety 5 ...
Page 14: ...96 8000 rev R June 2007 Safety 7 LATHE WARNING DECALS ...
Page 15: ...8 Safety 96 8000 rev R June 2007 ...
Page 17: ...10 Introduction 96 8000 rev R June 2007 ...
Page 117: ...110 4 5 Axis Programming 96 8000 rev R June 2007 ...
Page 199: ...Settings 192 96 8000 rev R June 2007 ...