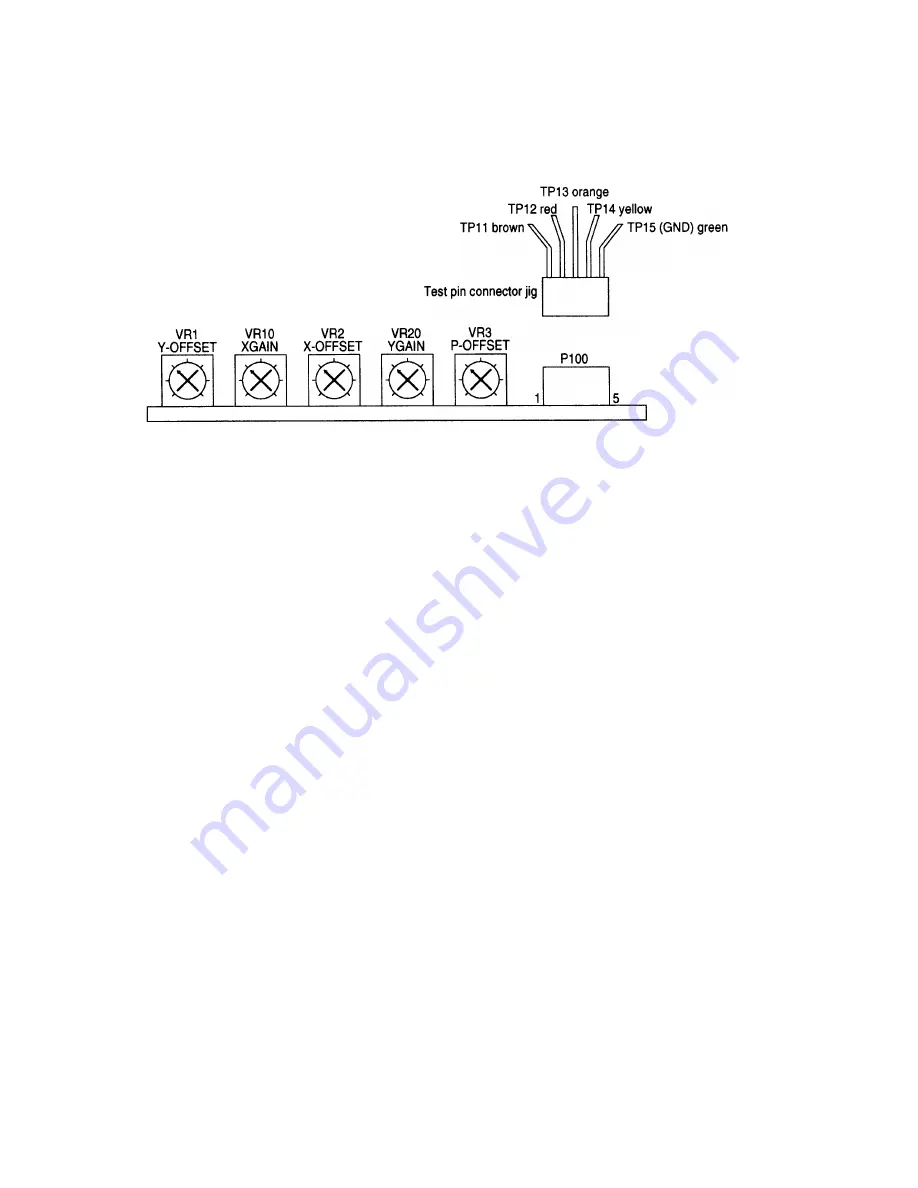
FC3100-60 Service Manual
P/N53802-031T Rev. A
5 - 6
5.6 Default Trimmer Settings
Before turning the plotter back on, set each of the main board's trimmers as indicated below.
VR1 (Y-OFFSET)
: Trimmer for adjusting the Y motor offset
VR2 (X-OFFSET)
: Trimmer for adjusting the X motor offset
VR3 (P-OFFSET)
: Trimmer for adjusting the pen offset
VR10 (X-GAIN)
: Trimmer for adjusting the X motor gain
VR20 (Y-GAIN)
: Trimmer for adjusting the Y motor gain
Brown : TP11
Red
: TP12
Orange : TP13
Yellow : TP14
Green
: TP15 (GND)
Summary of Contents for CUTTING PRO FC3100-60
Page 10: ...FC3100 60 Service Manual P N53802 031T Rev A 1 6 FC3100 60 with Stand Option Unit mm...
