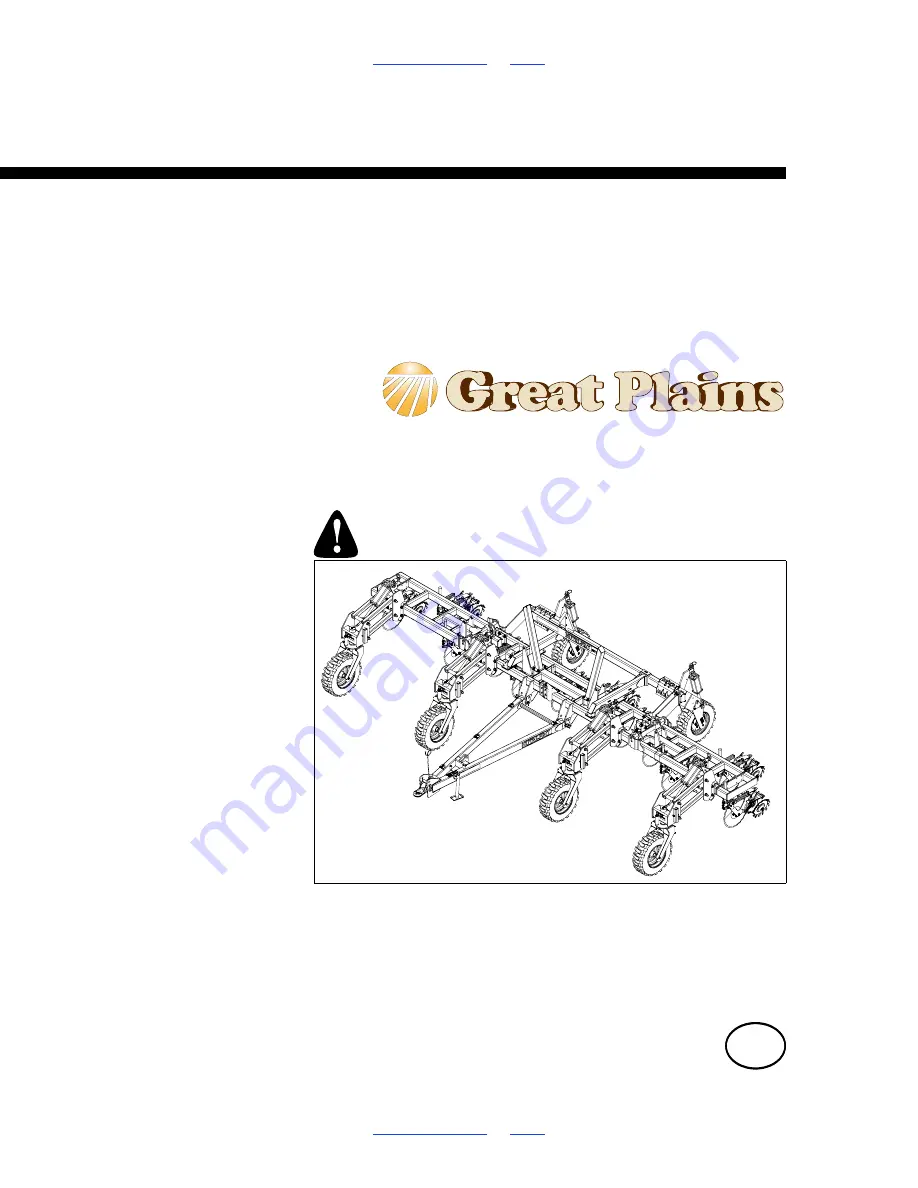
Manufacturing, Inc.
www.greatplainsmfg.com
© Copyright 2019
Printed 2019-03-11
407-502M
EN
ORIGINAL INSTRUCTIONS
Operator Manual
Nutri-Pro
®
NP30A and NP40A
30- and 40-Foot NH
3
(Anhydrous Ammonia)
Applicators
Read the operator manual entirely. When you see this symbol, the
subsequent instructions and warnings are serious - follow without
exception. Your life and the lives of others depend on it!
Illustrations may show optional equipment not supplied with standard unit, or
may show NP30L, NP40L or NP3000 models where the topic function is
identical.
38809