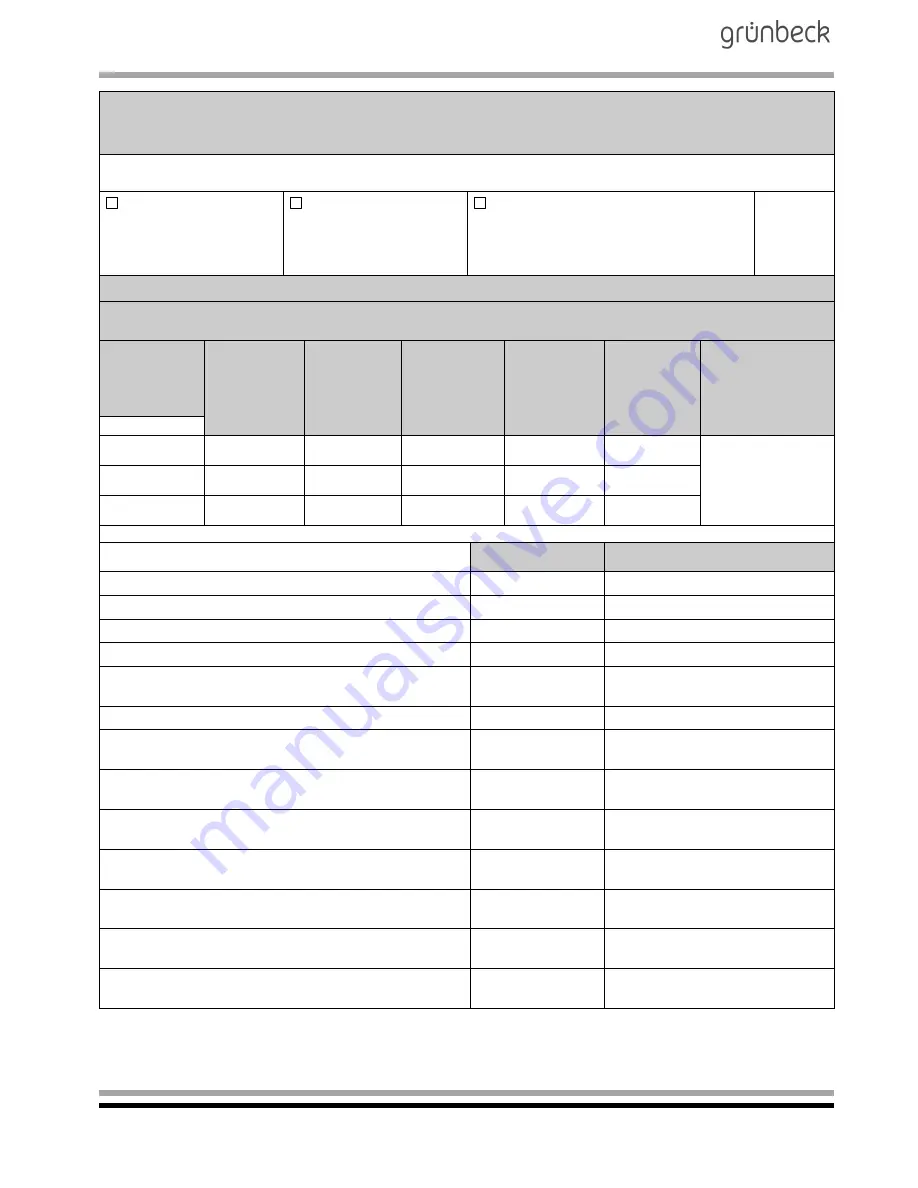
Reverse osmosis system
AVRO 125 TS/TL
Order no. 185 752 945-inter Edited by: nkes-mrie G:\BA-752945-INTER_185_AVRO_125.DOCX
56
Maintenance work on reverse osmosis system AVRO 125 TS/TL
Checklist
Please enter measured values. Confirm checks with OK or enter repair work performed.
Maintenance performed
without
replacement of
module
Maintenance performed
with
replacement of
module
Maintenance performed
with
replacement of AVRO treatment module
Module
no.
.........................
Treatment module no. .............................
Measured values
Water volumes and water qualities
before
the replacement of the module /
after
the replacement of the module or
in case of maintenance
Pump
pressure
[bar]
Conductivity
[
S/cm]
Total
hardness
[
dH]
1)
Carbonate
hardness
[°cH]
2)
Temperature
[
C]
Volume flow
[l/h]
Recovery
[%]
before/after
before/after before/after before/after before/after before/after
before/after
/
Feed water
/
/
/
/
/
Permeate / / /
/ /
Concentrate
/
/
/
/
/
. . . . . % / . . . . . %
Acknowledgement
Remarks
Water meter reading upstream of the system
[m³]
Inlet water pressure (2.5 - 4 bar) checked
Filter element replaced (80 µm / 5 µm)
Settings of electronics checked
Remaining AVRO maintenance interval
(chapter F 2.1)
[h]
Operating hours (chapter F, 2.1)
Run time of high-pressure pump
(code 245, par.
c
)
[h]
Run time of pressure booster pump
(code 245, par.
d
)
[h]
Permeate volume produced
(code 245, par.
E
)
[m³]
Concentrate volume generated
(code 245, par.
F
)
[m³]
Blended water quantity
(code 245, par.
G
)
[m³]
AVRO treatment current intensity
(code 245, par.
I
)
[mA]
Error memory
(code 245, par.
1..9
)
[Er]
1)
1°dH = 1.78°f = 0.178 mmol/l
2)
1°cH = 0.36 mmol/l