Page 18: ...FC3100 60 Service Manual P N53802 031T Rev A 2 8 Sample printout by the CONDITION function...
Page 113: ...FC3100 60 Service Manual P N53802 031T Rev A 5 17 CONDITION 4...
Page 131: ...FC3100 60 Service Manual P N53802 031T Rev A 8 2 Mainframe...
Page 133: ...FC3100 60 Service Manual P N53802 031T Rev A 8 4 Y Drive Section...
Page 135: ...FC3100 60 Service Manual P N53802 031T Rev A 8 6 X Drive Section...
Page 137: ...FC3100 60 Service Manual P N53802 031T Rev A 8 8 Push Roller Arm and Y Rail Section...
Page 140: ...FC3100 60 Service Manual P N53802 031T Rev A 8 11 Pen Block and Y Slider Section...
Page 142: ...FC3100 60 Service Manual P N53802 031T Rev A 8 13 Chassis Section...
Page 144: ...FC3100 60 Service Manual P N53802 031T Rev A 8 15 Film Stocker Section...
Page 147: ...FC3100 60 Service Manual P N53802 031T Rev A 8 18 Stand and Media Basket Option...
Page 149: ...FC3100 60 Service Manual P N53802 031T Rev A 8 20 Pouncing Tool Option...
Page 151: ...FC3100 60 Service Manual P N53802 031T Rev A 9 2 Wiring Diagram...
Page 153: ...FC3100 60 Service Manual P N53802 031T Rev A 9 4 Main Board Wiring Diagram...
Page 154: ...FC3100 60 Service Manual P N53802 031T Rev A 9 5 Main Board Interface Section...
Page 155: ...FC3100 60 Service Manual P N53802 031T Rev A 9 6 Main Board CPU Section...
Page 156: ...FC3100 60 Service Manual P N53802 031T Rev A 9 7 Main Board Memory Section...
Page 157: ...FC3100 60 Service Manual P N53802 031T Rev A 9 8 Main Board 1MB Buffer Section...
Page 158: ...FC3100 60 Service Manual P N53802 031T Rev A 9 9 Main Board GRC1504 Section...
Page 159: ...FC3100 60 Service Manual P N53802 031T Rev A 9 10 Main Board Clock Section...
Page 160: ...FC3100 60 Service Manual P N53802 031T Rev A 9 11 Main Board Reset Section...
Page 161: ...FC3100 60 Service Manual P N53802 031T Rev A 9 12 Main Board Driver Section Diagram...
Page 162: ...FC3100 60 Service Manual P N53802 031T Rev A 9 13 Main Board Motor DAC Section...
Page 163: ...FC3100 60 Service Manual P N53802 031T Rev A 9 14 Main Board Motor Drive Section...
Page 164: ...FC3100 60 Service Manual P N53802 031T Rev A 9 15 Main Board A D Section...
Page 165: ...FC3100 60 Service Manual P N53802 031T Rev A 9 16 Main Board Pen DAC Section...
Page 166: ...FC3100 60 Service Manual P N53802 031T Rev A 9 17 Main Board Pen Drive Section...
Page 167: ...FC3100 60 Service Manual P N53802 031T Rev A 9 18 Main Board Input and Output Section...
Page 168: ...FC3100 60 Service Manual P N53802 031T Rev A 9 19 Main Board Connector Section 1...
Page 169: ...FC3100 60 Service Manual P N53802 031T Rev A 9 20 Main Board Connector Section 2...
Page 171: ...FC3100 60 Service Manual P N53802 031T Rev A 9 22 Interconnection Board...
Page 173: ...FC3100 60 Service Manual P N53802 031T Rev A 9 24 Pen Board...
Page 175: ...FC3100 60 Service Manual P N53802 031T Rev A 9 26 Sheet Switch Control Panel...