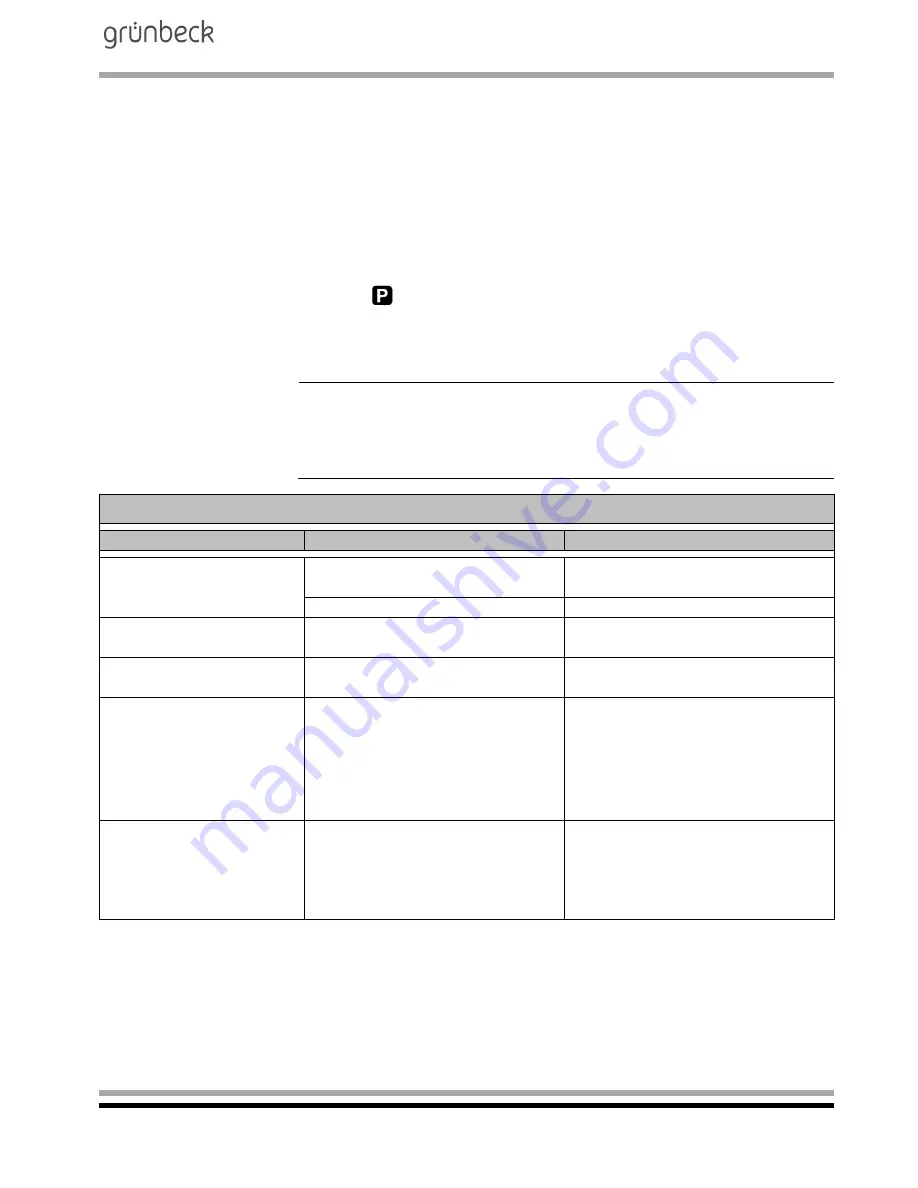
Reverse osmosis system
AVRO 125 TS/TL
Order no. 185 752 945-inter Edited by: nkes-mrie :\BA-752945-INTER_185_AVRO_125.DOCX
41
G Troubleshooting
Even carefully designed and manufactured technical systems that are
operated properly, can experience malfunctions. Table G-1 provides
an overview of possible problems that can occur during the operation
of the systems and indicates the causes and their elimination.
The systems are equipped with an error detection and reporting
system. If an error message is displayed:
1. Press button (= acknowledge malfunction).
2. Watch the display.
If the message reappears, compare it with table G-1.
3. If necessary, notify Grünbeck’s technical customer service.
Note:
In the case of malfunctions which cannot be remedied with the
information in Table G-1, it is essential to contact the customer service
(refer to www.gruenbeck.de)! Enter the system designation, serial
number and, if necessary, fault signal in the display.
Table G-1: Troubleshooting
This is what you observe
This is the cause
This is what to do
Water quality deteriorated
by 50 %.
Membrane clogged.
Replace or flush the membrane
1)
.
Feed water values deteriorated.
Check feed water values.
Solenoid valve does not
open
.
Coil defective or fuse on the
circuit board blown.
Replace coil or fuse.
Solenoid valve does not
close
.
Valve contaminated.
Clean valve.
Bar appears in the
display above Symbol
Close.
HP pump: Thermostat contact
has responded, pump has
overheated.
Upstream hardness
monitoring or water treatment
blocks the system.
Wait until the pump has cooled
down again, the system will
then automatically continue to
produce.
Inspect system installed
upstream.
Bar appears in the
display above screw
wrench symbol (without
further indications of a
malfunction).
Service interval has elapsed.
Have maintenance performed.